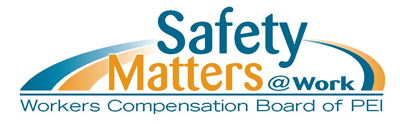


Asbestos
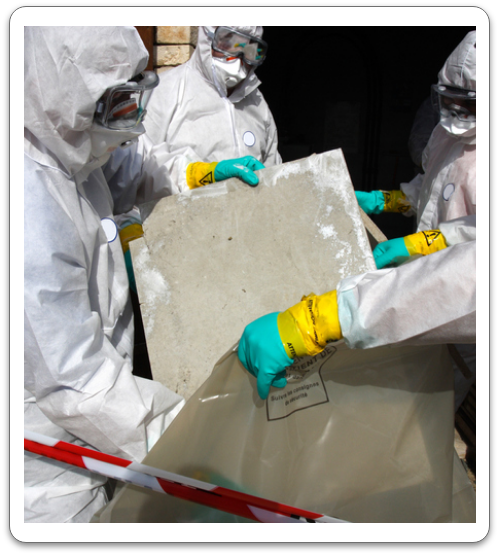
[OHS General Regs., S. x] Follow these links
to related legislation.
Highlighted words reveal
definitions and supplementary
information when selected.
Due to its heat and fire resistance qualities, asbestos was widely used in the past - often in buildings and homes as insulation against cold weather, noise, and for fireproofing. However, asbestos is also very hazardous. Breathing air contaminated with asbestos may cause serious health problems, including lung disease and cancer. The health effects of exposure to asbestos are latent, meaning they become evident many years after the first exposure.
Because of their shape and small size, airborne asbestos fibres can be inhaled. When these fibres reach the lungs, the lung tissue may trap the fibres. This encapsulation may lead to lung scarring and excessive development of fibrous tissue (pneumoconiosis) that damages the lungs.
Most buildings built before 1990 will have parts that contain asbestos. Asbestos must be identified to prevent the release of asbestos fibres when renovating or demolishing.
What is Asbestos?
Asbestos is the generic name for several naturally-occurring fibrous mineral silicates and includes all forms of asbestiform silicates, such as actinolite, anthophyllite, chrysotile crocidolite, amosite and tremolite. [OHS General Regs., S.49.1]
Where do you find asbestos?
- Asbestos cement pipes;
- Wallboard and joint compound;
- Siding;
- Roofing;
- Vinyl and asphalt flooring, including backing and mastics;
- Acoustic or decorative wall and ceiling plaster, including: paints, spackles, coatings, ceiling tiles, lay-in panels;
- Thermal insulation, including spray-applied, blown-in, boiler lagging and gaskets, breaching, pipe wrap, tank and vessel coverings;
- Fireproofing material, including blankets, curtains, countertops, gloves, electrical wiring, insulation, cloth, structural insulation;
- Flexible fabric firestops, duct connections, and insulation;
- Packing materials;
- Gaskets;
- Felts;
- Caulking;
- Putties;
- Joint compounds;
- Adhesives;
- Interior surfaces of duct work in buildings where there was past airborne contamination with asbestos fibres;
- Car and truck brake pads; and
- Vehicle transmission components, such as clutches.
Duties of employers, contractors and owners
These duties apply to every workplace where asbestos is present. [OHS General Regs., S. 49.2]
Employers, contractors, and owners all have responsibilities to make sure that exposure to asbestos is prevented and work is undertaken using specific procedures.
Exposure must be reduced to the lowest practical level and cannot exceed the established threshold limit values. Take all necessary measures including using engineering controls, work practices and hygiene practices. [OHS General Regs., S.49.8 (1)]
Employers must:
- Make sure nobody uses, applies, or installs asbestos or asbestos containing material. [OHS General Regs., S.49.3(1)]
- Make sure that nobody remediates, disturbs, or works with asbestos-containing material without using appropriate methods to contain the fibres and keep the contamination in the air to below the threshold limit values. [OHS General Regs., S.49.3(2)]
- When a material is suspected to contain asbestos, it is treated as though it does until a competent person determines that it is free of asbestos. [OHS General Regs., S.49.4(3)]
- Make sure that before the demolition of a building, structure, all or part of machinery, equipment, aircraft, vehicle or vessel, all material that could release asbestos fibres into the atmosphere are removed. [OHS General Regs., S. 49.23]
The asbestos contractor must make sure all asbestos work is done so that it does not create a risk to the health or safety of any worker or other people. [OHS General Regs., S. 49.17 (4)]
Sampling
Employers must make sure only a competent person collects workplace samples of materials suspected to contain asbestos, as identified by the employer or the competent person [OHS General Regs., S. 49.4(1)]
When collecting samples suspected to contain asbestos, the competent person must: [OHS General Regs., S.49.4 (2) and (3)]
- Treat suspected material as though it does contain asbestos until it has been determined to be free of asbestos.
- Wear a negative pressure half face piece respirator.
- Take all reasonable measures to make sure asbestos fibres are not released into the air during the sampling collection process.
- Make sure all bulk samples are analyzed by an accredited lab according to the industry standards acceptable to the Director.
Asbestos samples must be analyzed by a laboratory accredited by the Canadian Association for Laboratory Accreditation (CALA) or the American Industrial Hygiene Association (AIHA) Asbestos Analysts Registry (AAR) in accordance with the National Institute of Occupational Safety and Health (NIOSH) Manual of Analytical Methods. Air tests to confirm asbestos fibres in ambient air must use the National Institute of Occupational Safety and Health (NIOSH) test methods. [OHS General Regs., S.49.8 (2) and (3)]
Inventory
Employers or owners must make sure:
- A competent person keeps an inventory that lists all asbestos-containing material present in the workplace. This inventory must be kept at the workplace and updated each time the asbestos containing material is repaired or removed. [OHS General Regs., S.49.5(1)]
- At least once a year, the asbestos-containing material is inspected by a competent person to ensure condition is stable and it is not hazardous. [OHS General Regs., S.49.5 (1)(d)]
- The inventory of asbestos-containing material: [OHS General Regs., S.49.5 (2)]
- Provides a general description of the asbestos-containing material, including the type of asbestos and the percentage of asbestos contained in the sample;
- Identifies the location of the asbestos-containing material;
- Specifies which locations have material that may release asbestos fibres into the atmosphere due to it being damaged or in poor repair;
- Includes when the inventory was prepared and any subsequent dates it was reviewed or updated; and
- Includes the names any competent people involved in the sampling as well as preparation, review and updating of the inventory.
Asbestos Management Plans
Employers or owners must make sure that workplaces that may have asbestos-containing material present develop an asbestos management plan, implement it, and communicate to workers about its contents and requirements. [OHS General Regs., S.49.6]
Asbestos management plans must: [OHS General Regs., S.49.6]
- Be reviewed at least once a year and when there is a relevant change in work conditions;
- Be developed, reviewed and updated in consultation with the joint occupational safety and health committee (JOSH) or representative, if any;
- Prevent asbestos-containing material that has been identified as being damaged or in poor repair from releasing asbestos fibres into the atmosphere; and
- Protect the health and safety of workers if asbestos-containing material becomes airborne.
An asbestos contractor must develop emergency response procedures to follow if a serious injury or emergency occurs within the asbestos work area. [OHS General Regs., S.49.24]
Exposure to Asbestos
Employers or owners must:
- Monitor the concentration of airborne asbestos in the workplace and exposure of workers to asbestos, using a recognized method approved by the Director. [OHS General Regs., S.49.7 (1)]
- Maintain records of the monitoring, and keep these records for at least 40 years. [OHS General Regs., S.49.7(2)(b)]
- Provide copies of these records as soon as possible to the workers and their JOSH committee or representative. [OHS General Regs., S.49.7 (3)]
- Make sure that workers handling, disturbing, or removing any asbestos-containing material have successfully completed an asbestos abatement course. [OHS General Regs., S.49.7 (4)]
- Make sure that workers transporting or handling sealed containers of asbestos-containing material have successfully completed an asbestos awareness course acceptable to the Director. [OHS General Regs., S.49.7 (4)]
- Reduce or eliminate exposure of workers to asbestos-containing material to the lowest practical level using all available and required procedures including using engineering controls, work practices and hygiene practices. [OHS General Regs., S.49.8 (1)]
- Make sure exposures do not exceed the established threshold limit values. [OHS General Regs., S.49.8 (1)]
Asbestos Contractor’s Certificates
Employers or owners of a workplace must make sure that all asbestos work is done by a person who holds a valid asbestos contractor’s certificate as granted by the Director. [OHS General Regs., S. 49.9 (1)] Certificates are valid for five years, but are not transferable and expire if the business is sold. [OHS General Regs., S. 49.9 (6) and (9)]
The applicant for an asbestos contractor’s certificate must provide: [OHS General Regs., S. 49.9]
- A copy of the applicant’s current asbestos work procedure manual that will be used in the proposed asbestos work.
- A copy of a Respiratory Protection Program that meets the requirements as established by the CSA Standard Z94.4-18, Selection, Use, and Care of Respirators.
- Satisfactory proof that all workers who will carry out the asbestos work have successfully completed a course in asbestos abatement that meets the required standards set by the Director.
- Confirmation that the applicant has or has access to all equipment required by the contractor’s procedure manual to perform the asbestos work.
- Satisfactory proof that the applicant has at least one competent person to supervise the asbestos work to be undertaken by the applicant.
- Confirmation of applicant’s worker medical surveillance program.
Before Beginning Asbestos Work
An asbestos contractor must:
- First determine the type and content of the asbestos or asbestos-containing material present in the work area. Refer to the inventory workplace’s asbestos management plan or have a competent person collect samples to submit to an accredited laboratory. [OHS General Regs., S.49.12 (1)]
- Take all reasonable measures to make sure asbestos fibres that could be breathed in are not released while the material is being sampled. [OHS General Regs., S.49.12 (2)]
- When the sampling results are returned, provide the Director with written notice at least three business days before beginning any asbestos work. [OHS General Regs., S.49.10 (1)]
- Make sure the written notification:[OHS General Regs., S.49.10 (2)]
- Is signed by the asbestos contractor or a competent person authorized to represent the asbestos contractor.
- Includes a description of the asbestos work to be done that shows procedures will be done as specified in the asbestos work procedure manual, or that new procedures have been developed to accommodate the particular needs of the asbestos work.
- Lists the names of all workers performing the asbestos work and confirm that those workers successfully completed an asbestos abatement course.
- Lists the names of all competent people supervising the asbestos work and satisfactory proof they are competent to supervise.
- Confirms these workers have participated in a medical surveillance program.
If the Director suspends or cancels an asbestos contractor’s certificate, all asbestos work that has not begun or is not yet completed must stop immediately. [OHS General Regs., S.49.11 (3)]
For protective clothing and equipment, an asbestos contractor must:
- Provide and pay for the required protective clothing if a worker’s personal clothing may become contaminated with asbestos-containing material. [OHS General Regs., S.49.13 (1)]
- Make sure that all workers within an asbestos work area wear protective clothing. Protective clothing must: [OHS General Regs., S.49.13 (2) and (3)]
- Be made of material resistant to penetration by asbestos fibres.
- Cover the head and fit snugly at the neck, wrists, ankles, and anywhere necessary to protect against the risk of exposure to asbestos fibres.
- Include footwear that is impermeable to asbestos fibres.
- Make sure that workers do not wear or remove the protective clothing outside of the asbestos work area. [OHS General Regs., S.49.13 (3)]
- Provide respirators appropriate for the level of risk of the anticipated exposure to asbestos fibres. [OHS General Regs., S.49.14 (1)]
- Make sure workers use the provided respirators when in an asbestos work area. [OHS General Regs., S.49.14 (1)]
- Make sure respirators provided are selected, used, cleaned, stored, maintained, inspected and tested according to the CSA Standard Z94.4-18, Selection, Use, and Care of Respirators. [OHS General Regs., S.49.14 (2)]
Asbestos Work
There are three types of asbestos removal work:
- Type I Removal Operations present the least risk of releasing asbestos fibres into the air, such as asbestos-containing material that is non- friable and work can be done without damaging it. Work may include using non-powered handheld tools as long as water is used to prevent the release of fibres. [OHS General Regs., S. 49.1(2)]
- Type II Removal Operations present an increased risk of releasing asbestos, such as the removal or minor disturbance of friable asbestos-containing material with a surface area of less than 0.09 of a square meter or where the minor removal or disturbance exceeds the scope of a Type I Removal. [OHS General Regs., S. 49.1(3)]
- Type III Removal Operations means removal operations with the highest risk of asbestos exposure, including the spraying of an encapsulant over friable asbestos using a low- pressure sprayer or any indoor removal or stripping of friable asbestos-containing material. [OHS General Regs., S. 49.1(4)]
Before beginning asbestos work, the asbestos contractor must: [OHS General Regs., S.49.15]
- Clearly establish and identify the boundaries of the asbestos work area by using barricades, fences or other similar barriers.
- Post warning signs at the boundaries of the asbestos work area that state:
- An asbestos hazard is present.
- A cancer and lung disease hazard is present.
- The enclosure is restricted to authorized personnel only.
- Respiratory protection and protective clothing must be worn in the enclosure.
- Post the asbestos contractor’s permit to undertake the asbestos work.
- Clear the area, only keeping the materials and equipment needed to do the work.
- Secure or seal all windows, doorways or other openings to prevent the release of asbestos fibres.
- Make sure nobody eats, drinks, or smokes inside an asbestos work area.
Encapsulation
- An employer may be ordered to remove the asbestos-containing material or seal it with an encapsulant that penetrates or bridges the material if it is possible that asbestos may be released into the air. [OHS General Regs., S.49.16 (3)]
- Do not apply a liquid sealant to encapsulate friable asbestos-containing material if it has visibly deteriorated. [OHS General Regs., S.49.16 (1)]
- Do not encapsulate friable asbestos-containing material by applying a liquid sealant if the friable asbestos-containing material’s strength and bond to the underlying materials or surfaces cannot support both its own weight and the weight of the sealant. [OHS General Regs., S.49.16 (1)]
- Only use a liquid sealant to encapsulate asbestos-containing material if an officer determines that it does not go against the two bullets above, and that workers can safety occupy the space after the material is encapsulated. [OHS General Regs., S.49.16 (2)]
Enclosures
Asbestos contractors must:
- Use an enclosure constructed according to the approved asbestos work procedure manual. [OHS General Regs., S.49.17 (1)]
- Make sure enclosures are built for asbestos work and can effectively contain the asbestos fibres that may be released during a Type I, Type II, or Type III Removal Operations. [OHS General Regs., S.49.17 (2)]
- Apply at least five days before beginning the asbestos work if they want to use different work procedures than those in the approved asbestos work procedure manual. A variance will require the contractor to specify any changes in procedures, equipment or materials for the asbestos work and must demonstrate these changes still meet the established requirements. [OHS General Regs., S.49.17 (3)]
- Make sure that the work does not create a health and safety risk for any person. [OHS General Regs., S.49.17 (4)]
- Make sure final clearance air samples are within the established threshold limit values before dismantling the enclosure for asbestos work area. [OHS General Regs., S. 49.17 (5)]
Employers must make sure that before an enclosure is dismantled, the entire area is sprayed with a latex sealant, and allowed to dry for an appropriate amount of time. [OHS General Regs., S. 49.17]
Enclosure entry and exit
The employer must:
- Make sure only workers who have successfully completed the required training courses enter the enclosure. [OHS General Regs., S.49.18 (1)]
- Make sure before people enter the enclosure and asbestos work area: [OHS General Regs., S.49.18 (2)]
- Remove all street clothing before entering the enclosure and leave their street clothes in the clean area of the asbestos work area;
- Put on clean disposable protective clothing; and
- Wear the provided and appropriate respirator.
- Make sure workers leaving the contaminated work area [OHS General Regs., S.49.19]
- Remove all loose asbestos fibres from protective clothing with the vacuum system while still in the contaminated work area room of the full enclosure;
- Enter the worker transfer room and remove all protective clothing except the respirator, and place the clothing in the waste container provided for that purpose;
- Shower before removing the respirator;
- Clean the respirator while in the shower; and
- Dry and dress in street clothing using the worker change room located in the clean area of the asbestos work area.
Ventilation and Vacuum Cleaner Requirements
The asbestos contractor must make sure:
- Each enclosure must have a ventilation system that puts the enclosure under adequate negative pressure to prevent the release of respirable asbestos fibres into the air outside the enclosure. [OHS General Regs., S.49.20 (1)]
- If an exhaust ventilation equipment is used to contain asbestos fibres, the system must be: [OHS General Regs., S.49.20 (2)]
- Designed and only used for asbestos abatement projects;
- Equipped with a HEPA filter;
- Maintained in good working order;
- Inspected regularly in accordance with the manufacturer’s specifications; and
- Certified as functional, safe and effective by a competent person at least once a year.
- Make sure the ventilation system for an enclosure has an air exchange rate of at least 4 air changes per hour, and the differential pressure is at least 5 Pascals (-0.02 inches) of water. [OHS General Regs., S.49.20 (3)]
- Provide a vacuum system with HEPA filtration within the unit and HEPA filtration fitted to the exhaust of the unit in all asbestos removal projects using an enclosure. [OHS General Regs., S.49.21]
Asbestos Waste Handling
An asbestos contractor must:
- Make sure the water-saturated asbestos-containing material is removed in small sections and immediately placed in waste containers. [OHS General Regs., S.49.22 (1)]
- Label the waste containers as containing asbestos
- Seal each waste container is immediately after it is full. [OHS General Regs., S.49.22 (1)]
- To dispose of used drop sheets: [OHS General Regs., S.49.22 (2)]
- Wet the drop sheets and place them in the sealed waste containers
- Label the waste containers as containing asbestos,
- Seal each waste container is immediately after it is full.
- Do not reuse drop sheets. [OHS General Regs., S.49.22 (3)]
- Wash the entire outside of a waste container in the asbestos waste transfer room. [OHS General Regs., S.49.22 (4)]
- Place the waste containers in uncontaminated containers in an area outside the asbestos waste transfer room [OHS General Regs., S.49.22 (5)]
- Transport the waste from the asbestos work area to a waste disposal facility that meets the requirements of the Waste Resource Management Regulations under the Environmental Protection Act R.S.P.E.I. 1988, Cap. E-9. Waste from the asbestos work area must be sent as soon as it is practical. [OHS General Regs., S.49.22 (6)]
- Make sure waste from the asbestos work area is transported by workers who have successfully completed an approved asbestos awareness course. [OHS General Regs., S.49.22 (7)]
- Make sure workers transporting the asbestos waste are handling it in a safe manner that will not create a hazard to the health or safety of workers or others at the waste disposal facility site. [OHS General Regs., S.49.22 (8)]
Medical Surveillance Program
The asbestos contractor must:
- Establish a medical surveillance program for all workers who are or will be exposed to airborne asbestos fibres at or above the established threshold limit values. [OHS General Regs., S.49.25 (2)]
- Make sure that any associated costs due to medical exams or servicers from a health care provider are delivered without cost to the worker. [OHS General Regs., S.49.25 (2)]
- Make sure before workers begin their asbestos abatement work, that they have a pre-placement examination which includes: [OHS General Regs., S.49.25 (3)]
- a physical examination, with emphasis on the respiratory system;
- a screening chest radiograph;
- 2 tests of lung function - Forced Expiratory Volume (FEV1) and Forced Vital Capacity (FVC); and
- an occupational exposure history.
- Make sure asbestos abatement workers have their medical records updated as follows:
- Annual lung function tests, including Forced Expiratory Volume (FEV1) and Forced Vital Capacity (FVC);
- annual occupational exposure history; and
- a screening chest radiograph every five years, or every two years if the worker had exposure to airborne fibres of asbestos for more than 20 years. [OHS General Regs., S.49.25 (4)]
Records
An asbestos contractor must maintain an accurate and complete record for each worker for at least 40 years, containing: [OHS General Regs., S.49.26]
- All health examinations reports which assess the worker’s potential exposures, ability to use a respirator, and any specified limitations of use;
- Their detailed work history containing dates and length of jobs performed including types of job and material handled; and
- All training records.
The employer must maintain an accurate record for each worker for at least 40 years, containing: [OHS General Regs., S.49.26]
- Physician’s reports from the routine examinations that have assessed the worker’s potential exposures and limitations;
- Detailed work history, such as dates and length of jobs done, types of job, and material handled; and
- All training records.
Worker responsibilities
As a worker you must:- Follow the safe work practices and procedures that comply with the regulatory requirements.
- Make sure not to eat, drink or smoke in an asbestos work area. [OHS General Regs., S. 49.15 (2)]
- Use the personal protective equipment provided by the employer, and maintain the equipment in good condition.
- Participate fully in an established medical surveillance program.
General Regulations
EC180/87
Part 49 ASBESTOS
Section 49.1 Definitions
49.1 (1) In this Part,
(a) "asbestos" means any of the following asbestiform silicates:
(i) actinolite,
(ii) anthophyllite,
(iii) chrysotile,
(iv) crocidolite,
(v) amosite, or
(vi) tremolite;
(b) "asbestos-containing material" means
(i) material, other than vermiculite insulation, that contains 1 per cent or more asbestos by dry weight, and
(ii) vermiculite insulation;
(c) "asbestos contractor" means the holder of a valid asbestos contractor’s certificate;
(d) "asbestos contractor’s certificate" means a valid asbestos contractor’s certificate granted or deemed to have been granted under section 49.9;
(e) "asbestos warning sign" means a sign posted at the boundaries of an asbestos work area that states
(i) that an asbestos hazard is present,
(ii) that a cancer and lung disease hazard is present,
(iii) that the enclosure is restricted to authorized personnel only, and
(iv) that respiratory protection and protective clothing must be worn in the enclosure;
(f) "asbestos work" means the handling of asbestos or asbestos-containing material, and includes
(i) the removal of asbestos or asbestos-containing material,
(ii) the encapsulation or repair of asbestos or asbestos-containing material, or
(iii) the enclosure of asbestos or asbestos-containing material for the purpose of creating a physical barrier to potential fibre release;
(g) "asbestos work area" means the area in which asbestos work is being prepared for or carried on by an asbestos contractor and the contractor’s workers, and includes any enclosure established by the asbestos contractor or the workers;
(h) "exposure to asbestos" means the exposure of a worker to airborne respirable asbestos fibres originating from asbestos or asbestos-containing material;
(i) "friable asbestos-containing material" means asbestos-containing material that when dry can be crumbled, pulverized or powdered by hand pressure and includes asbestos-containing material that is in a crumbled, pulverized or powdered state;
(j) "HEPA filter" means a high efficiency particulate aerosol filter that has an efficiency of at least 99.97% in containing an aerosol of 0.3 of a micrometre in diameter;
(k) "Threshold Limit Values" means the threshold limit values for asbestos exposure specified by the ACGIH in its publication "Threshold Limit Values and Biological Exposure Indices" adopted under subsection 49.3(3).
(2) In this Part, "Type I Removal Operations" means removal operations that present a minimal risk of releasing asbestos fibres into the air, such as the removal of asbestos-containing material that is nonfriable, work that can be done without damaging the asbestos-containing material, including the use of non-powered handheld tools as long as water is used to control fibre release, and
(a) removal of asbestos-containing material ceiling tiles where the total area to be disturbed is less than 1 square meter without damage;
(b) removal of non-friable asbestos-containing material without damage;
(c) removal of vinyl asbestos floor tile, asbestos cement products, and millboard where water is used to control fibre release; and
(d) removal of less than one square meter of drywall where joint-filling compounds with asbestos-containing material were used.
(3) In this Part, "Type II Removal Operations" means removal operations that present a medium risk of asbestos exposure to workers, such as the removal or minor disturbance of friable asbestos-containing material with a surface area of less than 0.09 of a square meter or 1 square foot during the repair, alteration, maintenance or demolition of all or part of a building, or any machinery or equipment, or where the minor removal or disturbance exceeds the scope of a Type I Removal, including
(a) using a mechanical or electrically powered tool, fitted with a HEPA filter dust collector, to cut, shape or grind non-friable manufactured products containing asbestos;
(b) removing all or part of a false ceiling to gain access to a work area where friable asbestos-containing material is, or is likely to be, lying on the surface of the false ceiling;
(c) removing, encapsulating, enclosing or disturbing a surface area of less than 0.09 of a square meter or 1 square foot of friable asbestos-containing material during the repair, alteration, maintenance, demolition or dismantling of a building, structure, machine, tool or equipment, or parts of any of them;
(d) performing glove bag operations;
(e) dry removal of non-friable asbestos-containing material where the material may be cut, broken, or otherwise damaged during removal; and
(f) removing a surface area of up to 9.3 square meters or 100 square feet of contiguous ceiling tile containing asbestos or sheet vinyl flooring having an asbestos backing.
(4) In this Part, "Type III Removal Operations" means removal operations during the repair, alteration, maintenance or demolition of all or part of any building, machinery or equipment that present the highest risk of asbestos exposure to workers, including
(a) spraying of an encapsulant over friable asbestos using a low-pressure sprayer;
(b) using a power tool not having a dust collection device equipped with a HEPA filter to cut, grind or abrade asbestos-containing material;
(c) any indoor operation involving the removal or stripping of friable asbestos-containing material; and
(d) repairing, altering or demolishing a boiler, furnace or similar device or any part of it that is made in part of asbestos-containing material.
[EC596/90, s. 1; EC2020-147, s. 8]
Section 49.2 Application
49.2 This Part applies to every workplace where asbestos is present.
[EC596/90, s. 1; EC2020-147, s. 8]
Section 49.3 Asbestos in workplace
49.3 (1) No person shall, in a workplace,
(a) use; or
(b) apply or install, or cause to be applied or installed,
any asbestos-containing material.
(2) No person shall remediate, disturb or actively work with asbestos-containing material without the use of an appropriate type of containment to reduce contamination in the atmosphere to or below the threshold limit values.
(3) The 2019 edition of the "Threshold Limit Values and Biological Exposure Indices" published by the ACGIH, as amended from time to time, is adopted and in force with respect to the threshold limit values for exposure to asbestos.
[EC596/90, s. 1; EC2020-147, s. 8]
Section 49.4 Sampling of asbestos-containing material
49.4 (1) An employer or owner of a workplace shall ensure that a competent person
(a) collects representative samples of any materials in the workplace that the employer or the competent person suspects contain asbestos; and
(b) determines whether each of the samples is asbestos-containing material.
(2) When collecting samples of materials in accordance with clause (1)(a), the competent person shall
(a) wear a negative pressure half face piece respirator;
(b) take all reasonable measures to ensure asbestos fibres are not released during the sampling collection process; and
(c) ensure all bulk samples are submitted to an accredited lab for analysis in accordance with industry standards acceptable to the Director.
(3) If an employer or a competent person suspects that a material contains asbestos, the material shall be treated as asbestos-containing material unless the competent person determines that it is not asbestos-containing material.
[EC596/90, s. 1; EC2020-147, s. 8]
Section 49.5 Inventory
49.5 (1) An employer or owner of a workplace shall Inventory
(a) ensure that a competent person prepares an inventory of asbestos-containing material in the workplace;
(b) ensure that the inventory is updated each time asbestos-containing material is repaired or removed from the workplace;
(c) keep the inventory at the workplace; and
(d) at least annually, ensure that the condition of all asbestos-containing material in the workplace is inspected by a competent person.
(2) The inventory prepared under subsection (1) shall
(a) identify the location of the asbestos-containing material in the workplace;
(b) specify the location of any asbestos-containing material that may release asbestos fibres into the atmosphere due to damage or poor repair;
(c) include the date the inventory was prepared and the subsequent dates of review as required in clause (1)(d);
(d) include the name of the competent person completing the inventory; and
(e) provide a general description of the asbestos-containing material, including the type of asbestos and the percentage of the sample that is comprised of asbestos.
[EC596/90, s. 1; EC2020-147, s. 8]
Section 49.6 Management plan
49.6 An employer or owner of a workplace shall ensure that an asbestos management plan is
(a) developed to
(i) prevent asbestos-containing material identified in the inventory under section 49.5 from becoming airborne in the workplace, and
(ii) protect the health and safety of workers if asbestos-containing material becomes airborne in the workplace;
(b) implemented and communicated to the workers so as to ensure that they are made aware of the asbestos management plan and of its contents; and
(c) reviewed at least annually, or more frequently if required by a change in work conditions, and in consultation with the joint health and safety committee, if any, or health and safety representative, if any.
[EC596/90, s. 1; EC2020-147, s. 8]
Section 49.7 Monitoring exposure levels
49.7 (1) Where it is necessary for the protection of workers, an employer or owner of a workplace shall monitor the concentration of airborne asbestos in the workplace and shall monitor the exposure of workers to asbestos by a recognized method approved by the Director.
(2) An employer or owner of a workplace shall
(a) establish and maintain records of the monitoring of the workplace and of the exposure of workers to asbestos-containing material; and
(b) ensure the records are kept for a period of not less than 40 years.
(3) The employer or owner of a workplace shall provide copies of the records required to be established and kept under subsection (2) to the employer’s workers and to their safety committee or safety representative as soon as practicable.
(4) An employer or owner of a workplace shall ensure that
(a) any worker who handles, disturbs or removes asbestos-containing material in the course of the worker’s work activities has successfully completed an asbestos abatement course that includes a review of the provisions of these regulations that apply to asbestos-containing material and that is acceptable to the Director; and
(b) any worker who transports or handles sealed containers of asbestos-containing material for disposal has successfully completed an asbestos awareness course acceptable to the Director.
[EC360/92, s. 1; EC2020-147, s. 8]
Section 49.8 Exposure limits
49.8 (1) An employer, owner and contractor shall take all necessary measures and implement all necessary procedures, by means of engineering controls, work practices and hygiene practices and facilities required by this Part, to ensure that the exposure of a worker to asbestos-containing material in a workplace is reduced to the lowest practical level and, in any case, does not exceed the threshold limit values.
(2) The analysis of asbestos samples shall be performed by a laboratory that is accredited by the Canadian Association for Laboratory Accreditation (CALA) or the American Industrial Hygiene Association (AIHA) Asbestos Analysts Registry (AAR) in accordance with the National Institute of Occupational Safety and Health (NIOSH) Manual of Analytical Methods.
(3) All air tests conducted to confirm asbestos fibres in ambient air in the workplace shall follow the National Institute of Occupational Safety and Health (NIOSH) test methods.
(4) Projects with a Type III Removal Operations enclosure shall be subject to daily air sampling of the ambient air outside the enclosure to determine the exposure of any worker to asbestos.
(5) For projects conducted as Type II and Type III Removal Operations, following the final clean-up requirements, and prior to the removal of an enclosure, a visual inspection of the work area inside the enclosure shall be carried out by a competent person and confirmed with a final clearance air sample.
[EC596/90, s. 1; EC360/92, s. 1; EC2020-147, s. 8]
Section 49.9 Asbestos contractor’s certificate
49.9 (1) No person shall undertake asbestos work unless the person is the holder of a valid asbestos contractor’s certificate.
(2) A person may apply for an asbestos contractor’s certificate by submitting to the Director an application in the form required by the Director containing the information and other requirements specified in subsection (3).
(3) An applicant for an asbestos contractor’s certificate shall provide for the purposes of the application referred to in subsection (2)
(a) a copy of the applicant’s current asbestos work procedure manual that
(i) is to be used in the asbestos work the applicant proposes to carry out under the authority of the certificate,
(ii) includes a copy of the applicant’s Respiratory Protection Program, as required by the CSA Standard Z94.4-18, "Selection, Use, and Care of Respirators", and
(iii) is satisfactory to the Director;
(b) proof satisfactory to the Director that any workers the applicant intends to engage to carry out the asbestos work have successfully completed a course in asbestos abatement acceptable to the Director;
(c) confirmation that the applicant has or has access to the equipment necessary to perform the asbestos work in accordance with the contractor’s procedure manual referred to in clause (a) and this Part;
(d) proof satisfactory to the Director that the applicant has at least one competent person to supervise the asbestos work to be undertaken by the applicant;
(e) confirmation that the applicant has implemented a worker medical surveillance program that meets the requirements set out in section 49.25; and
(f) confirmation that the applicant has established and will maintain the records required by section 49.26.
(4) The Director may grant an asbestos contractor’s certificate to an applicant where the Director is satisfied that
(a) the applicant has submitted an application in accordance with subsection (2); and
(b) the applicant has met the requirements of subsection (3).
(5) A certificate issued under subsection (4) shall be subject to any terms and conditions in respect of the type of asbestos work that may be undertaken by the certificate holder that the Director considers appropriate.
(6) Subject to subsections (7) and (8), a certificate expires on the earlier of
(a) five years from the date of issue; or
(b) the sale of the business for which it was issued.
(7) A certificate in respect of which no notification has been provided under section 49.10 for a period of three years expires at the end of the three-year period.
(8) A certificate that was issued under this Part as it read immediately prior to the coming into force of this subsection and that was valid and in force on the coming into force of this subsection is deemed to be a certificate under this section according to its terms for a period of two years.
(9) No person shall transfer a certificate to any other person or business.
[EC596/90, s. 1; EC2020-147, s. 8]
Section 49.10 Requirements before commencing work
49.10 (1) Before commencing any asbestos work, an asbestos contractor shall provide written notification respecting the asbestos work to the Director, in the form required by the Director and containing the information specified in subsection (2).
(2) The written notification referred to in subsection (1) shall be provided to the Director at least three business days prior to the planned asbestos work, shall be signed by the asbestos contractor or a competent person who is authorized to represent the asbestos contractor, and shall include
(a) a description of the asbestos work to be performed that shows that it is adequately covered by specific procedures in the asbestos work procedure manual submitted under clause 49.9(3)(a) or, if the manual does not contain the necessary procedures, the new procedures developed by the asbestos contractor to accommodate the particular needs of the asbestos work;
(b) the names of the workers who will perform the asbestos work and confirmation that those workers have successfully completed a course in asbestos abatement acceptable to the Director;
(c) confirmation of the name of the competent person who will be supervising the asbestos work and proof satisfactory to the Director that the person is competent to supervise the asbestos work;
(d) confirmation that the workers named in clause (b) have participated in a medical surveillance program acceptable to the Director.
(3) On receipt of the notification required under subsection (1), an officer shall review the notification and may, if satisfied with the information provided, issue a permit to the asbestos contractor to undertake the asbestos work.
(4) The asbestos contractor shall carry out the asbestos work in accordance with the information provided in the notification.
[EC596/90, s. 1; EC2020-147, s. 8]
Section 49.11 Suspension or cancellation
49.11 (1) The Director may suspend or cancel an asbestos contractor’s certificate for any contravention by the asbestos contractor or by the workers of the asbestos contractor of any provision of the Act, these regulations or any other regulations made under the Act.
(2) A suspension under this section may be for a specified period of time and subject to any conditions that the Director considers appropriate.
(3) Where an asbestos contractor’s certificate is suspended or cancelled by the Director under subsection (1), any approval for asbestos work that has not been commenced, or that has been commenced but not completed, is also cancelled.
[EC596/90, s. 1; EC2020-147, s. 8]
Section 49.12 Product analysis
49.12 (1) Prior to the submission of the written notification and commencement of any asbestos work, the asbestos contractor shall ascertain the type and content of asbestos or asbestos-containing material present in the asbestos work area by
(a) referring to the inventory described in the asbestos management plan prepared according to section 49.6; or
(b) by having a competent person obtain a sample or samples to submit to an accredited laboratory for the determination of its asbestos type and content, if any.
(2) Where an asbestos contractor is required to obtain a sample under subsection (1) for the determination of its asbestos content, the asbestos contractor shall take all reasonable measures to ensure respirable asbestos fibres are not released during the sampling process.
[EC596/90, s. 1; EC2020-147, s. 8]
Section 49.13 Protective clothing
49.13 (1) Where a worker’s personal clothing may become contaminated with asbestos-containing material, the asbestos contractor shall provide and pay for appropriate protective clothing that meets the requirements of this section.
(2) The asbestos contractor shall ensure that all workers within an asbestos work area
(a) wear protective clothing referred to in subsection (1) that
(i) is made of material resistant to penetration by asbestos fibres, and
(ii) covers the head and fits snugly at the neck, wrists, ankles and elsewhere as necessary to protect against the risk of exposure to asbestos fibres; and
(b) use footwear that is impermeable to asbestos fibres.
(3) A worker who is engaged in asbestos work for which the worker is provided with protective clothing in accordance with this section shall not wear or remove the protective clothing from inside to outside of the asbestos work area.
[EC596/90, s. 1; EC2020-147, s. 8]
Section 49.14 Respiratory protection
49.14 (1) An asbestos contractor shall provide, and ensure that workers use, within an asbestos work area, respirators which are appropriate for the level of risk of the anticipated exposure to asbestos fibres.
(2) An asbestos contractor shall ensure that the respirators provided to workers are selected, used, cleaned, stored, maintained, inspected and tested in accordance with the relevant provisions of CSA Standard Z94.4-18 , "Selection, Use, and Care of Respirators".
[EC596/90, s. 1; EC2020-147, s. 8]
Section 49.15 Asbestos work area, boundaries
49.15 (1) An asbestos contractor shall, prior to the commencement of asbestos work, ensure that
(a) the boundaries of the asbestos work area are identified and marked by barricades, fences or similar means;
(b) asbestos warning signs are posted at the boundaries of the asbestos work area which meet the requirements of clause 49.1(1)(e);
(c) the permit issued under subsection 49.10(3) is posted;
(d) the immediate work area is cleared of objects, materials and equipment other than those required to do the work; and
(e) the windows, doorways and all other openings are adequately secured to prevent the release of asbestos fibres into other work areas.
(2) No person shall eat, drink or smoke in an asbestos work area.
[EC596/90, s. 1; EC2020-147, s. 8]
Section 49.16 Sealants
49.16 (1) Subject to subsection (3), no person shall apply a liquid sealant to encapsulate friable asbestos-containing material in a workplace if, in the opinion of an officer,
(a) the friable asbestos-containing material has visibly deteriorated; or
(b) the friable asbestos-containing material’s strength and its adhesion to its underlying materials and surfaces are insufficient to support both the weight of the asbestos-containing material and the sealant.
(2) An asbestos contractor may use an encapsulant to prevent the release of asbestos-containing material into the ambient air of the workplace where
(a) the use of encapsulation as a means of dealing with asbestos-containing material is not prohibited pursuant to subsection (1); and
(b) in the opinion of an officer, the persons who ordinarily occupy the workplace can do so safely if the asbestos-containing material that is allowed to remain in place is encapsulated.
(3) Where, in the opinion of an officer, there is a potential risk that asbestos fibres may be released into the ambient air due to the condition or friable nature of the asbestos-containing material, the officer may order the employer
(a) to seal the asbestos-containing material with an encapsulant, either penetrating or bridging; or
(b) to remove the asbestos-containing material.
[EC596/90, s. 1; EC2020-147, s. 8]
Section 49.17 General
49.17 (1) An asbestos contractor shall take every reasonable precaution to prevent the release of asbestos fibres into the ambient air of the workplace, and for that purpose may use an enclosure constructed in accordance with the approved asbestos work procedure manual submitted to the Director under clause 49.9(3)(a).
(2) An enclosure purposely built for asbestos work shall effectively contain the asbestos fibres that may be released during a Type I, Type II, or Type III Removal Operations.
(3) An asbestos contractor may apply to the Director not less than five days prior to the commencement of work for approval of a variance from the enclosure requirements specified in the approved asbestos work procedure manual referred to in subsection (1) by submitting a proposal that
(a) specifies the changes in procedures, equipment or materials to be used during the asbestos work; and
(b) demonstrates to the satisfaction of the Director that the variance will result in an enclosure that meets the requirements of subsection (2).
(4) An asbestos contractor shall ensure asbestos work is conducted in a manner that does not create a risk to the health or safety of any person.
(5) An asbestos contractor shall not dismantle the enclosure of an asbestos work area unless the final clearance air sample required under subsection 49.8(5) is within the threshold limit values.
[EC596/90, s. 1; EC2020-147, s. 8]
Section 49.18 Enclosure entry
49.18 (1) Where asbestos work is in progress, an employer shall ensure that only workers who have successfully completed the training courses referred to in subsection 49.7(4) are permitted to enter the enclosure.
(2) Prior to entering a full enclosure where asbestos work is taking place, a worker shall
(a) remove all street clothing and leave the clothing in the clean area of the asbestos work area;
(b) put on clean disposable protective clothing; and
(c) wear a respirator as required in subsection 49.14(1).
[EC596/90, s. 1; EC2020-147, s. 8]
Section 49.19 Worker exit decontamination procedure
49.19 After a worker completes asbestos work in a contaminated work area, or when the worker leaves the contaminated work area for any reason, the worker shall
(a) remove all loose asbestos fibres from protective clothing with the vacuum system while still in the contaminated work area room of the full enclosure;
(b) enter the worker transfer room of the full enclosure and remove all protective clothing except the respirator, and place the clothing in the waste container provided for that purpose;
(c) enter the shower room of the enclosure and thoroughly shower before removing the respirator;
(d) adequately clean the respirator while in the shower; and
(e) enter the worker change room to dry and dress in street clothing.
[EC596/90, s. 1; EC2020-147, s. 8]
Section 49.20 General
49.20 (1) An asbestos contractor shall ensure that each enclosure is equipped with a ventilation system for the purpose of asbestos work that is sufficient to ensure that the enclosure is under adequate negative pressure to prevent the release of respirable asbestos fibres into the air outside the enclosure.
(2) If exhaust ventilation equipment is used to contain asbestos fibres, an asbestos contractor shall ensure that the equipment is
(a) of a type designed and solely used for asbestos abatement procedures;
(b) equipped with a HEPA filter;
(c) maintained in good working condition and inspected regularly in accordance with the manufacturer’s specifications; and
(d) certified by a competent person not less than once a year as being able to function safely and effectively.
(3) An asbestos contractor shall ensure that the capacity of the ventilation system used in an enclosure is such that the air exchange rate is a minimum of 4 air changes per hour, and the differential pressure is at least 5 Pascals (-0.02 inches) of water.
[EC596/90, s. 1; EC2020-147, s. 8]
Section 49.21 Vacuum cleaner
49.21 An asbestos contractor shall provide a vacuum system with HEPA filtration within the unit and HEPA filtration fitted to the exhaust of the unit for use when performing all types of asbestos removal where an enclosure is present.
[EC596/90, s. 1; EC2020-147, s. 8]
Section 49.22 Mode of removal
49.22 (1) An asbestos contractor shall ensure that water-saturated asbestos-containing material is removed in small sections and immediately placed in waste containers that are labelled as containing asbestos and that each waste container is sealed when filled.
(2) An asbestos contractor shall ensure that drop sheets are wetted and placed in the sealed containers as part of the asbestos waste handling method specified in subsection (1).
(3) Drop sheets referred to in subsection (2) shall not be reused.
(4) An asbestos contractor shall ensure that the exterior surfaces of waste containers are adequately cleaned in the asbestos waste transfer room of the enclosure.
(5) An asbestos contractor shall ensure that waste containers are placed in uncontaminated containers in an area outside the asbestos waste transfer room of the enclosure.
(6) An asbestos contractor shall ensure that asbestos waste is transported as soon as practicable to a waste disposal facility that meets the requirements of the Waste Resource Management Regulations under the Environmental Protection Act R.S.P.E.I. 1988, Cap. E-9.
(7) An asbestos contractor shall ensure that a worker who transports asbestos waste has successfully completed an asbestos awareness course referred to in clause 49.7(4)(b).
(8) The worker referred to in subsection (7) shall ensure that the asbestos waste is handled in a manner that will not create a hazard to the health or safety of workers or other individuals at the waste disposal facility site.
[EC596/90, s. 1; EC2020-147, s. 8]
Section 49.23 Demolition
49.23 An employer shall ensure that materials with the potential of releasing asbestos fibres into the atmosphere are removed before proceeding with
(a) the demolition of a building or structure; and
(b) the demolition of all or part of any machinery, equipment, aircraft, vehicle or vessel.
[EC596/90, s. 1; EC2020-147, s. 8]
Section 49.24 Emergency response
49.24 An asbestos contractor shall develop emergency response procedures to be used in the event of serious injury and other emergencies in an asbestos work area.
[EC596/90, s. 1; EC2020-147, s. 8]
Section 49.25 Program
49.25 (1) An asbestos contractor shall implement a medical surveillance program for all workers who are or will be exposed to airborne fibres of asbestos at or above the threshold limit values.
(2) The asbestos contractor shall ensure that all medical examinations and procedures are performed by or under the supervision of a health care provider, and shall be provided without cost to the worker.
(3) Before an asbestos abatement worker commences work, the worker shall undergo the following components of a pre-placement examination:
(a) a physical examination, with emphasis on the respiratory system;
(b) a screening chest radiograph;
(c) a lung function test, including
(i) Forced Expiratory Volume (FEV1),
(ii) Forced Vital Capacity (FVC);
(d) an occupational exposure history.
(4) A periodic medical examination shall include
(a) an annual lung function test that meets the requirements of clause (3)(c);
(b) an annual occupational exposure history; and
(c) a screening chest radiograph every five years or every two years if the worker had exposure to airborne fibres of asbestos for more than 20 years.
[EC596/90, s. 1; EC2020-147, s. 8]
Section 49.26 Worker record
49.26 (1) An asbestos contractor shall establish and maintain an accurate and complete record for each worker, containing
(a) the reports from examinations performed which assess the worker’s potential exposures, ability to use a respirator, and any specified limitations of use;
(b) a detailed work history containing dates and length of jobs performed including types of job and material handled; and
(c) the worker’s training records.
(2) An asbestos contractor shall ensure that all worker records required under subsection (1) shall be maintained for a period of not less than 40 years.
[EC596/90, s. 1; EC2020-147, s. 8]