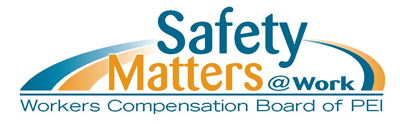


Workplace Inspections
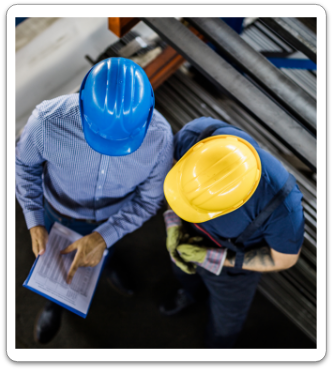
[OHS General Regs., S. x] Follow these links
to related legislation.
Highlighted words reveal
definitions and supplementary
information when selected.
Workplace inspections are a critical component of an occupational health and safety program. By examining the workplace for hazards and recording your findings, a plan for prevention can be created. The overall goal of an inspection is to listen to the concerns of workers, gain a further understanding about the jobs and tasks, and identify existing and potential hazards. After analysis, actions can be taken to resolve the issue to prevent accidents, injuries, or illnesses.
Employer Duties
When 20 or more workers are regularly employed, the employer must establish an occupational health and safety program [OHS Act, S. 23], which includes a system that monitors occupational health and safety matters and makes sure that there is prompt follow-up and control of any hazards that are identified. [OHS Act, S. 23 (3)(f)] The employer must also have a system for promptly investigating incidents and complaints. This system will assist in identifying hazards that should be regularly inspected. [OHS Act, S. 23 (3)(g)] Employers must also maintain records and statistics of inspections. [OHS Act, S. 23 (3)(h)]
Joint Occupational Safety and Health (JOSH) Committee or Representative Duties
A JOSH Committee can help plan, conduct, report and monitor workplace inspections.
The JOSH committee or representative must:
- participate in inspections that relate to the health and safety of workers; [OHS Act, S. 25 (7)(c)] [OHS Act, S. 26 (6)(c)]
- assist by helping to promptly deal with issues about health and safety; and [OHS Act, S. 25 (7)(b)] [OHS Act, S. 26 (6)(b)]
- make recommendations to the employer, worker or any other person, as required. [OHS Act, S. 25 (7)(f] [OHS Act, S. 26 (6)(f)]
General Inspection Steps
General steps when conducing a workplace inspection include:
- Timing – Plan when the inspections will take place. Will inspections be announced, random or both?
- Establish the inspection team – Who will be on the inspection team (e.g., committee members or representative? Workers? Supervisor? Management?) Will there be a team lead? Does the inspection team need training?
- Plan your inspection – Will the team inspect the entire workplace or certain areas? Use a site diagram, checklist or both to help make sure the inspection team does not miss an area, task or item. Review past inspections, or the results of a job hazard analysis, to ensure that corrective action has been taken on previously identified items.
- Thoroughly inspect the workplace – Look for who, what, where, when, and how. Think about how a small change might impact the safety of a worker. Will constant impact, vibration, heat, corrosion, or wear develop into an unsafe condition?
- Ask questions - Examine the workers, work environment, equipment, the processes, and how these elements interact. Ask the workers performing the task if they have concerns. These are the people who know their job task best.
- Review the inspection results - Identify where corrective action is needed and make recommendation on who or how these changes will take place. Analyse other inspection reports to identify trends and priorities, and where improvements can be made.
Hazard categories to look for during the inspection include:
- Safety - inadequate machine guards, unsafe workplace conditions, unsafe work practices, etc.
- Biological - organisms such as viruses, bacteria, fungi and parasites.
- Chemical - solid, liquid, vapour, gas, dust, fume or mist.
- Ergonomic - physiological demands on the worker such as repetitive and forceful movements, awkward postures, and improperly designed workstations, tools, and equipment.
- Physical – sources of energy such as noise, vibration, energy, weather, heat, cold, electricity, radiation, and pressure.
- Psychosocial hazards – psychological demands on the worker and their mental health, such as stress, bullying, or violence.
Specific inspection situations
Specific situations where inspection is required on PEI include:
- All safety equipment used in a confined space must be inspected by a competent person before use. [OHS General Regs., S. 13.3(m)]
- Ladders must be inspected before use. [OHS General Regs., S. 23.3]
- After explosive blasts have been fired, inspect that no unexploded charges remain in the holes [OHS General Regs., S. 26.37], and the person in charge of firing must inspect the site to give clearance before other workers are allowed to return to work. [OHS General Regs., S. 26.58]
- Tools must be inspected by their owners and users before being used. [OHS General Regs., S. 29.2] [OHS General Regs., S. 29.5]
- Power tools and their electrical cords must be inspected at regular intervals. [OHS General Regs., S. 29.6]
- Machinery must be inspected for defects [OHS General Regs., S. 30.3], including all power-operated machinery being inspected each day before operation, as practicable. [OHS General Regs., S. 31.1]
- Hoisting apparatus must be inspected according to required standards. [OHS General Regs., S. 34.2], and that the operator will visually inspect before use to verify the hoisting apparatus is in safe working order. [OHS General Regs., S. 34.6(3)]
- Welding and cutting torches, their fittings and regulators must be inspected before each use. [OHS General Regs., S. 37.11]
- Wires, ropes, slings and fittings must be inspected at regular intervals when used in logging operations. [OHS General Regs., S. 41.4]
- Ice roads, when over water, must be inspected daily to make sure the road is strong enough to carry any load expected to be hauled over it. [OHS General Regs., S. 41.44]
- Bridges on a haul road constructed by the employer must be inspected on a regular basis. [OHS General Regs., S. 41.45]
- Vehicles used in logging must be inspected before each work shift. [OHS General Regs., S. 41.60]
- Drums and barrels that were used for hazardous liquids and are now intended for other uses must be closely inspected for leaks and other defects. [OHS General Regs., S. 43.24]
- Carboys and their baskets or boxes must be examined before they are filled. [OHS General Regs., S. 43.30]
- Respirators must be inspected according to the specified standard. [OHS General Regs., S. 49.15]
- Asbestos that has been encapsulated must be inspected for potential fibre release. [OHS General Regs., S. 49.20]
Workers Duties
Workers can assist an inspection by
- discussing their concerns with the inspection team;
- being a member of the JOSH committee or a representative; and
- reporting concerns, including identified hazards, to their supervisor, or the JOSH committee or representative.
General Regulations
EC180/87
Part 13 CONFINED SPACE
Section 13.3 Hazardous confined space, conditions for entry
13.3 The employer shall ensure that a confined space in which there exists or is likely to exist
(a) a hazardous accumulation of gas, vapour, dust, mist, smoke or fumes; or
(b) an oxygen content of less than 19.5% or more than 23% at atmospheric pressure
is entered only when
(c) the requirements of section 13.2 and clause 13.5(a) are complied with;
(d) the space is purged and ventilated to provide a safe atmosphere; and
(e) provisions for continuous or periodic monitoring have been established to ensure that the hazardous condition does not recur;
(f) another worker is stationed outside the confined space;
(g) the worker entering the space is using such other equipment as is necessary to ensure his safety;
(h) suitable arrangements have been made to remove the worker from the confined space should it be required;
(i) a person adequately trained in cardiopulmonary resuscitation is conveniently available;
(j) the worker entering is using a CSA approved respirator, as specified in section 45.18;
(k) the worker entering the space is wearing an approved safety harness with attached life line that will permit that worker to be removed from the space; if more than one worker is working in the space, steps have been taken to ensure that the life lines do not become entangled;
(l) another worker is stationed outside the confined space and in addition, equipment and persons are available to ensure immediate removal of workers within the space;
(m) all safety equipment to be used in the confined space has been inspected by a competent person and is in good working order.
[EC2021-126, ss. 3, 21; EC2024-600, s. 12]
Part 23 LADDERS
Section 23.3 General obligations
23.3 The user of a ladder shall
(a) inspect a ladder before use;
(b) report any unsafe condition of the ladder to the employer;
(c) not work from the top three rungs of a single or extension ladder;
(d) not lash or splice ladders together;
(e) not place a ladder in front of or against a door unless the door is blocked in the open position, locked or guarded;
(f) use both hands and face the ladder when ascending or descending;
(g) when standing on a ladder, keep the centre of his body between the side rails.
Part 26 EXPLOSIVES
Section 26.37 Inspection
26.37 After blasts have been fired, a thorough examination shall be made to ascertain that no unexploded charges remain in holes.
Section 26.58 Inspection and clearance
26.58 A worker in charge of firing explosive charges shall make a thorough inspection of the site after a charge has been fired and give clearance before other workers are allowed to return to work.
[EC2021-126, s. 3]
Part 29 HAND TOOLS AND PORTABLE POWER TOOLS
Section 29.2 Responsibilities of owner for tools
29.2 The owner of a tool shall ensure that the tool
(a) is of good quality material appropriate for the intended use;
(b) is inspected before being used and repaired or replaced if necessary;
(c) is maintained in safe working condition;
(d) is equipped with adequate devices to ensure a secure hand grip;
(e) has smooth handles without splinters or sharp edges, firmly attached to the tools so as to prevent them from becoming loose;
(f) is of a non-sparking type where there is risk of an explosive atmosphere;
(g) has a proper storage place or facility to store or guard the tool when not in use at the place of employment.
Section 29.5 Responsibilities of user
29.5 Without limiting the generality of the duties under section 29.4 every user shall
(a) inspect tools before use;
(b) not use defective tools;
(c) report the existence of defective tools to the employer;
(d) maintain tools in safe working condition;
(e) use tools only for the specific purposes for which they were designed;
(f) place tools in safe suitable containers when not in use;
(g) ensure that tools are not left lying on floors, passageways, stairways or in other places where persons work or are likely to work or pass, or on elevations from which they may fall on persons below;
(h) ensure that sharp edged or sharp pointed tools are provided with protection for the edges or points when not in use;
(i) carry tools in a way that does not interfere with their using both hands on the ladder or while climbing a structure or on any hazardous work requiring the use of both hands;
(j) pass tools from one person to another in a safe manner;
(k) hold with a holding tool or other suitable device all chisels, drills, etc., which are held by one worker and struck by another; and the worker holding the tool shall place himself where he will be in the least danger of being hit by the hammer if it should glance off the tool or if the handle should break;
(l) keep all axes sharp and not use an axe as a mall or wedge;
(m) clear away interfering objects before swinging an axe;
(n) lay crowbars or pinchbars flat in safe places when not in use and not leaning against a flat surface;
(o) keep points or edges of crowbars or pinchbars in good condition to minimize slipping hazards;
(p) keep corrugations on the jaws of pipe wrenches sharp;
(q) use proper size wrenches and spanners when tightening or loosening nuts and bolts;
(r) discard or remove from service till repaired any wrenches with spread, battered or cracked jaws, cracked or broken handles or other defects;
(s) not carry edged or pointed tools such as screwdrivers, chisels, etc., in pocket;
(t) not use pipe or other extensions on wrenches or spanners unless the tools are designed for use in this manner;
(u) not chop towards their feet or legs with an axe.
[EC2021-126, s. 3]
Section 29.6 Responsibilities of employer, power tools
29.6 The employer shall ensure that
(a) portable power tools shall be inspected at regular intervals and any defective tools shall be removed from service until repaired;
(b) power tools shall be cleaned with a non-flammable non-toxic solvent;
(c) all electrically powered tools shall be properly grounded or of the double insulated type;
(d) electric cords used on power tools shall be inspected periodically and repaired or replace where necessary;
(e) electric cords and air lines used on power tools shall be suspended over aisles or work areas, where possible, to eliminate stumbling or tripping hazards;
(f) drill steel used for pneumatic hammers shall be sharpened and tempered in accordance with manufacturer's specifications.
Part 30 MECHANICAL SAFETY
Section 30.3 General provisions respecting machinery
30.3 (1) The employer shall ensure that machinery is erected, installed, assembled, started, operated, used, handled, stored, stopped, serviced, tested, adjusted, maintained, repaired and dismantled in accordance with the manufacturer's specifications.
(2) The employer shall ensure that the manufacturer's rated capacity or other limitations on the operation of the machinery or any part of it, as set out in the manufacturer's specifications or in any relevant specifications certified by an engineer are not exceeded and are clearly marked on the machinery in a location clearly visible to the operator.
(3) An operator of machinery shall not exceed the limitations described in subsection (2).
(4) The employer shall ensure that machinery is regularly inspected for defects and machinery which could cause injury to workers is removed from service until repaired.
[EC2021-126, s. 3]
Part 31 REPAIRS TO MACHINERY
Section 31.1 Inspection and repair
31.1 The employer shall ensure that all power-operated machinery shall
(a) be carefully inspected as far as is practicable each day before being operated;
(b) not be used while repair or maintenance work is being done on the machine;
(c) not have its steam, air or hydraulic lines repaired while subjected to internal pressure; and
(d) be adequately blocked while repair or maintenance work is being done under the machinery.
Part 34 HOISTING APPARATUS
Section 34.2 Construction
34.2 (1) The employer shall ensure that hoisting apparatus is constructed of sufficient strength and equipped with suitable ropes, chains, slings, hooks and other fittings so as to adequately ensure the safety of persons.
(2) The employer shall ensure that hoisting apparatus provided by an employer for the use of a worker is designed, installed, erected, examined, inspected, operated and maintained in accordance with the applicable provisions of the following standards:
(a) CSA Standards:
(i) B167-16, Overhead Cranes, Gentry Cranes, Monorails, Hoists, and Jib Cranes ,
(ii) C22.2 No.33-19, Electrical Safety Requirements for Cranes and Hoists ,
(iii) Z150-20, Safety Code on Mobile Cranes ,
(iv) Z248-17, Code for Tower Cranes ,
(v) Z150.3-17, Safety Code on Articulating Boom Cranes ;
(b) ANSI/ALI ALOIM Standard for Automotive Lifts - Safety Requirements for Operation, Inspection and Maintenance.
(3) The Minister may
(a) establish classifications for operators of hoisting apparatus and define the scope of work and duties that may be performed by persons in each class;
(b) establish a Board of Examiners to examine candidates for the various classifications;
(c) issue certificates of qualification to operators of hoisting apparatus who have passed an examination, who are holders of an equivalent certification from another jurisdiction, or who are otherwise judged by the Board of Examiners to be competent; and
(d) determine fees that are to be paid for examinations and certificates of qualification.
[EC339/93, s. 1; EC2006-43, s. 4; EC2021-126, s. 30]
Section 34.6 Responsibilities of employer
34.6 (1) The employer shall ensure that the operator of hoisting apparatus follows the procedures prescribed in subsection (3).
(2) The employer shall ensure that when mobile cranes are working in an area where the swing clearance of an obstruction is less than 600 mm (2 ft.), adequate barriers are installed to prevent workers from entering the area.
(3) The operator of hoisting apparatus shall
(a) visually inspect the hoisting apparatus before use to verify that it is in safe working order;
(b) move a load only on a signal from a signaller designated under section 34.7 unless he has an unobstructed view of the load at all times during the operation;
(c) raise a load vertically or, if necessary to raise a load obliquely, take precautions to avoid endangering workers;
(d) avoid carrying a load over workers;
(e) not leave a suspended load unattended.
(4) The employer shall ensure that a tag line or guide rope is used to control loads which may swing while being moved.
[EC2021-126, s. 3]
Part 37 WELDING
Section 37.11 Inspection of torches
37.11 (1) The employer and worker shall ensure that welding and cutting torches, their fittings and regulators are inspected before use.
(2) Where inspection reveals faults in the equipment mentioned in subsection (1), the employer shall ensure that the equipment is repaired or replaced with approved fittings in accordance with the manufacturer's specifications by a competent person.
(3) The employer and worker shall ensure that the supply of gas is cut off to any part of the welding or cutting operation when a leak develops and that work is not resumed until the leak is repaired.
[EC2021-126, s. 3]
Part 41 FOREST OPERATIONS
Section 41.4 General obligations of employer
41.4 The employer shall
(a) provide an adequate system of communication, such as mobile radio, telephone or transportation systems at all logging areas to ensure the immediate summoning of medical assistance where required;
(b) provide an adequate means of checking the well-being of any worker whose duties may not allow him to secure assistance in case of injury or other emergency;
(c) provide a minimum of 20 lux (2 ft. candles) of illumination where any logging operation is performed during darkness;
(d) maintain logging trails clear of obstructions, and keep icy pathways within a logging camp sanded or salted;
(e) ensure that a worker performing felling or bucking procedures is within sight or voice communication distance of at least one other worker;
(f) provide wire cable that is suitable for hauling logs which shall conform to the requirements set out in the CSA Standards for wire cable;
(g) inspect, at regular intervals, wire ropes, slings and fittings used in a logging operation and replace or repair these when found to be defective;
(h) provide current safety data sheets to workers employed in chemical application;
(i) provide an approved respirator to all workers mentioned in clause (h).
[EC2021-126, ss. 3, 36]
Section 41.44 Ice road precautions
41.44 Notwithstanding section 41.43, where a haul road is constructed on ice, over water, an employer shall
(a) make a daily inspection of the road to ensure that the road is adequate in strength to carry any load designated to ride thereon;
(b) place signs at suitable locations along the route indicating the minimum allowable distance to be maintained between vehicles and the maximum allowable speed; and
(c) instruct a worker driving a vehicle on an ice road over water with respect to the hazards involved, precautions to be taken and rescue techniques required in case of an ice breakthrough.
[EC2021-126, s. 3]
Section 41.45 Bridges
41.45 The employer shall
(a) design and construct each bridge on a haul road to safely support any load that may pass over the structure;
(b) install curbs on each bridge on a haul road of a height not less than 150 mm (6 in.); or
(c) ensure that each bridge on a haul road is inspected and maintained on a regular basis to ensure the structural integrity of the bridge.
Section 41.60 Inspection
41.60 The owner of the vehicle used in logging shall
(a) locate the controls and attachments in a manner so that the operator of the vehicle has an unobstructed view of the work he is performing; and
(b) maintain and regularly inspect the vehicle for defects before each work shift and keep a record of the inspections.
Part 43 HANDLING & STORAGE OF MATERIALS
Section 43.24 Cleaning procedure
43.24 Drums and barrels used for hazardous liquids, and intended for further use, shall be closely inspected for leaks and other defects, and if to be used for a different liquid shall be thoroughly cleansed with an appropriate neutralizing solution, steam or boiling water, and drained, dried and reinspected, with the operations repeated until the inside is entirely clean.
Section 43.30 Inspection
43.30 Carboys together with their baskets or boxes shall be examined as to their condition before they are filled.
Part 49 ASBESTOS
Section 49.15 Asbestos work area, boundaries
49.15 (1) An asbestos contractor shall, prior to the commencement of asbestos work, ensure that
(a) the boundaries of the asbestos work area are identified and marked by barricades, fences or similar means;
(b) asbestos warning signs are posted at the boundaries of the asbestos work area which meet the requirements of clause 49.1(1)(e);
(c) the permit issued under subsection 49.10(3) is posted;
(d) the immediate work area is cleared of objects, materials and equipment other than those required to do the work; and
(e) the windows, doorways and all other openings are adequately secured to prevent the release of asbestos fibres into other work areas.
(2) No person shall eat, drink or smoke in an asbestos work area.
[EC596/90, s. 1; EC2020-147, s. 8]
Section 49.20 General
49.20 (1) An asbestos contractor shall ensure that each enclosure is equipped with a ventilation system for the purpose of asbestos work that is sufficient to ensure that the enclosure is under adequate negative pressure to prevent the release of respirable asbestos fibres into the air outside the enclosure.
(2) If exhaust ventilation equipment is used to contain asbestos fibres, an asbestos contractor shall ensure that the equipment is
(a) of a type designed and solely used for asbestos abatement procedures;
(b) equipped with a HEPA filter;
(c) maintained in good working condition and inspected regularly in accordance with the manufacturer’s specifications; and
(d) certified by a competent person not less than once a year as being able to function safely and effectively.
(3) An asbestos contractor shall ensure that the capacity of the ventilation system used in an enclosure is such that the air exchange rate is a minimum of 4 air changes per hour, and the differential pressure is at least 5 Pascals (-0.02 inches) of water.
[EC596/90, s. 1; EC2020-147, s. 8]
OCCUPATIONAL HEALTH AND SAFETY ACT
R.S.P.E.I. 1988, c. O-1.01
Section 23 Occupational health and safety program
23. (1) Where 20 or more workers are regularly employed
(a) by an employer other than a constructor or contractor; or
(b) directly by a constructor or contractor,
the employer, constructor or contractor shall establish, and review at least annually, a written occupational health and safety program, in consultation with the committee or representative, if any.
(2) For the purposes of subsection (1), a worker is not regularly employed directly by a constructor or contractor if the worker works with the constructor or contractor as an independent contractor.
(3) An occupational health and safety program shall include
(a) provisions for the training and supervision of workers in matters necessary to their occupational health and safety and the occupational health and safety of other persons at or near the workplace;
(b) provisions for
(i) the preparation of written work procedures for the implementation of occupational health and safety work practices, required by this Act, the regulations or by order of an officer, and
(ii) the identification of the types of work for which the procedures are required at the employer's workplace;
(c) provisions for the establishment and continued operation of a committee required by this Act, including maintenance of records of membership, rules of procedure, access to a level of management with authority to resolve occupational health and safety matters, and information required by this Act or the regulations;
(d) provisions for the selection and functions of a representative where required by this Act, including provision for access by the representative to a level of management with authority to resolve occupational health and safety matters;
(e) a hazard identification system that includes
(i) evaluation of the workplace to identify potential hazards,
(ii) procedures and schedules for regular inspections,
(iii) procedures for ensuring the reporting of hazards and the accountability of persons responsible for the correction of hazards, and
(iv) identification of the circumstances where hazards shall be reported by the employer to the committee or representative, if any, and the procedures for doing so;
(f) a system for workplace occupational health and safety monitoring, prompt follow-up and control of identified hazards;
(g) a system for the prompt investigation of hazardous occurrences to determine their causes and the actions needed to prevent recurrences;
(h) the maintenance of records and statistics, including reports of occupational health and safety inspections and investigations, with provision for making the reports available to persons entitled to receive them under this Act; and
(i) provisions for monitoring the implementation and effectiveness of the program.
(4) The employer shall make a copy of the program established under this section available
(a) to the committee or representative, if any; and
(b) on request, to a worker at the workplace.
(5) The results of a workplace harassment investigation do not constitute a report for the purposes of clause (3)(h).
[S.P.E.I. 2018, c. 45, s. 5]
Section 25 Joint occupational health and safety committee
25. (1) At a workplace where 20 or more persons are regularly employed by an employer, the employer
(a) shall establish and maintain a joint occupational health and safety committee; and
(b) may establish additional such committees.
(2) Where 20 or more persons are regularly employed by one or more constructors at a project that is expected to last three months or more, a constructor shall establish and maintain a committee for the project.
(3) At a workplace where fewer than 20 but more than five persons are regularly employed, the Director may consult with the workers and employers at the workplace regarding the establishment of a committee and the Director may order that a committee be established.
(4) Where the Director orders that a committee be established under subsection (3), the employer shall ensure that the committee is functioning in accordance with this Act within 30 days of receipt of the order.
(5) A committee shall be composed of the number of persons
(a) agreed to by the workers or their union, and the employer; or
(b) ordered by the Director.
(6) Membership of the committee shall be determined as follows:
(a) one-half of the members shall be selected by the union representing the workers or, in the absence of a union, by the workers that the members represent;
(b) one-half of the members shall be selected by the employer.
(7) The committee shall
(a) cooperate to identify hazards to occupational health and safety in the workplace and effective systems to respond to the hazards;
(b) receive, investigate and promptly deal with issues respecting occupational health and safety , other than a complaint of workplace harassment;
(c) participate in inspections, inquiries and investigations respecting the occupational health and safety of workers in the workplace , other than an investigation of a complaint of workplace harassment;
(d) advise the employer on individual protective equipment, devices and safety features that are best suited to the needs of the workers, within the provisions of this Act and the regulations;
(e) advise the employer regarding a policy or program required by this Act;
(f) make recommendations to the employer, the workers and any other persons for the improvement of the occupational health and safety of persons at the workplace; and
(g) maintain records and minutes of committee meetings in a form and manner approved by the Director and provide an officer with a copy of those records and minutes at the request of the officer.
(8) Subject to subsection (9), a committee shall meet at least once each month unless the committee otherwise provides in its rules of procedure.
(9) Where the Director is not satisfied that the frequency of meetings of a committee is sufficient to enable the committee to effectively perform its functions, the Director may order the committee to hold meetings at such frequency as the Director may specify.
(10) A worker who is a member of a committee is entitled to take the necessary time off from work to attend meetings of the committee, to take training prescribed by the regulations and to carry out the worker's functions as a member of the committee.
(11) The time off from work referred to in subsection (10) shall be deemed to be work time for which the worker is entitled to the worker's usual salary and benefits, without change.
(12) A committee shall establish its own rules of procedure.
[S.P.E.I. 2018, c. 45, s. 6]
Section 26 Occupational health and safety representative
26. (1) Where the number of workers employed at a workplace is five or more but no committee is required under section 25, the employer shall require the workers to select at least one representative from among the workers who do not perform managerial functions.
(2) Where the number of workers at a project is five or more but no committee is required under section 25, the constructor shall require the workers to select at least one representative from among the workers who do not perform managerial functions.
(3) Where the number of workers at a workplace is fewer than five, the Director may
(a) consult with the workers and the employer at the workplace regarding whether a representative should be selected at the workplace; and
(b) order that the workers select a representative if the Director considers that a representative is necessary to ensure that occupational health and safety issues in the workplace are monitored.
(4) A worker who is a representative is entitled to take the necessary time off from work to attend meetings of the committee, to take training prescribed by the regulations and to carry out the worker's functions as a representative.
(5) The time off from work referred to in subsection (4) shall be deemed to be work time for which the worker is entitled to the worker's usual salary and benefits, without change.
(6) A representative shall be involved on behalf of the workers, together with the employer, in occupational health and safety issues in the workplace and shall
(a) cooperate to identify hazards to occupational health and safety in the workplace and effective systems to respond to the hazards;
(b) receive, investigate and promptly deal with issues respecting occupational health and safety , other than a complaint of workplace harassment;
(c) participate in inspections, inquiries and investigations respecting the occupational health and safety of workers in the workplace , other than an investigation of a complaint of workplace harassment;
(d) advise the employer on individual protective equipment, devices and safety features that are best suited to the needs of the workers, within the provisions of this Act and the regulations;
(e) advise the employer regarding a policy or program required by this Act; and
(f) make recommendations to the employer, the workers and any other persons for the improvement of the occupational health and safety of persons at the workplace.
[S.P.E.I. 2018, c. 45, s. 7]