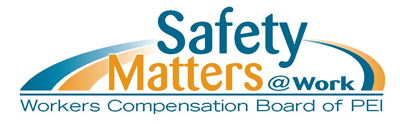


Personal Protective Equipment
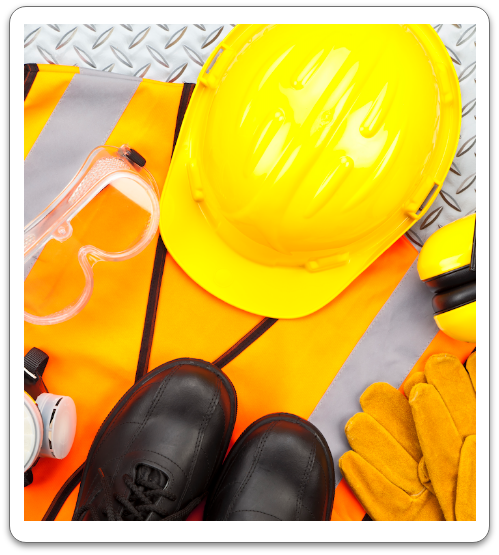
[OHS General Regs., S. x] Follow these links
to related legislation.
Highlighted words reveal
definitions and supplementary
information when selected.
Personal protective equipment (PPE) is an essential safety component of a worker's tasks when there is potential of injury as a result of an exposure or where a physical, chemical, or biological hazard exists and cannot be controlled otherwise. PPE is designed to protect a worker from possible harm and is required by workplace legislation. It is a control mechanism for an identified hazard; it only protects a worker when used properly and should only be considered as a last means of protection. Alternative options for controlling the hazard, such as removing or engineering out the hazards, should be tried before providing PPE for protection.
Hazard Control
The main ways to control a hazard include:
- Elimination (including substitution): remove the hazard from the workplace, or substitute (replace) with less hazardous options.
- Engineering Controls: includes designs or modifications to plants, equipment, ventilation systems, and processes that reduce the source of exposure.
- Administrative Controls: controls that alter the way the work is done, including timing of work, policies and other rules, and work practices such as standards and operating procedures.
- Personal Protective Equipment: equipment worn by individuals to reduce exposure such as contact with chemicals or exposure to noise.
These methods are also known as the "hierarchy of control". The hierarchy should be considered in the order presented (it is always best to try to eliminate the hazard first, etc.).
Employer duties
When PPE is being used, the employer is responsible for:
- Making sure workers’ clothing or accessories do not become a hazard in the workplace. Loose clothing or jewellery can get caught in machinery or become a choking hazard in certain situations. [OHS General Regs., S. 45.1]
- Keeping personal protective equipment in good condition. [OHS General Regs., S. 45.2]
- Providing workers who require PPE with instruction about their PPE so they understand its use, limitations, and maintenance requirements. Instruction must happen before the workers begin using their PPE. [OHS General Regs., S. 45.3]
- Making sure workers using PPE, test their equipment before each use. [OHS General Regs., S. 45.4]
- Making sure no one uses defective PPE. [OHS General Regs., S. 45.4]
- Making sure workers handling or using acids, caustics, steam, abrasives, hot fluid jets, or similar harmful substances use suitable PPE. Other measures can be used if they will protect against these hazards. [OHS General Regs., S. 45.14]
General requirements
- Making sure workers wear head protection that meets the specifications of CSA Standard Z94.1-15 Industrial Protective Headwear - Performance, Selection, Care and Use if they are at risk of a head injury. Note that the headwear should be chosen considering the individual hazards at each workplace. [OHS General Regs., S. 45.5]
- Fitting protective headwear with chinstraps in high winds or other conditions which might cause workers to lose their headwear. Employers may also use other effective methods to secure the protective headwear. [OHS General Regs., S. 45.6]
Head protection
- Making sure workers, who are exposed to hazards that may irritate or injure the eyes or face, wear eye protection. Further, making sure a worker with 20/200 vision in either eye or blind in either eye wears eye protection. All eye protection must meet the specifications of the CSA Standard Z94.3-15 Eye and Face Protectors or another standard offering equal protection. [OHS General Regs. S. 45.7] [OHS General Regs., S. 45.8]
- Making sure workers are not wearing contact lenses.
- While welding, [OHS General Regs., S. 45.11]
- When there are gases, vapours or other materials in the work area that could harm the eyes when absorbed by the worker’s contact lenses, or
- When there is dust or other materials present that could harm the eyes or cause the worker to be distracted. [OHS General Regs., S. 45.10]
Eye protection
- Making sure workers wear PPE if the worker is handling materials that may puncture, abrade, or irritate hands or arms, except if the PPE would become an equal or greater hazard. [OHS General Regs., S. 45.13]
Hand protection
- Making sure workers wear foot protection that meets the specifications of CSA Standard Z195-14 Protective Footwear, footguards, or other devices that provide equal protection if they are at risk of a foot injury. Do not allow workers to use protective footwear that has become too worn to protect the foot as intended. [OHS General Regs., S. 45.15] [OHS General Regs., S. 45.16]
Foot protection
- Using mechanical methods and engineering solutions such as ventilation to prevent workers from being exposed to contaminants at harmful concentrations or air with hazardously low levels of oxygen. If this is not possible or highly impractical, make sure every workers exposed wears protective respiratory equipment that meet specifications set out in CSA Standard Z94.4-18 Selection, Use, and Care of Respirators, including amendments, or another standard offering equal protection. [OHS General Regs., S. 45.17]
- Making sure during temporary or emergency conditions only, every worker being exposed is wearing protective respiratory equipment. [OHS General Regs., S. 45.18]
- Making sure any provided air for the respiratory protective equipment meets the applicable specifications set out in CSA Standard Z180.1-19 Compressed Breathing Air and Systems. [OHS General Regs., S. 45.18]
- Making sure the selected respiratory protective equipment for filtering particulate matter meets the applicable standards and specifications set out in CSA Standard Z94.4.1:21, "Performance of Filtering Respirators," or a standard offering equivalent protection. [OHS General Regs., S. 45.18 (3)]
- Making sure workers using a respirator are clean shaven where the respirator seals with the face. [OHS General Regs., S. 45.19]
- Posting signs in work areas with harmful concentrations of air contaminants or hazardously low levels of oxygen. The signs must specify: [OHS General Regs., S. 45.20(1)]
- The hazards that exist in the area.
- The required personal protective equipment.
- Making sure that sufficient workers trained in rescue procedures are immediately available whenever workers are working in areas where an oxygen deficient atmosphere or harmful concentrations of air contaminants exist or are likely to develop. [OHS General Regs., S. 45.20(2)(a)]
- Making sure the rescue workers have immediate access to appropriate respirators or other aids necessary for rescue. [OHS General Regs., S. 45.20(2)(b)]
- Making sure where a worker is wearing an approved air-line or approved air-hose type respirator in an atmosphere immediately harmful to the worker: [OHS General Regs., S. 45.20(3)]
- The air supply source be attended by another worker with the equipment necessary to rescue if the worker is rendered unconscious or otherwise injured; and
- Provide the worker to carry an auxiliary supply of compressed air of sufficient capacity to enable the worker to escape from the area during an emergency or until rescue begins.
Respiratory protection
- Appropriate protection to protect workers from direct sunlight include wearing sunscreen, a hat (that keeps direct sunlight off the head and face area), and sunglasses or goggles that protect the eyes.
Sun Protection
- Providing personal floatation devices to workers at risk of drowning except workers who are protected from falling to water by other safety measures, a worker who is a lifeguard on duty, or the worker is performing occupational diving tasks. [OHS General Regs., S. 45.4.1] [Fall Protection Regs., S. 10(1)] [Fall Protection Regs., S. 10(5)]
- Making sure these devices are worn under conditions that involve a risk of drowning [OHS General Regs., S. 45.4.1(1)] [Fall Protection Regs., S. 10(2)]
- Making sure the lifejacket or personal flotation device are suitable to the conditions in the workplace and of the correct size and weight of the worker who wears it. [OHS General Regs., S. 45.4.1(1)]
- Noting that:
- Life jackets are intended to provide buoyancy that will turn the wearer face-up on entry to water and keep that person in that position. [OHS General Regs., S. 45.01]
- Personal floatation devices will support a conscious person in an upright or backward-leaning position in water. [OHS General Regs., S. 45.01]
- Both devices must be approved by Transport Canada, or an another agency permitted by TC to approve such devices, and must bear an approval mark or label. [OHS General Regs., S. 45.01]
- Making sure devices are inspected and maintained according to the manufacturer’s instructions and recommendations and must keep records for the life of the lifejacket or device. [Fall Protection Regs., S. 10(3)] [OHS General Regs., S. 45.4.2]
Life Jacket or – Personal Flotation Device
Specific situations
PPE is also required under specific situations including:
- Power tools: eye protection, dust type respirators when buffing, grinding, sanding. [OHS General Regs., S.29.7]
- Welding: adequate fire retardant work clothing including gauntlet type gloves and arm protection, apron or other materials. Adequate eye and face protection against radiation, molten metal, chips or when grinding welds, safety footwear (boots), [OHS General Regs., S. 37.9] and respirators if tests of air samples indicate respirators are required. [OHS General Regs., S. 37.10]
- In tanks and vessels: respirators when air supply cannot be confirmed. [OHS General Regs., S. 40.3]
- Forest operations: at all times, safety footwear and safety hat. As required, eye protection or safety screens, protective clothing (e.g., safety pants, gloves or mitts) and hearing protection. [OHS General Regs., S. 41.6]
- Chain saw operation: hearing protection, safety eyewear, safety pants, hard hat, and safety footwear (boots). [OHS General Regs., S. 41.8] Safety gloves or mitts are required when sharpening a chain saw [OHS General Regs., S. 41.21], puncture-resistant safety mitts or gloves when handling wire cable. [OHS General Regs., S. 41.32] Choker men or workers require mitts or gloves of leather or nylon when handling wire cables. [OHS General Regs., S. 41.67]
- Storage battery rooms: acid resistant gloves, aprons, goggles or face shields, and straps for carrying car or truck batteries, and when handling storage batteries or electrolyte. [OHS General Regs., S. 44.2] [OHS General Regs., S. 44.3]
- Asbestos: work clothing which must not be worn outside of the workplace (e.g., disposable clothing such as full body coveralls), respirators, including air purifying or supplied air. [OHS General Regs., S. 49.14] [OHS General Regs., S. 49.15]
- Excavations, trenches and construction: safety hats and safety footwear. [OHS General Regs., S.12.3]
- Traffic Control: as required, including safety footwear, hard hat, safety vest, eye protection and rain wear. [OHS General Regs., S. 50.6]
- Non-ionizing radiation: goggles, face shields or other adequate eye protection. [OHS General Regs., S. 10.2]
- Electrical work: rubber gloves with the appropriate rating. [OHS General Regs., S. 36.5] [OHS General Regs., S. 36.17]
Be aware that other regulations have specific requirements for personal protective equipment, such as the Fall Protection Regulations.
Worker duties
Workers are responsible for,
- Working safely and following health and safety rules.
- Participating in all training so they have a full understanding of the need for their PPE and how to use it safely.
- Properly, and consistently, wearing required PPE.
- Testing their PPE before each use and making sure it is not defective. [OHS General Regs., S. 45.4]
- Notifying the employer immediately if they are planning to wear contact lenses while at work. [OHS General Regs., S. 45.9] Workers cannot wear contact lenses while welding or in other specified situations. [OHS General Regs., S. 45.11]
- Not using protective footwear that is too worn to protect the foot as intended. [OHS General Regs., S. 45.16(1)]
- Shaving where a respirator seals with their face, if they are using a respirator and have facial hair. [OHS General Regs., S. 45.19]
- Ensuring properly fitted PPE is used and maintained as per the manufacturer’s instructions and recommendations.
To access these, you must first create an account with "CSA Communities".
Go to: https://community.csagroup.org/login.jspa?referer=%252Findex.jspa
Once you are logged in, click on the text below the "OHS Standards / View Access" graphic.
Click on the jurisdiction of your choice to see the CSA Standards as referenced in that legislation.
Standards may also be purchased from CSA Group: https://store.csagroup.org/
Fall Protection Regulations
EC2004-633
PART 8 - MEASURES REQUIRED WHERE RISK OF DROWNING
Section 10 Risk of drowning
10. (1) Where a worker is exposed to the hazard of falling from a work area and there is a risk of drowning if the worker does fall, the employer shall
(a) provide to the worker a lifejacket or personal floatation device where the work area is less than 3 m above the surface of the water;
(b) provide rescue equipment that includes
(i) an adequate boat to ensure a safe and timely rescue,
(ii) a life buoy attached with 15 m of rope that is at least 10 mm in diameter and that is made from polypropylene or other material that provides an equivalent level of protection,
(iii) a boat hook,
(iv) an audible alarm system to notify of an accident and to initiate the rescue procedure; and
(c) ensure that workers who are
(i) designated to perform specific rescue tasks,
(ii) properly informed as to the proper rescue procedures, and
(iii) trained in the use of the rescue equipment in order to perform rescue operations in a safe manner,
are available in such numbers as are needed in the circumstances to perform rescue operations safely.
(2) Where, in accordance with subsection (1), an employer provides a worker with a lifejacket or personal floatation device, the worker shall wear the personal floatation device while the worker is in the work area.
(3) Where inflatable lifejackets or personal flotation devices are used, the employer shall ensure that
(a) the lifejackets and devices are inspected and maintained in accordance with the manufacturer’s instructions and recommendations; and
(b) records of all inspections and maintenance are maintained for the life of the lifejacket or device.
(4) Where work is being performed above water that has a fast current and where it is practicable, an employer shall ensure that a line is placed across the water that
(a) is at least 10 mm in diameter or is made of polypropylene or other material that provides an equivalent level of protection; and
(b) has a buoy or some other flotation device attached.
(5) For greater certainty, an employer is not required to provide a worker with a lifejacket or personal floatation device under subsection (1) where the worker is protected by a means of fall protection in accordance with subsection 2(1).
[EC2021-125, ss. 3, 9]
General Regulations
EC180/87
Part 10 NON-IONIZING RADIATION
Section 10.2 Infra-red radiation
10.2 (1) The employer shall ensure that all sources of intense infrared radiation are shielded as near the source as possible by heat absorbing screens, water screens, or other suitable devices.
(2) The employer shall ensure that workers are provided with and all workers shall wear properly fitting goggles, face shields, or other adequate eye protection when entering an area where they may be subjected to heat rays liable to injure or irritate the eyes.
[EC2021-126, s. 3]
Part 12 EXCAVATIONS, TRENCHES AND CONSTRUCTION
Section 12.3 Safety requirements before entry
12.3 The employer shall ensure that workers are not allowed to enter an excavation or trench 1 219 mm (4 ft.) or more in depth, and workers shall not enter unless
(a) the requirements of section 12.2 are complied with;
(b) CSA approved safety headwear and footwear are provided and worn by the workers, as specified in sections 45.5 or 45.15, as the case may be;
(c) ladders, extending at least 914 mm (3 ft.) above the excavation or trench are installed and located no more than 15 240 mm (50 ft.) from where workers are working or other safe means of access and egress are provided;
(d) the sides and crests have been scaled down to prevent loose material from falling into the excavation or trench.
[EC2021-126, ss. 3, 20]
Part 29 HAND TOOLS AND PORTABLE POWER TOOLS
Section 29.7 Responsibilities of worker, power tools
29.7 The worker shall
(a) wear eye protection when using power tools;
(b) wear dust type respirators while buffing, grinding or sanding material which produces harmful dusts;
(c) disconnect the source of power from power tools before changing accessories;
(d) keep all guards on power tools in place while the tool is in use;
(e) protect flexible shafts of flexible tools against denting and kinking which may damage the inner core;
(f) when starting the motor of a flexible shaft tool, hold the tool end firmly to prevent whipping.
[EC2021-126, s. 3]
Part 36 ELECTRICITY
Section 36.5 Protective devices
36.5 (1) The employer shall ensure that workers do not work on energized electrical conductors or equipment unless adequate protective devices specified for protection against the voltage involved are used.
(2) When working on energized electrical conductors or equipment operating at a potential greater than 120 v nominal up to and including 5,000 v phase to phase, the employer shall provide and the worker shall use rubber gloves having a minimum rating of 10,000 v, shields and other necessary safety equipment.
(3) When working on energized electrical conductors or equipment in excess of 5,000 v, and not exceeding 15,000 v phase to phase, the employer shall provide and the worker shall wear rubber gloves having a minimum rating of 20,000 v or use adequate hot line tools.
(4) Rubber gloves shall be tested at least twice a year and replaced as required.
(5) Rubber gloves shall be worn at all times while working on energized circuits in accordance with section 36.6 or while within the primary zone on any poles or structure carrying over 120 v phase to ground to 25000 phase to phase circuits.
(6) In subsection (5), "primary zone" means the distance measured from a high voltage (120 v phase to ground and 25000 phase to phase) source to a suitable distance of clearance measured down or away from the pole or structure to the top of the worker's head, which in all cases shall be 1 200 mm (4 ft.) measured to the nearest live point and all insulator porcelain is to be considered energized.
[EC2021-126, s. 3]
Section 36.17 Protective measures
36.17 The employer shall ensure that workers required to perform such work as described in section 36.16 shall, and workers required to perform the work as described in section 36.16 shall
(a) wear adequate rubber gloves;
(b) use cant hooks or other approved controlling devices; and
(c) not get on or off the lifting machine until the pole is in a secured position.
[EC2021-126, s. 3]
Part 37 WELDING
Section 37.9 Safety clothing
37.9 The employer shall ensure that all workers engaged in welding or cutting operations wear, and all workers shall wear
(a) adequate fire retardant work clothing;
(b) fire retardant gauntlet type gloves and arm protection;
(c) an apron of fire retardant or other adequate materials;
(d) adequate eye and face protection against harmful radiation, or particles of molten metal, or while chipping and grinding welds; and
(e) safety boots which meet the requirements of section 45.15.
[EC2021-126, s. 3]
Section 37.10 Respirators
37.10 Approved respirator equipment shall be worn if tests of air samples indicate it is necessary.
Part 40 TANKS AND VESSELS
Section 40.3 Toxic fumes, precautions
40.3 No worker shall enter any tank, vessel or chamber that may contain toxic fumes or gases until it has been ascertained that the air contained therein is sufficiently pure. In doubtful cases, approved air-supply respirators and lifelines shall be stationed at the entrance to assist those who may become distressed.
[EC2021-126, s. 3]
Part 41 FOREST OPERATIONS
Section 41.6 Protective equipment
41.6 A worker shall
(a) at all times while on a logging worksite, wear an approved safety headwear and approved safety footwear;
(b) if likely to be exposed to eye injury due to flying particles or other harmful substance, wear safety screens or safety eyewear; and
(c) wear other protective clothing, such as safety pants and safety gloves or mitts, and approved hearing protection appropriate to the type of work to be performed.
[EC2021-126, ss. 37]
Section 41.8 Chain saw operation
41.8 When operating a chain saw, the employer shall ensure that the worker wears and the worker shall wear approved hearing protection, safety eyewear, safety pants, a hard hat and safety boots.
[EC2021-126, s. 3]
Section 41.21 Safety gloves
41.21 A worker shall wear safety gloves or mitts while sharpening a chain saw.
[EC2021-126, s. 3]
Section 41.32 Handling wire cable
41.32 The worker shall wear puncture-resistant safety mitts or gloves when handling wire cable.
[EC2021-126, s. 3]
Section 41.67 Choker men
41.67 Choker men or workers handling wire cables shall wear mitts or gloves of leather or nylon safety gloves.
[EC2021-126, s. 3]
Part 44 STORAGE BATTERY ROOMS
Section 44.2 Safety equipment
44.2 The employer shall provide and shall instruct the worker to wear acid resistant gloves, aprons, goggles or face shields and straps for carrying car or truck batteries when handling storage batteries or electrolyte.
[EC2021-126, s. 3]
Section 44.3 Safety equipment
44.3 The worker shall wear acid resistant gloves, aprons, and goggles or face shields and use appropriate carrying straps when handling storage batteries or electrolyte.
[EC2021-126, s. 3]
Part 45 PERSONAL PROTECTIVE EQUIPMENT
Section 45.01 Definitions
45.01 In this Part,
(a) "lifejacket" means a device that
(i) provides a specified buoyancy that will turn the wearer face-up on entry to water and keep the wearer in that position, and
(ii) is approved by Transport Canada, or an agency permitted by Transport Canada to approve lifejackets, and bears a mark or label indicating that approval;
(b) "personal flotation device" means a device that
(i) provides a specified buoyancy that will support a conscious device person in an upright or backward-leaning position in water, and
(ii) is approved by Transport Canada, or an agency permitted by Transport Canada to approve personal flotation devices, and bears a mark or label indicating that approval;
(c) "personal protective equipment" means equipment worn or used by a person for the protection of that person from health or safety hazards that may exist at a workplace.
[EC2021-126, s. 39; EC2024-600, s. 19]
Section 45.1 Wearing apparel
45.1 The employer shall ensure that the personal wearing apparel of a worker shall be of a type and condition that will not expose the worker to any unnecessary and avoidable hazards.
[EC2021-126, s. 3]
Section 45.2 Maintenance
45.2 The employer shall ensure that personal protective equipment is maintained in good condition.
Section 45.3 Instruction
45.3 Every employer shall ensure that every worker who is required to use personal protective equipment shall be given pre-job instruction by the employer to understand its use, its limitations, and its maintenance requirements, as far as these relate to its correct use by the worker.
[EC2021-126, s. 3]
Section 45.4 Testing
45.4 A worker wearing or using personal protective equipment shall test the equipment before each use and shall not wear or use any equipment the worker has reason to believe is defective.
[EC2021-126, s. 3; EC2024-600, s. 20]
Section 45.4.1 Flotation device, when required
45.4.1 (1) An employer shall ensure that a worker who is employed under conditions that involve a risk of drowning is provided with and wears at all times a lifejacket or personal flotation device that is Flotation device, when required
(a) suitable to the conditions in the workplace; and
(b) of the correct size and appropriate for the weight of the worker who will wear it.
(2) Subsection (1) does not apply if
(a) other sufficient safety measures are in place to protect a worker from falling into water, including but not limited to a guardrail or safety net installed and used in accordance with the relevant requirements of Part 2 of the Fall Protection Regulations (EC633/04) made under the Act;
(b) the worker is a lifeguard on duty; or
(c) the worker is performing occupational diving tasks.
[EC2021-126, s. 40]
Section 45.4.2 Maintenance
45.4.2 Where inflatable lifejackets or personal flotation devices are used, the employer shall ensure that
(a) the lifejackets and devices are inspected and maintained in accordance with the manufacturer’s instructions and recommendations; and
(b) records of all inspections and maintenance are maintained for the life of the lifejacket or device.
[EC2021-126, s. 40]
Section 45.5 Standard head protection
45.5 The employer shall ensure that a worker on a worksite or at any other place of employment who is exposed to a hazard, which could injure the head, wears head protection appropriate to the hazard and which meets the requirements of CSA Standard Z94.1 , Industrial Protective Headwear - Performance, Selection, Care and Use.
[EC2021-126, ss. 3, 41]
Section 45.6 Chin straps
45.6 Chin straps or other effective means of ensuring retention of safety headgear shall be fitted and worn when workers are exposed to high winds or other conditions which might cause the loss of the headgear.
[EC2021-126, s. 3]
Section 45.7 Standard eye protection
45.7 The employer shall ensure that a worker exposed to a hazard which could irritate or injure the eyes or face wears protection appropriate to the hazard and which meets the standards and specifications of the CSA Standard Z94.3-15 , Eye and Face Protectors or a standard offering equivalent protection.
[EC2021-126, ss. 3, 42]
Section 45.8 Obligation of employer
45.8 The employer shall ensure that a worker who has 20/200 vision in either eye, or is blind in either eye, wears eye protection as required by section 45.7.
[EC2021-126, s. 3]
Section 45.9 Contact lenses
45.9 When a worker intends to wear contact lenses at his place of employment, he shall immediately notify the employer.
[EC2021-126, s. 3]
Section 45.10 Contact lenses
45.10 The employer shall ensure that no worker shall wear contact lenses where
(a) gases, vapours or other materials are present which when absorbed by contact lenses may harm the eyes; or
(b) dusts or other materials are present which may harm the eyes or cause distraction which may expose the worker to other injury.
[EC2021-126, s. 3]
Section 45.11 Contact lenses
45.11 A worker shall not wear contact lenses while welding.
[EC2021-126, s. 3]
45.12 Repealed. [EC2007-652, s. 3]
Section 45.13 Hands
45.13 The employer shall ensure that all persons handling materials likely to puncture, abrade or irritate hands or arms, shall wear personal protective equipment to prevent such injuries, except when the use of this equipment introduces equal or greater hazards.
Section 45.14 Handling acids, etc.
45.14 The employer shall ensure that workers handling or using acids, caustics, steam, abrasives, hot fluid jets, or similar harmful substances, shall use suitable personal protective equipment, or other means shall be adopted that will provide protection against these hazards.
[EC2021-126, s. 3]
Section 45.15 Footwear
45.15 The employer shall ensure that a worker on a worksite or at any place of employment who is exposed to a hazard which could injure the foot wears footwear which meets the standards and specifications of CSA Standard Z195-14 Protective Footwear or a standard offering equivalent protection.
[EC2021-126, ss. 3, 43]
Section 45.16 Defective footwear
45.16 (1) Footwear that has deteriorated to a point where it does not provide the required protection shall not be used.
(2) When mobile equipment is fitted with foot operated controls the operator shall not wear footwear deemed by the officer to be unsafe.
(3) Section 45.15 does not apply when footguards or other devices affording equivalent protection are worn.
Section 45.17 Hazardous air
45.17 (1) Every employer shall ensure that when workers are or may be exposed to an oxygen deficient atmosphere or harmful concentrations of air contaminants, mechanical means of engineering design shall be utilized to prevent or to eliminate such hazardous conditions of exposure.
(2) Every employer shall ensure that where the prevention or elimination of such hazardous conditions is not reasonably practicable, or where the exposure results from temporary or emergency conditions only, every worker exposed shall wear approved protective respiratory equipment.
[EC2021-126, s. 3]
Section 45.18 Standards
45.18 (1) The employer shall ensure that the selection, use and care of respirators meet the applicable standards and specifications set out and referred to in the CSA Standard Z94.4-18 , "Selection, Use, and Care of Respirators
(2) The employer shall ensure that where air is provided for the purpose of any respiratory protective equipment, the air meets the applicable standards and specifications set out and referred to in the CSA Standard Z180.1-19 , Compressed Breathing Air and Systems.
(3) The employer shall ensure the selected respiratory protective equipment for filtering particulate matter meets the applicable standards and specifications set out in CSA Standard Z94.4.1:21 , "Performance of Filtering Respirators," or a standard offering equivalent protection.
[EC2020-147, s. 7; EC2021-126, ss. 3, 44; EC2024-600, s. 21]
Section 45.19 Shaving
45.19 Every employer shall ensure that workers required to use a respirator shall be clean shaven where the respirator seals with the face.
[EC2021-126, s. 3]
Section 45.20 Signs
45.20 (1) Every employer shall ensure that access routes to work areas where workers may be exposed to oxygen deficient atmosphere or harmful concentrations of air contaminants shall be posted with signs and specifying
(a) the required personal protective equipment; and
(b) the areas and hazards involved.
(2) The employer shall ensure
(a) that sufficient workers who are trained in rescue procedures are immediately available whenever workers are working in areas where an oxygen deficient atmosphere or harmful concentrations of air contaminants exist or are likely to develop; and
(b) that the rescue workers have immediate access to appropriate respirators or other aids necessary to effect a rescue.
(3) The employer shall ensure that where a worker is wearing an approved air-line or approved air-hose type respirator in an atmosphere immediately harmful to the worker
(a) the air supply source shall be attended by another worker who shall be equipped to effect rescue or render assistance if the worker is rendered unconscious or otherwise incapacitated; and
(b) the worker shall be provided with and carry an auxiliary supply of compressed respirable air of sufficient capacity to enable the worker to escape from the area in an emergency or until rescue is effected.
[EC2021-126, s. 3; EC2024-600, s. 22]
45.21 Repealed. [EC2004-632, s. 6]
45.22 - 45.23 Repealed. [EC2004-632, s. 7]
Part 49 ASBESTOS
Section 49.14 Respiratory protection
49.14 (1) An asbestos contractor shall provide, and ensure that workers use, within an asbestos work area, respirators which are appropriate for the level of risk of the anticipated exposure to asbestos fibres.
(2) An asbestos contractor shall ensure that the respirators provided to workers are selected, used, cleaned, stored, maintained, inspected and tested in accordance with the relevant provisions of CSA Standard Z94.4-18 , "Selection, Use, and Care of Respirators".
[EC596/90, s. 1; EC2020-147, s. 8]
Section 49.15 Asbestos work area, boundaries
49.15 (1) An asbestos contractor shall, prior to the commencement of asbestos work, ensure that
(a) the boundaries of the asbestos work area are identified and marked by barricades, fences or similar means;
(b) asbestos warning signs are posted at the boundaries of the asbestos work area which meet the requirements of clause 49.1(1)(e);
(c) the permit issued under subsection 49.10(3) is posted;
(d) the immediate work area is cleared of objects, materials and equipment other than those required to do the work; and
(e) the windows, doorways and all other openings are adequately secured to prevent the release of asbestos fibres into other work areas.
(2) No person shall eat, drink or smoke in an asbestos work area.
[EC596/90, s. 1; EC2020-147, s. 8]
Part 50 TRAFFIC CONTROL
Section 50.6 Equipment
50.6 The employer shall ensure that a signaller is equipped with such protective health and safety equipment and clothing as is required to ensure the health and safety of the signaller at the signaller's workplace, including any required safety footwear, hard hat, safety vest, eye protection and rain wear.
[EC225/91, s. 1]
- Asbestos - Developing a Respirator Program
- Farm Safety Code of Practice
- Guide for Employers of Young Workers
- Guide to Workplace Safety for Construction Sites
- Guide to Workplace Safety for Golf Courses and Grounds keeping
- Information on Workplace Health and Safety
- Rights & Responsibilities
- Solar Radiation