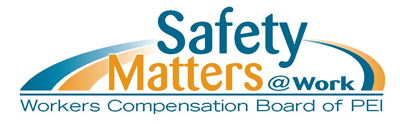


Hazardous or Toxic Substances
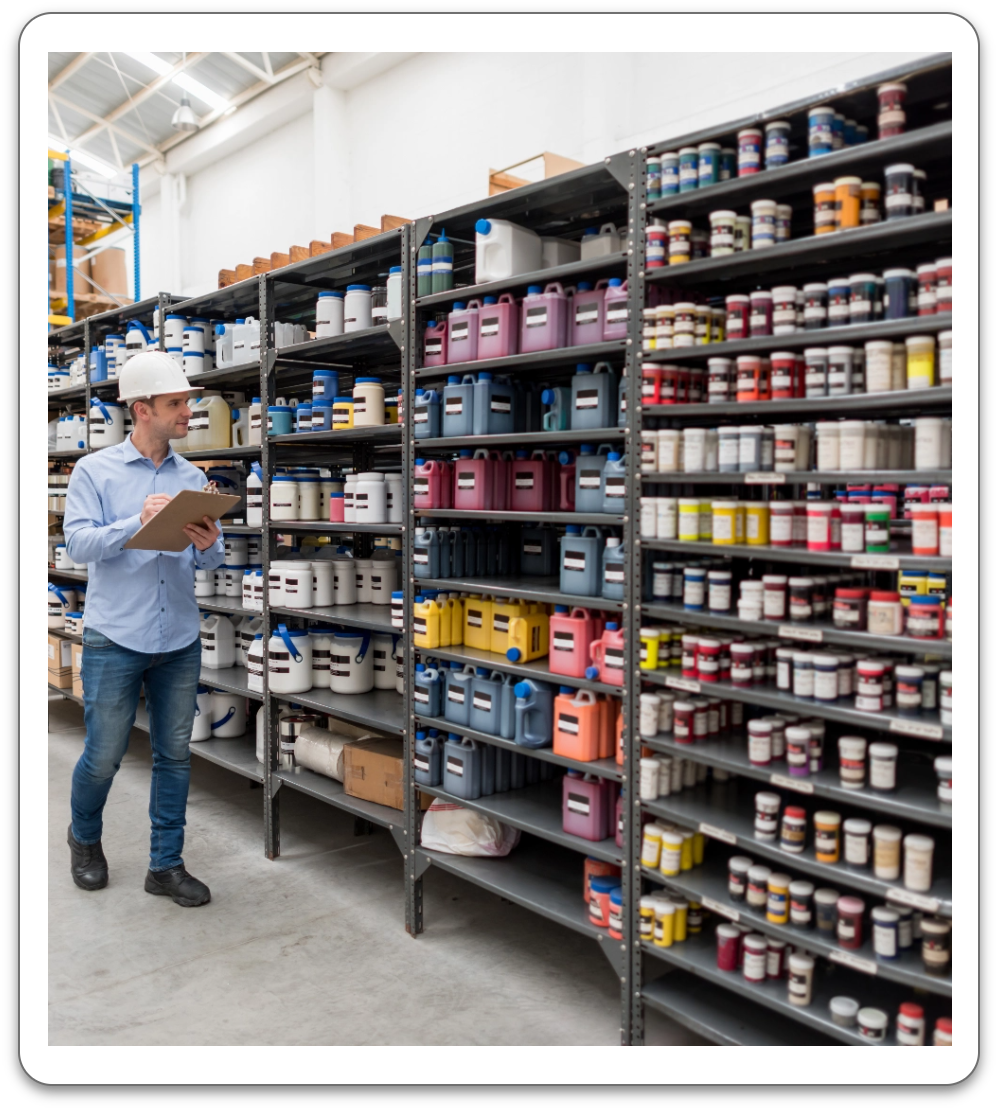
[OHS General Regs., S. x] Follow these links
to related legislation.
Highlighted words reveal
definitions and supplementary
information when selected.
A variety of products are used in many workplaces. Products that are classified as hazardous products under the federal Hazardous Products Act must meet the requirements for WHMIS. Other hazardous or toxic substances such as consumer products, pest control products, nuclear products, and food and drug products are only partially regulated by WHMIS. This topic describes the requirements for substances that fall in this gap or are regulated by other legislation.
Employer duties
Employers must take every reasonable precaution to protect the health and safety of persons at or near the workplace. [OHS Act, S. 12(1)(a)] Employers must make sure that all workers who use, store, transport, or dispose of a hazardous or toxic substance receive appropriate information and training about that substance.
In terms of these substances, employers must:
- Prepare a list of all biological, chemical, or physical agents that are used, produced, or present at the workplace that may be hazardous to the health and safety of workers, or are suspected of being hazardous by the workers. The list must identify all agents by their common or generic name if known. [OHS Act, S. 32(1)]
- For every substance, find out from the supplier, manufacturer, or other sources and record the following information: [OHS Act, S. 32(2)]
- Its ingredients and their common or generic names;
- Its composition and properties;
- The toxicological effects;
- The effects of exposure by contact (skin), inhalation, or ingestion;
- The measures used or to be used to protect workers;
- The emergency measures used or to be used; and
- Information about use, transport, storage, and disposal.
- Keep the list current. [OHS Act, S. 32(3)]
- Provide a copy of the current list to the committee or representative, if any, and on request to an OHS officer or worker. When information is not available, on the ingredients or composition of an agent, the employer will provide the officer with the trade name, and name and address of the manufacturer. [OHS Act, S. 32(3) and (4)]
- Supply and maintain, where reasonable and practical, changing rooms and showering facilities, where there is a high risk of workers being contaminated by a hazardous substance, infectious or other offensive materials that are regularly in the workplace. [OHS General Regs., S. 2.6(3)]
- Not allow hazardous liquids or gases, and explosives to be stored in excavations or trenches. [OHS General Regs., S. 12.6(2)]
Tanks and Vessels
When working in a tank, vessel, or chamber, workers must not enter a space that may contain toxic fumes or gases until it has been determined that the air is sufficiently pure. If in doubt, provide air-supplied respirators and lifelines, as part of a confined space entry procedure. [OHS General Regs., S. 40.3]
When tanks are used to store hazardous liquids, the tank must be prepared or repaired as follows: [OHS General Regs., S. 40.11]
- The tank must be drained as much as possible.
- The inlet pipes must be disconnected and blanked off or moved out of alignment or locked in the closed position.
- Residual liquid and sludge must be removed by workers stationed outside the tank through manholes or hatches. Using water from a hose with a curved nozzle to make sure all parts of the tank are thoroughly washed. Long handles spears may also be used.
- If steam is available, close all openings (except the vent pipe and steam outlet) and blow live steam into the tank for a time suitable for the conditions and nature of the liquid. Open lids or manhole plates during the last one/fifth of the steaming period.
- If steam is not available, keep the tank filled with flowing water for at least 24 hours.
- Thoroughly ventilate after steaming or flooding by forcing air or inducing a draft for at least 2 hours.
- After ventilation, have a competent person (or persons) examine the interior of the tank to make sure it is free from residue, as well as take and test air samples to make sure all hazardous vapours are removed.
- Repeat the steaming or flooding procedures if the tests show that there is still a presence of hazardous vapours or fumes.
Hazardous liquids
When storing hazardous liquids, the employer must make sure that tanks used for storage are: [OHS General Regs., S. 43.9]
- Labelled to identify the contents and nature of the hazards of handling the tank and the hazardous liquids.
- Located above ground or floor level.
- Supported so that if the tank leaks, the leak will be noticed.
- Surrounded with pits, catch basins, or depressions that are large enough to hold the entire content of the largest tank if there is a rupture.
- Covered with paint that prevents corrosion from moisture or fumes.
- Provided with stairways or permanent ladders and platforms where necessary, that allow for convenient and safe access to all parts of the tanks. The stairways and platforms must have railings, and the floors and platforms are preferably constructed of grating.
- Protected from low temperatures. [OHS General Regs., S. 43.10]
- Not placed above passageways. [OHS General Regs., S. 43.11]
- Be placed on foundations that will hold the content of the tank, and have overflow pipes that discharge to a safe place. [OHS General Regs., S. 43.14]
When tanks are used for storing non-flammable hazardous liquids are installed in pits below ground level, the pits must be made of concrete or masonry, and have enough space between the walls and tanks to allow a person to pass at any point. The tanks must be mounted 381 to 457 mm above the bottom of the well. [OHS General Regs., S. 43.12] All control valves must be placed or designed so that they can be turned without any person entering the pit, and have a locking device that is operated from outside the pit. [OHS General Regs., S. 43.13]
Tanks used to store corrosive or caustic liquids must have a permanently open vent pipe that is not smaller than 50 mm (2 inches) in diameter at the highest point in the tank, and a drain connection at the lowest point that discharges from the lowest point to a safe place. [OHS General Regs., S.43.15] The tanks must have the filling connection at the top and the discharge pipe 152 mm above the bottom. [OHS General Regs., S. 43.16]
When barrels or drums that contain flammable liquids are stored in special storerooms inside factories or in small, isolated storehouses that area must be fire-resistant, and the floor of the area must have a slope to a drain pipe that leads outside to a catch basin that is not connected to a sewer. [OHS General Regs., S. 43.17] The floor must be waterproof, with the waterproofing raised at least 76 mm up the side walls. The barrels or drums must be placed in cement platforms, concrete blocks, brick, and metal racks. [OHS General Regs., S. 43.18]
Drums that contain acids must be stored in cool places with the bung facing up. They should be opened carefully to relieve any internal pressure and sealed again each time the drum is moved, or once a week if stored. [OHS General Regs., S. 43.19]
Empty barrels or drums that contained:
- Flammable liquids must be stored for re-use with bungs or outlet plugs present so that they confine the flammable vapours. [OHS General Regs., S. 43.20] These barrels must be steamed before being crushed or broken up. [OHS General Regs., S. 43.23]
- Acids or other non-flammable liquids, if it is to be reused, must be cleaned promptly and stored away from other containers. [OHS General Regs., S. 43.21]
- Hazardous non-flammable liquids, if it is to be reused, must be cleaned promptly and stored away from other containers. [OHS General Regs., S. 43.22]
- Hazardous liquids, intended for further use, must be closely inspected for leaks and other defects. If it is to be used for a different liquid, it must be thoroughly cleansed with an appropriate neutralizing solution, steam, or boiling water, and drained, dried, and reinspected until the inside is entirely clean. [OHS General Regs., S. 43.24]
Worker duties
Workers must:
- Follow the instructions, education and training about air quality provided by your employer, and properly use any equipment that is required.
- Wear the personal protective equipment provided by the employer.
- Be aware of changing conditions and air quality.
- Report any hazards.
- Do not enter a restricted area without authorization and appropriate personal protective equipment, as required by the employer.
General Regulations
EC180/87
Part 2 TOILET AND WASHING FACILITIES
Section 2.6 Requirements
2.6 (1) In every place of employment where running water is available, the employer shall provide
(a) toilet facilities in accordance with the following table:
Table
No. of Persons | Facilities |
1 to 9 | 1 |
10 to 24 | 2 |
25 to 49 | 3 |
50 to 74 | 4 |
75 to 100 | 5 |
Over 100 | (1 for each additional 30 persons) |
(b) a supply of toilet tissue for each toilet at all times and washable covered receptacles for waste;
(c) adequate and suitable facilities for personal washing including a supply of clean hot and cold running water, soap, towels or other suitable means of washing and drying.
(2) Where more than two toilets are required for male workers the employer may substitute urinals for up to 2/3 of the required number of toilets.
(3) Where there is a high risk of contamination of workers by the presence of hazardous substances, infectious or offensive materials that are part of the regular work processes at a workplace, an employer shall, where reasonably practicable, supply and maintain adequate changing and showering facilities.
(4) Where changing and shower facilities referred to in subsection (3) are provided, an employer shall
(a) provide separate shower rooms for male and female employees except where there are fewer than six persons employed at a workplace;
(b) ensure that where there are fewer than six persons employed at a workplace a shower room with a door that has a locking device on the inside is provided;
(c) ensure that the floors of shower rooms have a non-slip surface; and
(d) ensure that at every workplace the water supply, used for washing and showering,
(i) can be manually adjusted to within a range of 35°C and 45°C, and
(ii) is not heated by the injection of steam.
[EC2021-126, ss. 3, 5]
Part 12 EXCAVATIONS, TRENCHES AND CONSTRUCTION
Section 12.6 Water
12.6 (1) The employer shall ensure that every excavation and trench is kept reasonably free of water.
(2) The employer shall ensure that hazardous liquids or gases and explosives are not stored in excavations or trenches.
(3) When hazardous liquids or gases or internal combustion engines are used in or near excavations or trenches, or where hazardous liquid or gases may enter or be present in an excavation or trench, the employer shall ensure that adequate ventilation precautions are taken to prevent the accumulation of hazardous gases in the excavation or trench.
Part 40 TANKS AND VESSELS
Section 40.3 Toxic fumes, precautions
40.3 No worker shall enter any tank, vessel or chamber that may contain toxic fumes or gases until it has been ascertained that the air contained therein is sufficiently pure. In doubtful cases, approved air-supply respirators and lifelines shall be stationed at the entrance to assist those who may become distressed.
[EC2021-126, s. 3]
Section 40.11 Cleaning procedure, tanks used for hazardous liquids
40.11 The employer shall ensure that tanks used for the storage of hazardous liquids shall be prepared for repairs as follows:
(a) the tank shall be drained as completely as possible;
(b) all inlet pipes shall be disconnected and blanked off or moved out of alignment, or the inlet valves shall be locked in the closed position;
(c) residual liquid and sludge shall be removed by workers stationed outside the tank and operating through manholes or hatches with water from a hose line equipped with a curved nozzle for washing all parts of the tank thoroughly and if necessary with long handled spears;
(d) where steam is available all openings except the vent pipe and a steam inlet shall be closed and live steam blown into the tank for a period of time suitable for the conditions and the nature of the liquid, with the lids or manhole plates opened during the last one- fifth of steaming period;
(e) where steam is not available the tank shall be kept filled with flowing water for a period of at least 24 hours;
(f) after steaming or flooding, the tank shall be thoroughly ventilated by means of air under forced or induced draft for a period of at least two hours;
(g) after ventilation, a competent person or persons shall examine the interior of the tank to see that it is free from residue and shall take and test air samples from the tank to ascertain that all hazardous vapours have been removed;
(h) where these tests indicate the presence of hazardous vapours or fumes, the steaming or flooding and ventilating operations shall be repeated.
[EC2021-126, s. 3]
Part 43 HANDLING & STORAGE OF MATERIALS
Section 43.9 Hazardous liquid storage
43.9 The employer shall ensure that tanks used for storing non-flammable hazardous liquids shall meet the following requirements:
(a) labelled to identify the contents and indicate the nature of the hazard involved in handling it as well as instructions for handling of the hazardous liquid;
(b) located above ground or floor level;
(c) so supported that leakage from any part of the tank will be noticeable;
(d) surrounded with pits, catch basins or depressions of sufficient size to hold the entire contents of the largest tank in the event of rupture;
(e) covered with protective paint to prevent corrosion from moisture or fumes; and
(f) provided with stairways or permanent ladders and platforms where necessary, for convenient and safe access to all parts of the tanks with standard safe railings on both stairways and platforms and preferably with floors or platforms constructed of grating.
Section 43.10 Low temperature protection
43.10 Where necessary, above ground tanks used for storing non-flammable hazardous liquids shall be suitably protected against low temperatures.
Section 43.11 Tanks
43.11 Tanks used for storing non-flammable hazardous liquids shall not be placed above passageways.
Section 43.12 Pits
43.12 Where tanks used for storing non-flammable hazardous liquids are installed in pits below ground level the pits shall be made of concrete or masonry, with sufficient space between the walls and the tanks to permit the passage of a person at any point; and the tanks shall be mounted 381 mm to 457 mm (15 in. to 18 in.) above the bottom of the well.
Section 43.13 Control valves
43.13 All control valves for sunken tanks used for storing non-flammable hazardous liquids shall be so situated or of such design that they can be turned without any person entering the pit; and provided with locking devices operated from outside the pit.
Section 43.14 Tank location requirements
43.14 Tanks used for storing non-flammable hazardous liquids shall be placed on foundations that will resist action by the contents of the tank and provided with overflow pipes discharging into a safe place.
Section 43.15 Caustic liquid tanks
43.15 Tanks used for storing corrosive or caustic liquids shall be provided with a permanently open vent pipe, not less than 50 mm (2 in.) in diameter, at the highest point in the tank and a drain connection at the lowest point in the tank discharging into a safe place.
Section 43.16 Connections
43.16 Tanks used for storing corrosive or caustic liquids shall have the filling connection at the top and the discharge pipe 152 mm (6 in.) above the bottom.
[EC2024-600, s. 18]
Section 43.17 Storerooms for flammable liquids
43.17 Where barrels or drums containing flammable liquids are stored in special storerooms inside factories or in small isolated storehouses, the storeroom or house shall be of fire-resistant construction and the floor of the storeroom or house shall slope to a drain pipe leading outside to a catch basin which shall not be connected to a sewer.
Section 43.18 Waterproof floors
43.18 The floor of the storeroom or house shall be waterproof, with the waterproofing extended up the side walls for not less than 76 mm (3 in.) and the barrels or drums shall be placed in cement platforms, concrete blocks, brick and metal racks.
Section 43.19 Acid drums
43.19 Drums containing acids shall be stored in cool places with the bung up; they should be carefully opened sufficiently to relieve any internal pressure, and subsequently sealed again, with the operation repeated each time the drum has been moved or once a week if stored for a period of time.
Section 43.20 Empty barrels
43.20 Empty barrels or drums which have contained flammable liquids shall be stored for re-use with the bungs or outlet plugs in place in order to confine all flammable vapours.
Section 43.21 Cleaning
43.21 Empty barrels or drums which have contained acids or other non- flammable liquids, if to be re-used, shall be promptly cleaned and stored apart from other containers.
Section 43.22 Cleaning
43.22 Barrels or drums which have contained hazardous non-flammable liquids, if to be re-used, shall be promptly cleaned and stored apart from other containers.
Section 43.23 Steaming
43.23 Barrels or drums used for flammable liquids shall be steamed before being crushed or broken up.
Section 43.24 Cleaning procedure
43.24 Drums and barrels used for hazardous liquids, and intended for further use, shall be closely inspected for leaks and other defects, and if to be used for a different liquid shall be thoroughly cleansed with an appropriate neutralizing solution, steam or boiling water, and drained, dried and reinspected, with the operations repeated until the inside is entirely clean.
OCCUPATIONAL HEALTH AND SAFETY ACT
R.S.P.E.I. 1988, c. O-1.01
Section 12 Duties of employers
12. (1) An employer shall ensure
(a) that every reasonable precaution is taken to protect the occupational health and safety of persons at or near the workplace;
(b) that any item, device, material, equipment or machinery provided for the use of workers at a workplace is properly maintained, and is properly equipped with the safety features or devices, as recommended by the manufacturer or required by the regulations;
(c) that such information, instruction, training, supervision and facilities are provided as are necessary to ensure the occupational health and safety of the workers;
(d) that workers and supervisors are familiar with occupational health or safety hazards at the workplace;
(e) that workers are made familiar with the proper use of all safety features or devices, equipment and clothing required for their protection; and
(f) that the employer's undertaking is conducted so that workers are not exposed to occupational health or safety hazards as a result of the undertaking.
(2) An employer shall
(a) consult and cooperate with the joint occupational health and safety committee or the representative, as applicable;
(b) cooperate with any person performing a duty or exercising a power conferred by this Act or the regulations;
(c) provide such additional training of committee members as may be prescribed by the regulations;
(d) comply with this Act and the regulations and ensure that workers at the workplace comply with this Act and the regulations; and
(e) where an occupational health and safety policy or occupational health and safety program is required under this Act, establish the policy or program.
(3) An employer shall establish and implement as a policy, in accordance with the regulations, measures to prevent and investigate occurrences of harassment in the workplace.
[S.P.E.I. 2018, c. 45, s. 3]
Section 32 Chemicals, etc. to be listed
32. (1) An employer at a workplace shall prepare a list of all biological, chemical or physical agents used, handled, produced or otherwise present at the workplace that may be hazardous to the occupational health or safety of workers or are suspected by the workers of being hazardous and the list shall identify all such agents by their common or generic names, where they are known to the employer.
(2) For every biological, chemical or physical agent required to be listed under subsection (1), the employer shall take all reasonable steps to ascertain from suppliers or otherwise and to record the following information on every agent:
(a) the ingredients and their common or generic names;
(b) the composition and the properties;
(c) the toxicological effects;
(d) the effects of exposure, whether by contact, inhalation or ingestion;
(e) the protective measures used or to be used in respect of the agent;
(f) the emergency measures used or to be used to deal with exposure to the agent;
(g) the information on the use, transport, storage and disposal of the agent.
(3) The employer shall ensure that the list referred to in subsection (2) is kept current and the employer shall provide a copy of the current list
(a) to the committee, where one exists, or to the representative, if any; and
(b) on request, to an officer or a worker.
(4) Where the employer is unable to ascertain the ingredients or composition of a biological, chemical or physical agent listed in this section, the employer shall promptly provide the officer with the trade name, and the name and address of the manufacturer of the agent.