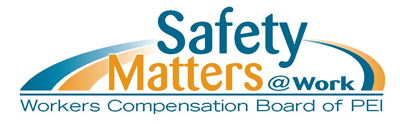


Respirator Programs
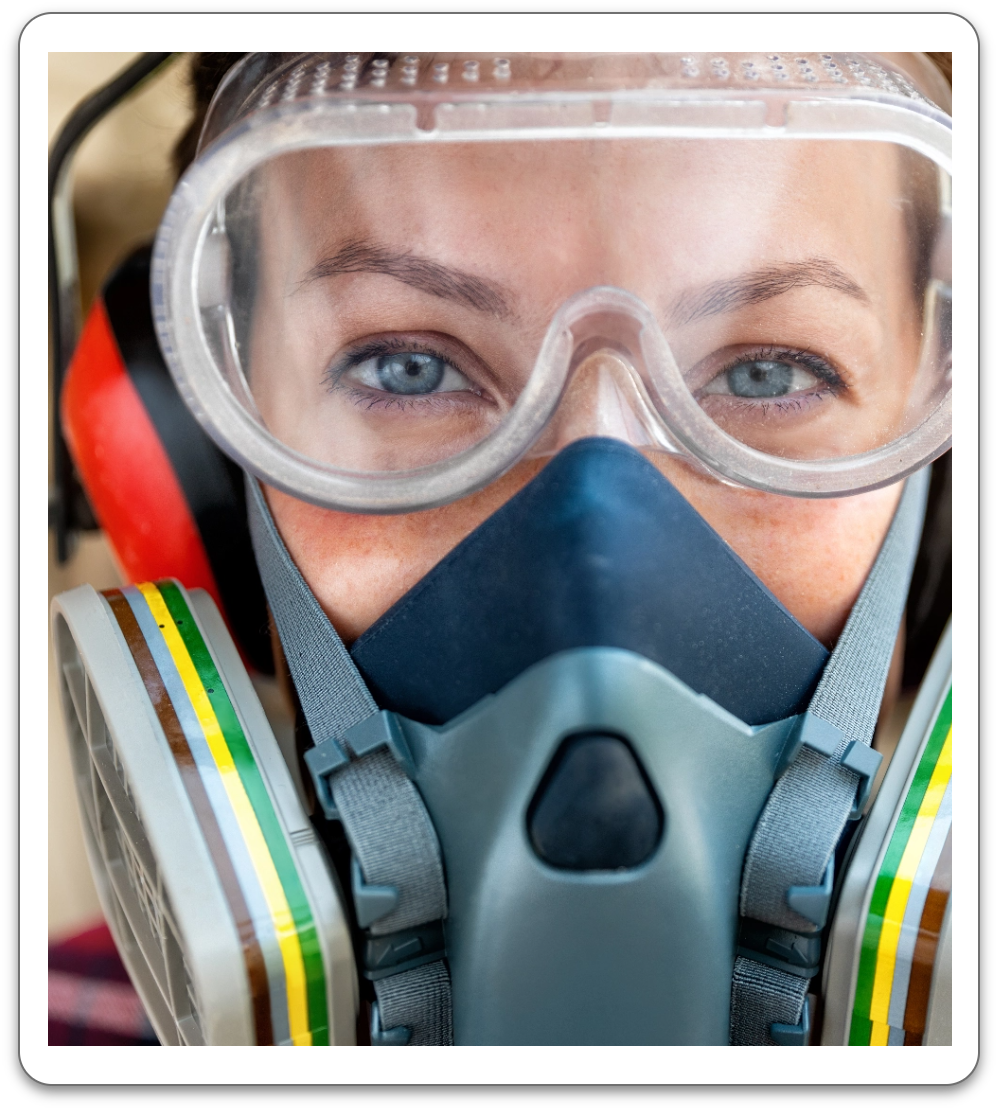
[OHS General Regs., S. x] Follow these links
to related legislation.
Highlighted words reveal
definitions and supplementary
information when selected.
Respiratory hazards can include oxygen-deficient atmospheres, or airborne contaminants such as biological agents, dusts, mists, fumes, and gases. Properly selected and fitted respirators can provide protection. At the same time, respirators should only be used if other hazard control methods are not practical or possible. Employers must follow the hierarchy of controls to protect workers from hazardous air (more information is available in the Personal Protective Equipment topic).
Limitation: This topic summarizes only the legal requirements related to respirators. For full health and safety requirements for specific hazards (e.g., asbestos), please see the relevant topic and legislation.
Employer duties
Employers must:
- Take all reasonable precautions to protect the health and safety of workers and others who may be at or near their workplace. [OHS Act, S. 12(1)(a)]
- Make sure the selection, use, and care of respirators follow CSA Standard Z94.4-18, Selection, Use, and Care of Respirators. [OHS General Regs., S. 45.18(1)]
- Make sure that air provided for any respiratory protective equipment follows CSA Standard Z180.1-19, Compressed Breathing Air and Systems. [OHS General Regs., S. 45.18(2)]
- Make sure all respirators provided to workers are equipped with appropriate safety features or devices recommended by the respirator manufacturer or required by the OHS Regulations. [OHS Act, S. 12(1)(b)]
- Make sure all respirators provided to workers are properly maintained in good condition. [OHS Act, S. 12(1)(b)] [OHS General Regs., S. 45.2]
- Instruct workers who require respirators on the respirator’s use, limitations, and maintenance requirements. Instruction must occur before workers begin using their respirator. [OHS Act, S. 12(1)(e)] [OHS General Regs., S. 45.3]
- Make sure every worker who is exposed to hazardous air wears approved protective respiratory equipment in situations where preventing or eliminating hazardous air is not reasonably practicable or where only temporary or emergency conditions can result in exposure to hazardous air. [OHS General Regs., S. 45.17]
- Make sure workers who are required to use respirators are clean-shaven where the respirator seals with the face. [OHS General Regs., S. 45.19]
- Provide approved respirators to forest operations workers employed in chemical application. [OHS General Regs., S. 41.4(i)]
- Provide approved air-supply respirators (and lifelines) at the entrance of a tank, vessel, or chamber that may contain toxic fumes or gases to assist individuals who may become distressed. (Note: Employers must take all reasonable steps to make sure no workers enter any tank, vessel, or chamber that may contain toxic fumes or gases until it is confirmed that the air inside is sufficiently pure.) [OHS General Regs., S. 40.3]
- Make sure where a worker is wearing an approved air-line or approved air-hose type respirator in an atmosphere immediately harmful to the worker: [OHS General Regs., S. 45.20(3)]
- The air supply source is attended by another worker with the equipment necessary to rescue or assist if the worker is unconscious or injured; and
- Provide the worker with enough auxiliary supply of compressed air to enable them to escape from the area in an emergency or until rescue can begin.
Respirator program
When respirators are used in a workplace, a written respirator program must be developed, implemented, and followed by all those who have a role to play in their safe and effective use.
It is important that the respirator is appropriate for the type of airborne contaminants. Some respirators may require fit testing to find the size and model that can create a good seal with the worker’s face. This fit should be evaluated periodically because workers’ face shape may change due to weight changes, new dentures, etc. Workers may also be asked to remove facial hair where it interferes with the seal between the respirator and skin.
Worker duties
Workers must:
- Test respirators before each use. [OHS General Regs., S. 45.4]
- Not use any respirators that may be defective. [OHS General Regs., S. 45.4]
- Wear approved respiratory equipment if they are exposed to hazardous air in situations where preventing or eliminating hazardous air is not reasonably practicable or where only temporary or emergency conditions can result in exposure to hazardous air. [OHS General Regs., S. 45.17]
- Be clean-shaven where the respirator seals with the face if they are required to use respirators. [OHS General Regs., S. 45.19]
- Wear dust-type respirators while buffing, grinding, or sanding material that produces harmful dusts. [OHS General Regs., S. 29.7]
- Wear approved respirator equipment while welding if air sample tests indicate that respirator equipment is necessary. [OHS General Regs., S. 37.10]
- Carry enough auxiliary supply of compressed air to enable them to escape from the area in an emergency or until rescue can begin if they are wearing an approved air-line or approved air-hose type respirator in an atmosphere immediately harmful to them [OHS General Regs., S. 45.20(3)(b)]
Additional duties for asbestos contractors
Asbestos contractors must:
- Make sure asbestos warning signs posted at the boundaries of an asbestos work area state that respiratory protection must be worn in the enclosure. [OHS General Regs., S. 49.1(1)(iv)]
- Include a copy of their respiratory protection program, as required by the CSA Standard Z94.4-18, Selection, Use, and Care of Respirators, in their current asbestos work procedure manual as part of their application for the asbestos contractor’s certificate. [OHS General Regs., S. 49.9(3)(a)(ii)]
- Provide respirators to workers that are appropriate for the risk level of the anticipated exposure to asbestos fibres. Contractors must also make sure that workers use these respirators within the asbestos work area. [OHS General Regs., S. 49.14(1)]
- Make sure that respirators provided to workers are selected, used, cleaned, stored, maintained, inspected, and tested following CSA Standard Z94.4-18, Selection, Use, and Care of Respirators. [OHS General Regs., S. 49.14(2)]
- Make sure the record for each worker contains all reports from health examinations that assessed the worker’s potential exposures, ability to use a respirator, and any specified limitations. [OHS General Regs., S. 49.26(1)(a)]
Additional duties for workers involved in asbestos work
Workers must:
- Wear a negative pressure half facepiece respirator while collecting samples of materials that may contain asbestos. [OHS General Regs., S. 49.4(2)(a)]
- Wear a respirator appropriate for the risk level of the anticipated exposure to asbestos fibre before entering a full enclosure where asbestos work is taking place. [OHS General Regs., S. 49.18(2)(c)]
- When leaving a contaminated asbestos work area, workers must: [OHS General Regs., S. 49.19]
- Not remove their respirator until they are in the shower room of the enclosure and have thoroughly showered, and
- Clean their respirator while in the shower.
To access these, you must first create an account with "CSA Communities".
Go to: https://community.csagroup.org/login.jspa?referer=%252Findex.jspa
Once you are logged in, click on the text below the "OHS Standards / View Access" graphic.
Click on the jurisdiction of your choice to see the CSA Standards as referenced in that legislation.
Standards may also be purchased from CSA Group: https://store.csagroup.org/
Approved
“approved” means any recognized standard or level which is acceptable to the Director.General Regulations
EC180/87
Part 29 HAND TOOLS AND PORTABLE POWER TOOLS
Section 29.7 Responsibilities of worker, power tools
29.7 The worker shall
(a) wear eye protection when using power tools;
(b) wear dust type respirators while buffing, grinding or sanding material which produces harmful dusts;
(c) disconnect the source of power from power tools before changing accessories;
(d) keep all guards on power tools in place while the tool is in use;
(e) protect flexible shafts of flexible tools against denting and kinking which may damage the inner core;
(f) when starting the motor of a flexible shaft tool, hold the tool end firmly to prevent whipping.
[EC2021-126, s. 3]
Part 37 WELDING
Section 37.10 Respirators
37.10 Approved respirator equipment shall be worn if tests of air samples indicate it is necessary.
Part 40 TANKS AND VESSELS
Section 40.3 Toxic fumes, precautions
40.3 No worker shall enter any tank, vessel or chamber that may contain toxic fumes or gases until it has been ascertained that the air contained therein is sufficiently pure. In doubtful cases, approved air-supply respirators and lifelines shall be stationed at the entrance to assist those who may become distressed.
[EC2021-126, s. 3]
Part 41 FOREST OPERATIONS
Section 41.4 General obligations of employer
41.4 The employer shall
(a) provide an adequate system of communication, such as mobile radio, telephone or transportation systems at all logging areas to ensure the immediate summoning of medical assistance where required;
(b) provide an adequate means of checking the well-being of any worker whose duties may not allow him to secure assistance in case of injury or other emergency;
(c) provide a minimum of 20 lux (2 ft. candles) of illumination where any logging operation is performed during darkness;
(d) maintain logging trails clear of obstructions, and keep icy pathways within a logging camp sanded or salted;
(e) ensure that a worker performing felling or bucking procedures is within sight or voice communication distance of at least one other worker;
(f) provide wire cable that is suitable for hauling logs which shall conform to the requirements set out in the CSA Standards for wire cable;
(g) inspect, at regular intervals, wire ropes, slings and fittings used in a logging operation and replace or repair these when found to be defective;
(h) provide current safety data sheets to workers employed in chemical application;
(i) provide an approved respirator to all workers mentioned in clause (h).
[EC2021-126, ss. 3, 36]
Part 45 PERSONAL PROTECTIVE EQUIPMENT
Section 45.2 Maintenance
45.2 The employer shall ensure that personal protective equipment is maintained in good condition.
Section 45.3 Instruction
45.3 Every employer shall ensure that every worker who is required to use personal protective equipment shall be given pre-job instruction by the employer to understand its use, its limitations, and its maintenance requirements, as far as these relate to its correct use by the worker.
[EC2021-126, s. 3]
Section 45.4 Testing
45.4 A worker wearing or using personal protective equipment shall test the equipment before each use and shall not wear or use any equipment the worker has reason to believe is defective.
[EC2021-126, s. 3; EC2024-600, s. 20]
Section 45.17 Hazardous air
45.17 (1) Every employer shall ensure that when workers are or may be exposed to an oxygen deficient atmosphere or harmful concentrations of air contaminants, mechanical means of engineering design shall be utilized to prevent or to eliminate such hazardous conditions of exposure.
(2) Every employer shall ensure that where the prevention or elimination of such hazardous conditions is not reasonably practicable, or where the exposure results from temporary or emergency conditions only, every worker exposed shall wear approved protective respiratory equipment.
[EC2021-126, s. 3]
Section 45.18 Standards
45.18 (1) The employer shall ensure that the selection, use and care of respirators meet the applicable standards and specifications set out and referred to in the CSA Standard Z94.4-18 , "Selection, Use, and Care of Respirators
(2) The employer shall ensure that where air is provided for the purpose of any respiratory protective equipment, the air meets the applicable standards and specifications set out and referred to in the CSA Standard Z180.1-19 , Compressed Breathing Air and Systems.
(3) The employer shall ensure the selected respiratory protective equipment for filtering particulate matter meets the applicable standards and specifications set out in CSA Standard Z94.4.1:21 , "Performance of Filtering Respirators," or a standard offering equivalent protection.
[EC2020-147, s. 7; EC2021-126, ss. 3, 44; EC2024-600, s. 21]
Section 45.19 Shaving
45.19 Every employer shall ensure that workers required to use a respirator shall be clean shaven where the respirator seals with the face.
[EC2021-126, s. 3]
Section 45.20 Signs
45.20 (1) Every employer shall ensure that access routes to work areas where workers may be exposed to oxygen deficient atmosphere or harmful concentrations of air contaminants shall be posted with signs and specifying
(a) the required personal protective equipment; and
(b) the areas and hazards involved.
(2) The employer shall ensure
(a) that sufficient workers who are trained in rescue procedures are immediately available whenever workers are working in areas where an oxygen deficient atmosphere or harmful concentrations of air contaminants exist or are likely to develop; and
(b) that the rescue workers have immediate access to appropriate respirators or other aids necessary to effect a rescue.
(3) The employer shall ensure that where a worker is wearing an approved air-line or approved air-hose type respirator in an atmosphere immediately harmful to the worker
(a) the air supply source shall be attended by another worker who shall be equipped to effect rescue or render assistance if the worker is rendered unconscious or otherwise incapacitated; and
(b) the worker shall be provided with and carry an auxiliary supply of compressed respirable air of sufficient capacity to enable the worker to escape from the area in an emergency or until rescue is effected.
[EC2021-126, s. 3; EC2024-600, s. 22]
45.21 Repealed. [EC2004-632, s. 6]
45.22 - 45.23 Repealed. [EC2004-632, s. 7]
Part 49 ASBESTOS
Section 49.1 Definitions
49.1 (1) In this Part,
(a) "asbestos" means any of the following asbestiform silicates:
(i) actinolite,
(ii) anthophyllite,
(iii) chrysotile,
(iv) crocidolite,
(v) amosite, or
(vi) tremolite;
(b) "asbestos-containing material" means
(i) material, other than vermiculite insulation, that contains 1 per cent or more asbestos by dry weight, and
(ii) vermiculite insulation;
(c) "asbestos contractor" means the holder of a valid asbestos contractor’s certificate;
(d) "asbestos contractor’s certificate" means a valid asbestos contractor’s certificate granted or deemed to have been granted under section 49.9;
(e) "asbestos warning sign" means a sign posted at the boundaries of an asbestos work area that states
(i) that an asbestos hazard is present,
(ii) that a cancer and lung disease hazard is present,
(iii) that the enclosure is restricted to authorized personnel only, and
(iv) that respiratory protection and protective clothing must be worn in the enclosure;
(f) "asbestos work" means the handling of asbestos or asbestos-containing material, and includes
(i) the removal of asbestos or asbestos-containing material,
(ii) the encapsulation or repair of asbestos or asbestos-containing material, or
(iii) the enclosure of asbestos or asbestos-containing material for the purpose of creating a physical barrier to potential fibre release;
(g) "asbestos work area" means the area in which asbestos work is being prepared for or carried on by an asbestos contractor and the contractor’s workers, and includes any enclosure established by the asbestos contractor or the workers;
(h) "exposure to asbestos" means the exposure of a worker to airborne respirable asbestos fibres originating from asbestos or asbestos-containing material;
(i) "friable asbestos-containing material" means asbestos-containing material that when dry can be crumbled, pulverized or powdered by hand pressure and includes asbestos-containing material that is in a crumbled, pulverized or powdered state;
(j) "HEPA filter" means a high efficiency particulate aerosol filter that has an efficiency of at least 99.97% in containing an aerosol of 0.3 of a micrometre in diameter;
(k) "Threshold Limit Values" means the threshold limit values for asbestos exposure specified by the ACGIH in its publication "Threshold Limit Values and Biological Exposure Indices" adopted under subsection 49.3(3).
(2) In this Part, "Type I Removal Operations" means removal operations that present a minimal risk of releasing asbestos fibres into the air, such as the removal of asbestos-containing material that is nonfriable, work that can be done without damaging the asbestos-containing material, including the use of non-powered handheld tools as long as water is used to control fibre release, and
(a) removal of asbestos-containing material ceiling tiles where the total area to be disturbed is less than 1 square meter without damage;
(b) removal of non-friable asbestos-containing material without damage;
(c) removal of vinyl asbestos floor tile, asbestos cement products, and millboard where water is used to control fibre release; and
(d) removal of less than one square meter of drywall where joint-filling compounds with asbestos-containing material were used.
(3) In this Part, "Type II Removal Operations" means removal operations that present a medium risk of asbestos exposure to workers, such as the removal or minor disturbance of friable asbestos-containing material with a surface area of less than 0.09 of a square meter or 1 square foot during the repair, alteration, maintenance or demolition of all or part of a building, or any machinery or equipment, or where the minor removal or disturbance exceeds the scope of a Type I Removal, including
(a) using a mechanical or electrically powered tool, fitted with a HEPA filter dust collector, to cut, shape or grind non-friable manufactured products containing asbestos;
(b) removing all or part of a false ceiling to gain access to a work area where friable asbestos-containing material is, or is likely to be, lying on the surface of the false ceiling;
(c) removing, encapsulating, enclosing or disturbing a surface area of less than 0.09 of a square meter or 1 square foot of friable asbestos-containing material during the repair, alteration, maintenance, demolition or dismantling of a building, structure, machine, tool or equipment, or parts of any of them;
(d) performing glove bag operations;
(e) dry removal of non-friable asbestos-containing material where the material may be cut, broken, or otherwise damaged during removal; and
(f) removing a surface area of up to 9.3 square meters or 100 square feet of contiguous ceiling tile containing asbestos or sheet vinyl flooring having an asbestos backing.
(4) In this Part, "Type III Removal Operations" means removal operations during the repair, alteration, maintenance or demolition of all or part of any building, machinery or equipment that present the highest risk of asbestos exposure to workers, including
(a) spraying of an encapsulant over friable asbestos using a low-pressure sprayer;
(b) using a power tool not having a dust collection device equipped with a HEPA filter to cut, grind or abrade asbestos-containing material;
(c) any indoor operation involving the removal or stripping of friable asbestos-containing material; and
(d) repairing, altering or demolishing a boiler, furnace or similar device or any part of it that is made in part of asbestos-containing material.
[EC596/90, s. 1; EC2020-147, s. 8]
Section 49.4 Sampling of asbestos-containing material
49.4 (1) An employer or owner of a workplace shall ensure that a competent person
(a) collects representative samples of any materials in the workplace that the employer or the competent person suspects contain asbestos; and
(b) determines whether each of the samples is asbestos-containing material.
(2) When collecting samples of materials in accordance with clause (1)(a), the competent person shall
(a) wear a negative pressure half face piece respirator;
(b) take all reasonable measures to ensure asbestos fibres are not released during the sampling collection process; and
(c) ensure all bulk samples are submitted to an accredited lab for analysis in accordance with industry standards acceptable to the Director.
(3) If an employer or a competent person suspects that a material contains asbestos, the material shall be treated as asbestos-containing material unless the competent person determines that it is not asbestos-containing material.
[EC596/90, s. 1; EC2020-147, s. 8]
Section 49.9 Asbestos contractor’s certificate
49.9 (1) No person shall undertake asbestos work unless the person is the holder of a valid asbestos contractor’s certificate.
(2) A person may apply for an asbestos contractor’s certificate by submitting to the Director an application in the form required by the Director containing the information and other requirements specified in subsection (3).
(3) An applicant for an asbestos contractor’s certificate shall provide for the purposes of the application referred to in subsection (2)
(a) a copy of the applicant’s current asbestos work procedure manual that
(i) is to be used in the asbestos work the applicant proposes to carry out under the authority of the certificate,
(ii) includes a copy of the applicant’s Respiratory Protection Program, as required by the CSA Standard Z94.4-18, "Selection, Use, and Care of Respirators", and
(iii) is satisfactory to the Director;
(b) proof satisfactory to the Director that any workers the applicant intends to engage to carry out the asbestos work have successfully completed a course in asbestos abatement acceptable to the Director;
(c) confirmation that the applicant has or has access to the equipment necessary to perform the asbestos work in accordance with the contractor’s procedure manual referred to in clause (a) and this Part;
(d) proof satisfactory to the Director that the applicant has at least one competent person to supervise the asbestos work to be undertaken by the applicant;
(e) confirmation that the applicant has implemented a worker medical surveillance program that meets the requirements set out in section 49.25; and
(f) confirmation that the applicant has established and will maintain the records required by section 49.26.
(4) The Director may grant an asbestos contractor’s certificate to an applicant where the Director is satisfied that
(a) the applicant has submitted an application in accordance with subsection (2); and
(b) the applicant has met the requirements of subsection (3).
(5) A certificate issued under subsection (4) shall be subject to any terms and conditions in respect of the type of asbestos work that may be undertaken by the certificate holder that the Director considers appropriate.
(6) Subject to subsections (7) and (8), a certificate expires on the earlier of
(a) five years from the date of issue; or
(b) the sale of the business for which it was issued.
(7) A certificate in respect of which no notification has been provided under section 49.10 for a period of three years expires at the end of the three-year period.
(8) A certificate that was issued under this Part as it read immediately prior to the coming into force of this subsection and that was valid and in force on the coming into force of this subsection is deemed to be a certificate under this section according to its terms for a period of two years.
(9) No person shall transfer a certificate to any other person or business.
[EC596/90, s. 1; EC2020-147, s. 8]
Section 49.14 Respiratory protection
49.14 (1) An asbestos contractor shall provide, and ensure that workers use, within an asbestos work area, respirators which are appropriate for the level of risk of the anticipated exposure to asbestos fibres.
(2) An asbestos contractor shall ensure that the respirators provided to workers are selected, used, cleaned, stored, maintained, inspected and tested in accordance with the relevant provisions of CSA Standard Z94.4-18 , "Selection, Use, and Care of Respirators".
[EC596/90, s. 1; EC2020-147, s. 8]
Section 49.18 Enclosure entry
49.18 (1) Where asbestos work is in progress, an employer shall ensure that only workers who have successfully completed the training courses referred to in subsection 49.7(4) are permitted to enter the enclosure.
(2) Prior to entering a full enclosure where asbestos work is taking place, a worker shall
(a) remove all street clothing and leave the clothing in the clean area of the asbestos work area;
(b) put on clean disposable protective clothing; and
(c) wear a respirator as required in subsection 49.14(1).
[EC596/90, s. 1; EC2020-147, s. 8]
Section 49.19 Worker exit decontamination procedure
49.19 After a worker completes asbestos work in a contaminated work area, or when the worker leaves the contaminated work area for any reason, the worker shall
(a) remove all loose asbestos fibres from protective clothing with the vacuum system while still in the contaminated work area room of the full enclosure;
(b) enter the worker transfer room of the full enclosure and remove all protective clothing except the respirator, and place the clothing in the waste container provided for that purpose;
(c) enter the shower room of the enclosure and thoroughly shower before removing the respirator;
(d) adequately clean the respirator while in the shower; and
(e) enter the worker change room to dry and dress in street clothing.
[EC596/90, s. 1; EC2020-147, s. 8]
Section 49.26 Worker record
49.26 (1) An asbestos contractor shall establish and maintain an accurate and complete record for each worker, containing
(a) the reports from examinations performed which assess the worker’s potential exposures, ability to use a respirator, and any specified limitations of use;
(b) a detailed work history containing dates and length of jobs performed including types of job and material handled; and
(c) the worker’s training records.
(2) An asbestos contractor shall ensure that all worker records required under subsection (1) shall be maintained for a period of not less than 40 years.
[EC596/90, s. 1; EC2020-147, s. 8]
OCCUPATIONAL HEALTH AND SAFETY ACT
R.S.P.E.I. 1988, c. O-1.01
Section 12 Duties of employers
12. (1) An employer shall ensure
(a) that every reasonable precaution is taken to protect the occupational health and safety of persons at or near the workplace;
(b) that any item, device, material, equipment or machinery provided for the use of workers at a workplace is properly maintained, and is properly equipped with the safety features or devices, as recommended by the manufacturer or required by the regulations;
(c) that such information, instruction, training, supervision and facilities are provided as are necessary to ensure the occupational health and safety of the workers;
(d) that workers and supervisors are familiar with occupational health or safety hazards at the workplace;
(e) that workers are made familiar with the proper use of all safety features or devices, equipment and clothing required for their protection; and
(f) that the employer's undertaking is conducted so that workers are not exposed to occupational health or safety hazards as a result of the undertaking.
(2) An employer shall
(a) consult and cooperate with the joint occupational health and safety committee or the representative, as applicable;
(b) cooperate with any person performing a duty or exercising a power conferred by this Act or the regulations;
(c) provide such additional training of committee members as may be prescribed by the regulations;
(d) comply with this Act and the regulations and ensure that workers at the workplace comply with this Act and the regulations; and
(e) where an occupational health and safety policy or occupational health and safety program is required under this Act, establish the policy or program.
(3) An employer shall establish and implement as a policy, in accordance with the regulations, measures to prevent and investigate occurrences of harassment in the workplace.
[S.P.E.I. 2018, c. 45, s. 3]