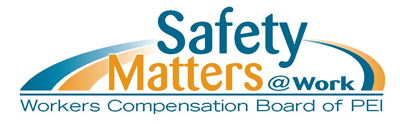


Lockout Tag Out
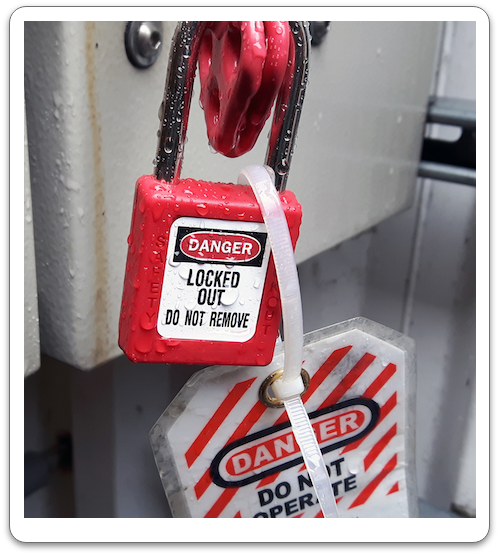
[OHS General Regs., S. x] Follow these links
to related legislation.
Highlighted words reveal
definitions and supplementary
information when selected.
Workers can be exposed to hazards during regular operations, maintenance, repair, or when troubleshooting energized machinery or equipment. Every year, workers are killed or seriously injured when hazardous energy is not properly locked out or safeguarded. Hazardous energy includes electrical, mechanical, hydraulic, pneumatic, chemical, nuclear, thermal, gravitational, or other energy that can harm personnel.
Lockout involves taking steps that will isolate energy from the system (a machine, equipment, or process) which will allow a worker to work on the system safely. Employers must also use safeguards such as a guard shield, guardrail, fence, gate, barrier, wire mesh or other protective enclosure, safety net, handrail, or other similar equipment to protect workers from hazardous energy. [OHS General Regs., S. 30.1 (a)]
Employer duties
Employers must:
- Make sure all electric machinery and equipment have, in addition to the regular start and stop switch, a means of disconnecting the power supply circuit that is: [OHS General Regs., S. 30.6 (1)]
- lockable;
- in a location familiar to all; and
- identified.
- Provide a safety lock and key to all machinery and equipment operators and maintenance personnel to use when disconnecting the energy. [OHS General Regs., S. 30.6(2)]
- Make sure workers are trained in lockout procedures for each situation. [OHS General Regs., S. 30.6(3)]
- Make sure that machinery is not lubricated, cleaned, serviced, or repaired while in motion unless a disconnecting method is available and there is no risk to the worker. [OHS General Regs., S. 30.6(4)]
- Make sure all electric machinery is disconnected from its source of power and locked during repair or maintenance. [OHS General Regs., S. 31.3]
- Make sure workers do not carry out work on the machinery or equipment shut down for cleaning, maintenance, or repairs until they have: [OHS General Regs., S. 30.7(1)]
- Locked out the source of energy using the safety lock and key provided by the employer.
- Put the machine in a zero-energy state by making sure all power sources and other movable parts supported, retained, or controlled by the machine which can move or cause movement, are:
- locked out;
- vented to the atmosphere;
- reduced to atmospheric pressure; or
- otherwise acted upon to render the machinery incapable of spontaneous or unexpected action.
- Put a tag on the control device of the machinery that does not conduct electricity and contains:
- words directing others not to start or operate machinery;
- the worker’s printed name and signature; and
- the date the tag is attached to the machinery.
- Make sure no person removes a lockout device or tag except: [OHS General Regs., S. 30.7(3)]
- the worker who installed it; or
- in an emergency, or when the worker is unavailable after attempts have been made to contact them, as long as a competent worker designated by the employer verifies that the removal would not endanger anyone.
- Make sure to provide sufficient space around individual machines or process units to allow for the safety of workers during operations, adjustments, or repairs. [OHS General Regs., S. 30.8(1)]
- Make sure that all power-operated machinery: [OHS General Regs., S. 31.1]
- is carefully inspected before use each day;
- is not used while repair or maintenance work is being done on that machine;
- does not have its steam, air, or hydraulic lines repaired while they contain internal pressure; and
- is adequately blocked while repair or maintenance work is being done under the machinery.
- Not allow a person to remove or make a safeguard ineffective, other than a removable guardrail or gate, unless necessary for maintenance or adjustments. [OHS General Regs., S. 30.10(1)]
- Make sure where a person has removed or made a safeguard ineffective, the person replaces the safeguard before leaving the unguarded area and verifed the guard will function properly. [OHS General Regs., S. 30.10(2)]
- Make sure that when a safeguard has been removed or made ineffective and when the worker cannot directly control the machinery, the machinery is locked out and tagged. [OHS General Regs., S. 30.10(3)]
Other Employer duties related to Mechanical Safety
Employers must make sure:
- All moving parts of machinery, equipment, and tools are effectively safeguarded unless: [OHS General Regs., S. 30.2]
- they are constructed or located to stop a person or object from coming in contact with them; or
- the guarding would unreasonably interfere with the operation of the machinery, equipment, or tool.
- Machinery is erected, installed, assembled, started, operated, used, handled, stored, stopped, serviced, tested, adjusted, maintained, repaired, and dismantled according to the manufacturer’s specifications. [OHS General Regs., S. 30.3(1)]
- The rated capacity or other limitations specified by the manufacturer or certified by an engineer are not exceeded and are marked on the machinery in a location visible to the operator. [OHS General Regs., S. 30.3(2)]
- The machinery is regularly inspected for defects, and the machinery that could endanger workers is removed from service until repaired. [OHS General Regs., S. 30.3(4)]
- The operational controls on machinery are located, protected, and identified to specify what each control does. [OHS General Regs., S. 30.4(1)]
- When a pedal is used to operate a clutch or belt shifter, that pedal is guarded to prevent unintentional contact that might activate the machine. [OHS General Regs., S. 30.4(2)]
- Each pair of active and idler pulleys is equipped with a permanent belt shifter that has a mechanical way to prevent the belt from creeping off the idler to the active pulley. [OHS General Regs., S. 30.4(3)]
- An alarm system: [OHS General Regs., S. 30.4(4)]
- is installed where moving machine parts may endanger workers during the machine start-up and when there is not a clear view of the machine or parts from the control panel or operator’s station.
- gives an adequate warning before the start-up of the machine to warn workers of the imminent start-up.
- The way to stop the machine is in the immediate area of the workers so that any machine operator has unobstructed access. [OHS General Regs., S. 30.5(1)]
- Every power-driven machine not driven by an individual motor or prime mover is equipped with a clutch, idler pulley, or other means to disengage power sources quickly. [OHS General Regs., S. 30.5(2)]
- Adequate safeguards are provided where a worker comes into contact with moving parts such as belts, rollers, gears, drive-shafts, keyways, pulleys, sprockets, chains, ropes, spindles, drums, counterweights, flywheels or couplings on machinery, pinch-points, and cutting edges. [OHS General Regs., S. 30.9(1)] Safeguards are not necessary for machinery equipped with a device to stop the machine automatically when a worker contacts the moving parts or prevents a worker from coming in contact with the moving parts. [OHS General Regs., S. 30.9(2)]
- Safeguards are strong enough to contain or deflect the broken parts or particles of machinery and flying particles to prevent an injury to a worker during a machine failure. [OHS General Regs., S. 30.9(3)]
- No one alters the design of guards that interlock with the machinery control to prevent operation unless the guard is in its proper place. [OHS General Regs., S. 30.9(4)]
- An alternative mechanism, system, or change in work procedure approved by an officer is put into place to protect workers when it is not practical to provide an effective safeguard. [OHS General Regs., S. 30.9(5)]
- The maximum number of revolutions per minute of an abrasive wheel or disc recommended by the manufacturer is identified on the wheel or disc. The maximum revolutions per minute of a grinder output shaft is identified on the grinder. [OHS General Regs., S. 30.11(1)]
- A tool rest is installed on a fixed grinder in a way that is compatible with the work process. [OHS General Regs., S. 30.11(2)]
- The abrasive and grinding wheels are fitted with protective hoods that are strong enough to contain fragments or ruptured wheels. [OHS General Regs., S. 30.11(4)]
- The workers check the abrasive or grinding wheels for flaws before installing. [OHS General Regs., S. 30.11(5)]
- The workers mount the abrasive wheels according to the manufacturer’s specifications. [OHS General Regs., S. 30.11(6)]
- Before doing any work, make sure workers run abrasive and grinding wheels at full operating speed according to the manufacturer’s specifications. [OHS General Regs., S. 30.11(7)]
- Provide a push stick or push block for feeding materials into cutting or shaping machinery where there is a risk of injury to a worker’s hands. [OHS General Regs., S. 30.12]
- Stands for lead sawyers on sawmills are protected by shields not less than 1.2 m (4 ft.) in height and are constructed of: [OHS General Regs., S. 30.13(1)]
- steel or iron at least 6 mm (1/4 in.) thick; or
- wooden planks at least 5 cm (2 in.) thick; or
- other material of equal strength.
- Wheels on band saws and the return portion of the blades between the upper and lower wheels are enclosed with guards of sheet metal at least 1 mm (0.04 in.) thick or other material of equal strength. [OHS General Regs., S. 30.13(2)]
- The circular saws are provided with hood guards covering most of the exposed part of the saw, at least to the depth of the teeth. [OHS General Regs., S. 30.13(3)]
- The access doors in the guards or enclosures to tumbler drums that might be hazardous to workers are fitted with interlocks which will: [OHS General Regs., S. 30.14]
- prevent the access doors from opening during the rotation of drums; or
- disconnect the power from the driving machinery that will make the tumblers stop when doors are opened.
- The guardrails are installed on all open sides of an agitator, beater, or paddle tank less than 100 cm (40 in.) above the floor, walkway, or work area. [OHS General Regs., S. 30.15]
- A conveyor is constructed and installed: [OHS General Regs., S. 30.16(1)]
- to have sufficient clearance between the material transported and fixed or moving object;
- to avoid shearing points between moving and stational parts; and
- that no conveyor can feed onto a stopped conveyor.
- Emergency stop devices are provided on a power-driven conveyor at locations including loading and unloading stations, drive and take up sections, and other convenient places along the run of the conveyor. [OHS General Regs., S. 30.16(2)]
- A walkway not less than 450 mm (18 in.) wide with guardrails is provided along the entire length of an elevated conveyor where worker access is necessary. [OHS General Regs., S. 30.17(1)]
- Adequate crossing facilities are provided where a worker must cross over a conveyor. [OHS General Regs., S. 30.17(2)]
- Sheet metal or screen guards are installed under a conveyor not entirely enclosed to prevent injury to a worker from material falling from a conveyor. [OHS General Regs., S. 30.18(1)]
- Adequate guards extending 1060 mm (40 in.) from the pulleys and along the sides of the conveyor are provided for a belt conveyor. [OHS General Regs., S. 30.18(2)]
- A screw conveyor is placed in metal troughs fitted with secured covers at least 3.2 mm (1/8 in.) thick metal plates in removable sections or other equivalent protection. [OHS General Regs., S. 30.18(3)]
- Adequate safeguards are provided around the opening when a screw conveyor is fed from the floor level. [OHS General Regs., S. 30.18(4)]
Workers
Workers must:
- Follow the instructions, education, and training about lock-out procedures and machine safety provided by your employer, and properly use any required equipment.
- Not carry out work on machinery and equipment shut down for cleaning, maintenance, or repairs until you have:
- Locked out the source of energy using the safety lock and key provided by the employer. [OHS General Regs., S. 30.7(1)(a)]
- Put the machine in a zero-energy state by making sure all power sources, pressurized fluids, air, potential mechanical energy, accumulators, air surge tanks, kinetic energy of machine parts, loose or freely movable machine parts, and material or workpieces supported, retained, or controlled by the machine which can move or cause movement, are:
- locked out;
- vented to the atmosphere;
- reduced to atmospheric pressure; or
- otherwise acted upon to render the machinery incapable of spontaneous or unexpected action.
- Put a tag on the control device of the machinery that does not conduct electricity and contains:
- words directing others not to start or operate machinery;
- the worker’s printed name and signature; and
- the date the tag is attached to the machinery.
- Make sure they have double checked to make sure that the machinery or equipment is inoperative before doing the work. [OHS General Regs., S. 30.7(2)]
- Make sure that before putting machinery in motion, it will not endanger any person. [OHS General Regs., S. 30.7(4)]
- Not stand on the supporting frames of an open conveyor while loading, unloading or when clearing blockages unless the conveyor is stopped and locked out. [OHS General Regs., S. 30.19(1)]
- Lockout and tag the machinery where a safeguard for machinery has been removed or made ineffective and when the machinery cannot be directly controlled by themself. [OHS General Regs., S. 30.10(3)]
Workers must also:
- Not exceed the limitations marked on the machinery. [OHS General Regs., S. 30.3(3)]
- Before starting the machinery, make sure that start up will not harm themselves or others. [OHS General Regs., S. 30.4(5)]
- Make sure that no one, including themself, is endangered by its operation. [OHS General Regs., S. 30.4(6)]
- Wear close-fitting clothing, confine head or facial hair and do not wear dangling neckwear, jewelley, rings, or similar items that might come in contact moving parts of machinery. Wearing medic-alert bracelets is permitted when such bracelets are used with transparent rubber bands that fit snugly over the bracelets. [OHS General Regs., S. 30.8(2)]
- A tool rest is installed on a fixed grinder in a manner compatible with the work process. [OHS General Regs., S. 30.11(2)]
- Not operate abrasive and grinding wheels at speed over that is specified by the manufacturer. [OHS General Regs., S. 30.11(3)(a)]
- Not grind on the side of an abrasive wheel unless the wheel has been designed for that purpose. [OHS General Regs., S. 30.11(3)(b)]
- Not adjust a tool rest while the grinder is in motion. [OHS General Regs., S. 30.11(3)(c)]
- Use a push stick or push block for feeding materials into cutting or shaping machinery where there is a risk of injury to the hands. [OHS General Regs., S. 30.12]
General Regulations
EC180/87
Part 30 MECHANICAL SAFETY
Section 30.1 Definitions
30.1 In this regulation
(a) "safeguard" means a guard shield, guardrail, fence, gate, barrier, wire mesh or other protective enclosure, safety net, handrail or other similar equipment designed to protect the safety of workers, but does not include personal protective equipment;
(b) "push block" means a block of wood long enough to protect workers from the danger area and provided with a handle similar to that of a hand plane and having a shoulder at the rear;
(c) "push stick" means a narrow strip of wood or other soft material with a notch cut into one end.
[EC2021-126, s. 3]
Section 30.2 Guarding moving parts
30.2 The employer shall ensure that all moving parts of machinery, equipment and tools shall be effectively safeguarded unless
(a) they are so constructed or located as to prevent a person or object from coming in contact with them; or
(b) the guarding would unreasonably interfere with the operation of the machinery, equipment or tool.
Section 30.3 General provisions respecting machinery
30.3 (1) The employer shall ensure that machinery is erected, installed, assembled, started, operated, used, handled, stored, stopped, serviced, tested, adjusted, maintained, repaired and dismantled in accordance with the manufacturer's specifications.
(2) The employer shall ensure that the manufacturer's rated capacity or other limitations on the operation of the machinery or any part of it, as set out in the manufacturer's specifications or in any relevant specifications certified by an engineer are not exceeded and are clearly marked on the machinery in a location clearly visible to the operator.
(3) An operator of machinery shall not exceed the limitations described in subsection (2).
(4) The employer shall ensure that machinery is regularly inspected for defects and machinery which could cause injury to workers is removed from service until repaired.
[EC2021-126, s. 3]
Section 30.4 Starting machinery
30.4 (1) The employer shall ensure that operational controls on machinery are
(a) located and protected in such a manner as to prevent unintentional activation;
(b) suitably identified so as to indicate the nature of each control mechanism.
(2) Where a pedal is used to operate a clutch or belt shifter, the employer shall ensure that it is so guarded that it cannot be struck accidentally so as to activate the machine.
(3) The employer shall ensure that each pair of active and idler pulleys is equipped with a permanent belt shifter provided with a mechanical means of preventing the belt from creeping from the idler to the active pulley.
(4) The employer shall ensure that
(a) where moving machine parts may endanger workers when the machine is started and there is not a clear view of the machine or parts from the control panel or operator's station, as alarm system is installed; and
(b) the alarm system gives an effective warning before start up of the machine so that workers are made aware of the imminent start-up.
(5) Before starting machinery, a worker shall ensure that neither he nor any other worker is endangered by its starting.
(6) While operating machinery, a worker shall ensure that neither he nor any other worker is endangered by its operation.
[EC2021-126, s. 3]
Section 30.5 Stopping machinery
30.5 (1) The employer shall ensure that the operator of any machine has unimpeded access in the immediate area of the workers work area to the means of stopping that machine.
(2) The employer shall ensure that every power driven machine not driven by an individual motor or prime mover is equipped with a clutch, idler pulley or other means of quickly disengaging the power sources.
[EC2021-126, s. 3]
Section 30.6 Lock-out
30.6 (1) The employer shall ensure that in addition to the normal control start and stop switch, all electrically driven machinery and equipment has installed in the power supply circuit a disconnecting means which is
(a) of a lockable type;
(b) in a location familiar to all; and
(c) properly identified.
(2) The employer shall provide a safety lock and key for use on disconnecting means described in subsection (1) to all machinery and equipment operators and all maintenance personnel.
(3) The employer shall ensure that a worker has been adequately trained in lockout procedures for the particular situation.
(4) The employer shall ensure that machinery is not lubricated, cleaned, serviced or repaired while in motion unless a means is available which does not expose the worker to risk of injury.
[EC2021-126, s. 3]
Section 30.7 Servicing
30.7 (1) Where machinery or equipment is shut down for cleaning, maintenance or repairs, the employer shall ensure that no worker carries out work on the machinery or equipment until that worker has
(a) locked out the source of energy using the safety lock and key that the employer must provide under section 30.6; and
(b) put the machine in a zero energy state by ensuring that all
(i) power sources,
(ii) pressurized fluids and air,
(iii) potential mechanical energy,
(iv) accumulators and air surge tanks,
(v) kinetic energy of machine members,
(vi) loose or freely movable machine members, and
(vii) material or workpieces supported, retained or controlled by the machine which can move or cause movement, are
(A) locked out,
(B) vented to the atmosphere,
(C) reduced to atmospheric pressure, or
(D) otherwise acted upon to render the machinery incapable of spontaneous or unexpected action;
(c) put on the control device of the machinery a tag which does not conduct electricity and which contains
(i) words directing persons not to start or operate the machinery,
(ii) the worker's printed name and signature, and
(iii) the date when the tag was put on the machinery.
(2) No worker shall carry out work on machinery or equipment shut down for cleaning, maintenance or repairs until he has complied with subsection (1) and has double checked to ensure that the machinery is inoperative.
(3) No person shall remove a lock-out device or tag except
(a) the worker who installed it; or
(b) in an emergency or where attempts made to contact the worker indicate he is not available, a competent worker designated by the employer, who has first ensured that no person will be endangered by the removal.
(4) On completion of servicing or repairs, the worker shall, before the operation of the machine is resumed, ensure that putting the machinery in motion will not endanger any person.
[EC2021-126, s. 3]
Section 30.8 Contact with machinery
30.8 (1) The employer shall ensure that sufficient space is provided around individual machines or process units in order to ensure the safety of workers while operations, adjustments or repairs are being carried out.
(2) Where a worker or the worker’s clothing might come into contact with moving parts of machinery, the worker shall
(a) wear close fitting clothing;
(b) confine head or facial hair; and
(c) avoid wearing dangling neckwear, jewellery, rings or similar items. *
* The wearing of medic-alert bracelets is permitted when such bracelets are used with transparent rubber bands that fit snugly over the bracelets.
[EC2021-126, s. 3]
Section 30.9 Safeguards
30.9 (1) Subject to this section, an employer shall provide effective safeguards where a worker may come into contact with moving belts, rollers, gears, drive-shafts, keyways, pulleys, sprockets, chains, ropes, spindles, drums, counterweights, flywheels or couplings on machinery, pinchpoints and cutting edges.
(2) Subsection (1) does not apply to machinery that is equipped with an effective device which stops the machinery automatically when a worker comes into contact with the parts of it mentioned in subsection (1) or prevents a worker from coming in contact with parts mentioned in subsection (1).
(3) Where there is a possibility of machine failure that may result in an injury to a worker from flying objects, the employer shall install safeguards strong enough to contain or deflect the broken parts or particles of the machinery and flying particles of any product.
(4) The employer and worker shall not alter the design where machines are designed with guards that interlock with the machinery control so as to prevent operation of the machine unless the guard is in its proper place.
(5) Where it has been determined that an effective safeguard cannot be provided, the employer shall ensure that an alternative mechanism, system or change in work procedure, approved by an officer, is put into place to protect workers from being exposed to the hazards associated with the lack of the safeguard.
[EC2021-126, s. 3]
Section 30.10 Removing and rendering ineffective safeguards
30.10 (1) A person shall not remove or render ineffective a safeguard, other than a removable guardrail or gate, that is required by these regulations unless the removal or rendering ineffective is necessary to enable the effecting of maintenance or adjustments.
(2) Where a person has removed or rendered ineffective a safeguard, he shall ensure that
(a) the safeguard is replaced before he leaves the unguarded area; and
(b) the safeguard will function properly.
(3) Where a safeguard for machinery has been removed or rendered ineffective and the machinery cannot be directly controlled by the worker, the worker who removes or renders ineffective the safeguard shall lock-out and tag the machine according to section 30.7.
[EC2021-126, s. 3]
Section 30.11 Abrasive and grinding wheels
30.11 (1) An employer shall ensure that
(a) the maximum number of revolutions per minute of an abrasive wheel or disc, as recommended for safe use in the manufacturer's specifications, is identified on the wheel or disc; and
(b) the maximum revolutions per minute of a grinder output shaft is identified on the grinder.
(2) An employer and worker shall ensure that a tool rest is installed on a fixed grinder in a manner compatible with the work process.
(3) A worker shall not
(a) operate abrasive and grinding wheels at a speed in excess of that specified by the manufacturer;
(b) do grinding on the side of an abrasive wheel unless the wheel has been designed for that purpose; or
(c) adjust a tool rest while the grinder is in motion.
(4) The employer shall ensure that abrasive and grinding wheels are fitted with protective hoods of sufficient strength to contain fragments or ruptured wheels.
(5) The employer shall ensure that abrasive or grinding wheels are checked for flaws before installation.
(6) The employer shall ensure that abrasive wheels are mounted in accordance with manufacturer's specifications.
(7) Before applying any work, the employer shall run abrasive and grinding wheels at full operating speed in accordance with grinder and wheel manufacturer's specifications.
[EC2021-126, s. 3]
Section 30.12 Cutting or shaping machinery
30.12 Where there is or may be a danger of injury to a worker's hands, the employer shall provide and the worker shall use a push stick or push block for feeding materials into cutting or shaping machinery.
[EC2021-126, s. 3]
Section 30.13 Saws
30.13 (1) The employer shall ensure that stands for lead sawyers on sawmills are protected by shields not less than 1.2 m (4 ft.) in height and constructed of iron or steel not less than 6 mm (1/4 in.) thick, wooden planks not less than 5 cm (2 in.) thick or other material of equal strength.
(2) The employer shall ensure that wheels on band saws and the return portion of the blades between the upper and lower wheels are enclosed with guards of sheet metal not less than 1 mm (.04 in.) in thickness or other material of equal strength.
(3) The employer shall ensure that circular saws are provided with hood guards which cover as much as possible of the exposed part of the saw at least to the depth of the teeth.
Section 30.14 Tumblers
30.14 The employer shall ensure that the access doors in the guards or enclosures to tumbler drums are, if there is a potential hazard to workers, fitted with interlocks which will
(a) prevent the access doors from opening while the drums are rotating; or
(b) disconnect the power from the driving machinery causing the tumblers to stop, if the doors are opened.
[EC2021-126, s. 3]
Section 30.15 Agitators
30.15 When the top of an open agitator, beater or paddle tank is less than 100 cm (40 in.) above the floor, walkway or work area, the employer shall ensure that guardrails are installed on all exposed sides.
Section 30.16 Conveyors
30.16 (1) The employer shall ensure that a conveyer is so constructed and installed that
(a) sufficient clearance is provided between the material transported and fixed or moving object;
(b) hazardous shearing points between moving and stationary parts are avoided;
(c) no conveyer can feed onto a stopped conveyer.
(2) The employer shall ensure that a power driven conveyer to which a worker has access is provided with emergency stop devices at
(a) loading and unloading stations;
(b) drive and take up sections; and
(c) other convenient places along the run of the conveyer.
[EC2021-126, s. 3]
Section 30.17 Walkways
30.17 (1) The employer shall ensure that an elevated conveyer, where worker access is necessary, is provided with a walkway along its entire length which is not less than 450 mm (18 in.) wide and is equipped with guardrails.
(2) Where a worker must cross over a conveyer, the employer shall ensure that adequate crossing facilities are provided.
[EC2021-126, s. 3]
Section 30.18 Guards
30.18 (1) Where there is danger of injury to a worker from material falling from a conveyer, the employer shall ensure that sheet metal or screen guards are installed under a conveyer which is not entirely enclosed.
(2) The employer shall ensure that a belt conveyer is provided with adequate guards extending 1 060 mm (40 in.) from the pulleys and along the sides of the conveyer where there is danger of injury to a worker.
(3) The employer shall ensure that a screw conveyer is placed in metal troughs fitted with secured covers of not less than 3.2 mm (1/8 in.) thick metal plates in removable sections or other equivalent protection.
(4) The employer shall ensure that when a screw conveyer is fed from the floor level, adequate safeguards are provided around the opening.
[EC2021-126, s. 3]
Section 30.19 Prohibitions
30.19 (1) Unless the conveyer is stopped and locked out, a worker shall not stand on the supporting frames of an open conveyer while loading, unloading or when clearing blockages.
(2) A worker shall remove heavy or bulky articles by hand from a moving conveyer at designated stations only.
[EC2021-126, s. 3]
Part 31 REPAIRS TO MACHINERY
Section 31.1 Inspection and repair
31.1 The employer shall ensure that all power-operated machinery shall
(a) be carefully inspected as far as is practicable each day before being operated;
(b) not be used while repair or maintenance work is being done on the machine;
(c) not have its steam, air or hydraulic lines repaired while subjected to internal pressure; and
(d) be adequately blocked while repair or maintenance work is being done under the machinery.
Section 31.3 Electric
31.3 Electric machinery shall have the source of power disconnected and locked during repair or maintenance.