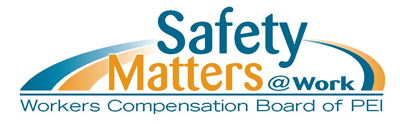


New Worker Safety Orientation
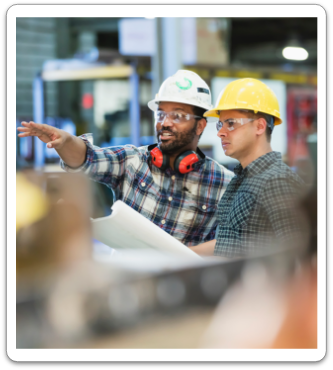
[OHS General Regs., S. x] Follow these links
to related legislation.
Highlighted words reveal
definitions and supplementary
information when selected.
Orientation is meant to help new and young workers integrate into their new work environment. Employers should share with the new worker their strong commitment to health and safety in the workplace and how their safety culture helps fulfill that commitment. Employers set clear expectations for safe behaviours and must make sure new workers understand all the procedures and policies related to the safe performance of their jobs.
Workers should receive hands-on instruction that is job specific. It is considered good practice for employers to provide this instruction individually or in small groups. Use demonstrations and make sure workers actively participate so that supervisors can confirm that the new workers fully understand the safe work procedures that they need to know.
It is also good practice for new worker orientation sessions to cover issues such as the location of hazards, the first aid kit, and any necessary communication equipment.
Employer duties
Employers must make sure that new workers are given the information, instruction, and training that will allow them to work safely. [OHS Act, S. 12 (c)]
Employers must make sure all new workers are familiar with:
- the occupational health or safety hazards at the workplace; and
- how to use of the required safety features or devices, equipment and clothing that is required for their protection. [OHS Act, S. 12 (d) (e)]
Employers regularly employing 20 or more workers must have an occupational health and safety program. Review the occupational health and safety program extensively throughout the orientation and cover occupational health and safety issues that concern all workers, as well as people at and near the workplace. [OHS Act, S. 23 (3)(a)]
An occupational health and safety program must:
- be written down;
- identify the types of work that may require health and safety procedures;
- include occupational health and safety work practices and how they will be implemented; and include procedures for training workers in relevant occupational health and safety issues. [OHS Act, S. 23 (3)]
Required Training
The OHS Regulations outline specific safety training that may apply in certain situations.
Noise
- A noise control and hearing conservation program is required when it is not practical to reduce noise levels to safe levels. A noise control program must include worker education and training related to noise hazards and hearing protection. [OHS General Regs., S. 8.8 (b)] Keep records of all education and training provided to workers. [OHS General Regs., S. 8.10 (b)]
- If new workers are going to be exposed to noise hazards that exceed the established limits, employers must provide them with training on how to use and care for hearing protection equipment, and how to maintain their hearing protection so that remains effective and meets the requirements of CSA Standard Z94.2-02, Hearing Protection Devices - Performance, Selection, Care, and Use (as amended). [OHS General Regs., S. 8.7(1)]
See the noise topic for more information.
Confined space entry and rescue
- Employers must make sure that all workers entering a confined space and those stationed outside it are trained in emergency procedures. This training must specifically address the factors related to confined spaces. [OHS General Regs., S. 13.2 (f)]
- Employers must make sure the worker stationed outside the confined space (the sentinel) understands the emergency rescue procedures, and is able to use the required equipment.[OHS General Regs., S. 13.5 (e)]
See the confined spaces topic for more information.
Using hand tools
- Employers must make sure workers are properly trained to use their hand tools safely. [OHS General Regs., S. 29.3 (b)]
- Instruct workers to use tools only for their intended purpose according to their design. [OHS General Regs., S. 29.3 (c)]
Lockout procedures
- The employer is responsible for adequately training new workers in lockout procedures that are relevant for the situation at hand. [OHS General Regs., S. 30.6 (3)]
Powered mobile equipment
- Employers must make sure that only competent workers operate power mobile equipment. New employees assigned to operate power mobile equipment must be able to do so safely. [OHS General Regs., S. 33.13]
See the powered mobile equipment topic for more information.
Electrical hazards
- Employers must make sure that workers working around electrical hazards are competent to do their work safely or are working under the direct supervision of a person who is competent. [OHS General Regs., S. 36.2]
- Those persons working around electrical hazards in communications or on other types of work (that does not require any licencing or certification) must have the demonstrated understanding, training, and experience to perform their assigned work safely. [OHS General Regs., S. 36.1]
See the Electricity topic for more information.
Material handling
- The employer is responsible for making sure each new worker receives individual instruction on how to lift and carry material. Instruction should focus on what is relevant for their position. Employers must consider the physical condition of the worker including their sex and age if that is relevant. [OHS General Regs., S. 43.8]
Personal protective equipment (PPE)
- Before beginning work on a job that will require workers to use PPE, employers must make sure the workers are trained about how to use and maintain their PPE correctly, and understand its limitations. [OHS General Regs., S. 45.3]
See the Personal protective equipment topic for more information.
Working alone
- When a workplace has employees who are working alone, employers must have a training program so that the workers understand all related procedures. This training must include those supervisors who are responsible for the worker who is working alone. [OHS General Regs., S. 53.4]
See the Working Alone topic for more information.
Fall protection
- Employers must make sure that all workers who use personal fall protection equipment are trained by a competent person about in the use, care and inspection of the fall arrest system, and a review all Prince Edward Island fall protection regulations and requirements. [Fall Protection Regs., S. 2.1]
See the Fall Protection topic for more information.
Traffic control signaling
- When assigning workers to work as signallers, the employer must make sure the signaller is competent, as well as can meet other conditions. [OHS General Regs., S. 50.4]
See the Traffic topic for more information.
Workplace Hazardous Materials Information System Regulations (WHMIS)
- Employers must inform all workers who work with or may be exposed to a hazardous product about the information received from the supplier, and any other information about the hazards of that product [WHMIS Reg., S. 4]
See the WHMIS topic for more information.
(i) is qualified because of that person's knowledge, training and experience to do the assigned work in a manner that will ensure the health and safety of persons in the workplace, and
(ii) is knowledgeable about the provisions of the Act and the regulations that apply to the assigned work, and about potential or actual danger to health or safety associated with the assigned work.
Fall Protection Regulations
EC2004-633
PART 2 - GENERAL REQUIREMENTS
Section 2.1 Required training in use of a means of fall protection
2.1 (1) Where, in accordance with subsection 2(1) or (4), an employer of a worker provides the worker with a means of fall protection for use at a work area, the employer shall ensure the worker is trained in the use of the means of fall protection by a competent person and that the training includes
(a) training in the use, care and inspection of the means of fall protection; and
(b) a review of the provisions of these regulations that apply to the means of fall protection.
(2) An employer shall
(a) maintain a training record for each worker during, and for a period of two years following, the worker's employment with the employer; and
(b) make the record available to an officer upon the officer's request.
(3) A training record referred to in subsection (2) shall include
(a) the name of the worker who received the training;
(b) the date on which the training took place;
(c) the name of the competent person providing the training; and
(d) any training material provided to the worker.
[EC2012-304, s. 1]
General Regulations
EC180/87
Part 8 NOISE
Section 8.7 Reduction of noise exposure, signs
8.7 (1) If it is not practicable for an employer to reduce the noise exposure of a worker of the employer at the workplace to or below any noise exposure limit, the employer shall
(a) reduce the noise exposure of the worker to the lowest level practicable;
(b) establish a noise control and hearing conservation program that complies with the requirements of section 8.8;
(c) post warning signs in the noise hazard areas;
(d) give to affected workers hearing protection that meets the requirements of CSA Standard Z94.2-14, Hearing Protection Devices - Performance, Selection, Care, and Use , as amended from time to time, provide training to the affected workers in the use and care of the hearing protection and maintain the hearing protection so that it continues to meet those requirements; and
(e) ensure that hearing protection required by clause (d), is worn properly by workers of the employer in noise hazard areas.
(2) Every worker in a posted noise hazard area shall wear hearing protection.
[EC2007-652, s. 1; EC2021-126, s. 9]
Section 8.8 Program - requirement
8.8 A noise control and hearing conservation program required under subsection 8.7(1) shall include provisions on
(a) noise measurement;
(b) education and training;
(c) engineered noise control;
(d) hearing protection;
(e) posting of noise hazard areas;
(f) hearing tests; and
(g) annual program review.
[EC2007-652, s. 1]
Section 8.10 Records
8.10 The employer shall keep records of
(a) the initial and annual hearing test results for each worker, which shall
(i) be kept as long as the worker is employed by the employer, and
(ii) be kept confidential and not released to anyone without the written permission of the worker, or as otherwise required by law;
(b) the education and training provided to workers; and
(c) the results of noise exposure measurements taken under section 8.4.
[EC2007-652, s. 1]
Part 13 CONFINED SPACE
Section 13.2 Conditions for entry of confined space
13.2 The employer shall ensure that a worker enters a confined space only where
(a) there is a safe method of access and egress from all parts of the confined space;
(b) mechanical equipment in the confined space is
(i) disconnected from its power source, and
(ii) locked out;
(c) prior to entry
(i) piping containing hazardous substances or substances under pressure or so located as to allow hazardous substances to enter such space is disconnected, blanked or blinded off, or
(ii) where it is impossible to employ blanks or blinds, as in welded piping systems, written work procedures are developed in consultation with (the Division, committee, or representative) and implemented to ensure equivalent protection to all workers exposed to the hazard but the closing of a valve on any line is not an acceptable substitute for blanking or blinding;
(d) the confined space is tested and evaluated by a competent person, properly equipped with personal protective equipment, who
(i) used an approved calibrated instrument that has been functionally tested,
(ii) records the results of each test in a permanent record which is available to an officer,
(iii) certifies in writing in a permanent record that the confined space is free from hazard, and
(iv) specifies the procedures to be followed to ensure that the space remains free of hazard;
(e) ground fault circuit interrupters are used for electrical equipment taken into wet or solidly grounded confined spaces unless battery operated or safety low voltage equipment is used; and
(f) training in emergency procedures is provided for workers assigned to a confined space entry job including the worker stationed outside the confined space.
[EC2021-126, s. 3]
Section 13.5 Sentinels
13.5 The employer shall ensure that when a worker enters a confined space, another
(a) remains in attendance outside the space at all times whenever the space is occupied and visually checks or is in constant voice communication with the worker in the confined space;
(b) is capable of raising an alarm in order to summon additional assistance;
(c) does not enter the space unless relieved by another worker;
(d) ensures that appropriate equipment is stationed outside the space to enable quick and safe entry to the space, should such an entry be required; and
(e) is knowledgeable in the correct use of the emergency retrieval system procedures.
[EC2021-126, s. 3]
Part 29 HAND TOOLS AND PORTABLE POWER TOOLS
Section 29.3 Responsibilities of employer
29.3 The employer shall ensure that
(a) workers are competent in the safe handling and use of tools;
(b) workers shall be properly instructed and trained in the safe use of the hand tools they use;
(c) workers are instructed to use tools only for the specific purpose for which they are designed;
(d) workers wear and use protective clothing and equipment as required by these regulations;
(e) procedures are implemented for safely supplying tools and materials to workers located in hazardous places;
(f) hammers, sledges, cold chisels, cutters, pinchers and other similar shock tools are made of carefully selected steel, hard enough to withstand repeated blows without extensive mushrooming but not so hard as to chip or break;
(g) files are provided with substantial metal ferruled handles or other suitable holders and shall not be used without them;
(h) lifting jacks shall be of such construction that the load will remain supported in any position and cannot be lowered inadvertently;
(i) when lifting objects with jacks, the jacks shall be set on solid footing, properly centered for the lift and so placed that they can be operated without obstruction; and
(j) after objects have been raised to the desired height by means of jacks, substantial blocking shall be placed under the object before work is started on the object or before the worker gets under the object.
[EC2021-126, s. 3]
Part 30 MECHANICAL SAFETY
Section 30.6 Lock-out
30.6 (1) The employer shall ensure that in addition to the normal control start and stop switch, all electrically driven machinery and equipment has installed in the power supply circuit a disconnecting means which is
(a) of a lockable type;
(b) in a location familiar to all; and
(c) properly identified.
(2) The employer shall provide a safety lock and key for use on disconnecting means described in subsection (1) to all machinery and equipment operators and all maintenance personnel.
(3) The employer shall ensure that a worker has been adequately trained in lockout procedures for the particular situation.
(4) The employer shall ensure that machinery is not lubricated, cleaned, serviced or repaired while in motion unless a means is available which does not expose the worker to risk of injury.
[EC2021-126, s. 3]
Part 33 POWERED MOBILE EQUIPMENT
Section 33.13
33.13 The employer shall ensure that any person or worker does not work under or go under the raised parts of any powered mobile equipment unless the raised parts of the equipment are adequately blocked.
[EC2021-126, s. 29]
Part 36 ELECTRICITY
Section 36.1 Competent
36.1 (1) In this Part "competent" in relation to a person means,
(a) when applied to electrical installations, as defined under the Electrical Inspection Act R.S.P.E.I. 1974, Cap. E-2 and regulations, a person who is the holder of a subsisting license as issued under the Electrical Inspection Act;
(b) when applied to electrical utility linework, a person who is the holder of a subsisting Certificate of Qualification or a Certificate of Proficiency as issued by the Department for the construction or utility lineman trades;
(c) when applied to communications and any other types of work covered by this Part, a person who demonstrates to the Division that he is qualified by knowledge, training and experience to perform an assigned task safely.
(2) "de-energized" in the electrical sense means isolated and grounded.
Section 36.2 Worker qualifications
36.2 The employer shall ensure that a worker shall not work on any energized electrical conductor or equipment unless he is
(a) competent; or
(b) an indentured apprentice under the direct supervision of a competent person.
[EC2021-126, s. 3]
Part 43 HANDLING & STORAGE OF MATERIALS
Section 43.8 Handling materials
43.8 The employer shall ensure that
(a) where practicable, mechanical appliances shall be provided and used for lightening and carrying materials and articles;
(b) workers assigned to handle material shall be instructed how to lift and carry material on an individual basis, the overriding factor being the physical condition of each worker including sex and age when relevant;
(c) where heavy objects are lifted or carried by two or more workers, the raising and lowering of the loads shall be governed by well understood signals in order to ensure unity of action;
(d) where heavy objects, such as loaded drums or tanks, are handled on inclines in either direction
(i) ropes or other tackle shall be used to control their motion, in addition to the necessary chocks or wedges, and
(ii) workers shall be prohibited from standing between the skids on the downhill side;
(e) where heavy objects are moved by means of rollers, bars or sledges shall be used instead of hands or feet for changing the direction of the rollers while in motion;
(f) workers handling objects with sharp edges, fins, slivers, splinters or similar dangerous projecting parts, or handling hot, caustic or corrosive material, shall be provided with and shall use suitable protective clothing and equipment;
(g) unless specific instructions are given to the contrary, loaded boxes and crates shall be piled on the sides having largest area;
(h) the piles shall be effectively cross-tied by suitable means;
(i) loaded cartons shall not be piled to such a height as to cause collapse of the lower cartons in the pile and shall be protected against moisture;
(j) lumber stored in yards shall be piled on supports above the grounds, the horizontal or slightly inclined layers separated by tie pieces, the ends of which will not project into walkways;
(k) pipe and bar stock shall, where practicable, be piled on stable storage racks so located that the withdrawal of the material does not create a hazard;
(l) where empty barrels or drums, large pipe, rolls of paper or other cylindrical objects are piled on their sides, the piles shall be symmetrical and stable; and every unit in the bottom row shall be carefully wedged;
(m) where storage racks are not provided for pipe and bar stock, the stock shall be piled on layers resting on wood strips with stock blocks fixed on the ends or on metal bars with unturned end;
(n) where loaded barrels, drums or keys are piled on their ends, the piles should be low and two planks should be laid side by side on top of each row before another row is started;
(o) equipment or objects, such as foundry flasks, forging dies, foundry castings and the like, shall be piled in a stable, orderly way on level and substantial foundation and arranged in order of size and type.
[EC2021-126, s. 3]
Part 45 PERSONAL PROTECTIVE EQUIPMENT
Section 45.3 Instruction
45.3 Every employer shall ensure that every worker who is required to use personal protective equipment shall be given pre-job instruction by the employer to understand its use, its limitations, and its maintenance requirements, as far as these relate to its correct use by the worker.
[EC2021-126, s. 3]
Part 50 TRAFFIC CONTROL
Section 50.4 Qualifications
50.4 The employer shall ensure that signallers
(a) are competent persons over the age of sixteen years who have been trained in, and have demonstrated an adequate knowledge of traffic control and signalling procedures;
(b) have such training as the Director may require;
(c) have a thorough knowledge of the regulations contained in this Part;
(d) are in good physical and mental condition;
(e) have adequate eyesight and hearing to carry out their duties;
(f) hold a certificate of training and shall produce proof of training at the request of an officer.
[EC225/91, s. 1]
Part 53 WORKING ALONE
Section 53.4 Training program
53.4 The employer shall implement a training program in respect of the procedures established under section 53.2 for each worker who is working alone and for each supervisor who is responsible for a worker working alone.
[EC2006-43, s. 5]
OCCUPATIONAL HEALTH AND SAFETY ACT
R.S.P.E.I. 1988, c. O-1.01
Section 12 Duties of employers
12. (1) An employer shall ensure
(a) that every reasonable precaution is taken to protect the occupational health and safety of persons at or near the workplace;
(b) that any item, device, material, equipment or machinery provided for the use of workers at a workplace is properly maintained, and is properly equipped with the safety features or devices, as recommended by the manufacturer or required by the regulations;
(c) that such information, instruction, training, supervision and facilities are provided as are necessary to ensure the occupational health and safety of the workers;
(d) that workers and supervisors are familiar with occupational health or safety hazards at the workplace;
(e) that workers are made familiar with the proper use of all safety features or devices, equipment and clothing required for their protection; and
(f) that the employer's undertaking is conducted so that workers are not exposed to occupational health or safety hazards as a result of the undertaking.
(2) An employer shall
(a) consult and cooperate with the joint occupational health and safety committee or the representative, as applicable;
(b) cooperate with any person performing a duty or exercising a power conferred by this Act or the regulations;
(c) provide such additional training of committee members as may be prescribed by the regulations;
(d) comply with this Act and the regulations and ensure that workers at the workplace comply with this Act and the regulations; and
(e) where an occupational health and safety policy or occupational health and safety program is required under this Act, establish the policy or program.
(3) An employer shall establish and implement as a policy, in accordance with the regulations, measures to prevent and investigate occurrences of harassment in the workplace.
[S.P.E.I. 2018, c. 45, s. 3]
Section 23 Occupational health and safety program
23. (1) Where 20 or more workers are regularly employed
(a) by an employer other than a constructor or contractor; or
(b) directly by a constructor or contractor,
the employer, constructor or contractor shall establish, and review at least annually, a written occupational health and safety program, in consultation with the committee or representative, if any.
(2) For the purposes of subsection (1), a worker is not regularly employed directly by a constructor or contractor if the worker works with the constructor or contractor as an independent contractor.
(3) An occupational health and safety program shall include
(a) provisions for the training and supervision of workers in matters necessary to their occupational health and safety and the occupational health and safety of other persons at or near the workplace;
(b) provisions for
(i) the preparation of written work procedures for the implementation of occupational health and safety work practices, required by this Act, the regulations or by order of an officer, and
(ii) the identification of the types of work for which the procedures are required at the employer's workplace;
(c) provisions for the establishment and continued operation of a committee required by this Act, including maintenance of records of membership, rules of procedure, access to a level of management with authority to resolve occupational health and safety matters, and information required by this Act or the regulations;
(d) provisions for the selection and functions of a representative where required by this Act, including provision for access by the representative to a level of management with authority to resolve occupational health and safety matters;
(e) a hazard identification system that includes
(i) evaluation of the workplace to identify potential hazards,
(ii) procedures and schedules for regular inspections,
(iii) procedures for ensuring the reporting of hazards and the accountability of persons responsible for the correction of hazards, and
(iv) identification of the circumstances where hazards shall be reported by the employer to the committee or representative, if any, and the procedures for doing so;
(f) a system for workplace occupational health and safety monitoring, prompt follow-up and control of identified hazards;
(g) a system for the prompt investigation of hazardous occurrences to determine their causes and the actions needed to prevent recurrences;
(h) the maintenance of records and statistics, including reports of occupational health and safety inspections and investigations, with provision for making the reports available to persons entitled to receive them under this Act; and
(i) provisions for monitoring the implementation and effectiveness of the program.
(4) The employer shall make a copy of the program established under this section available
(a) to the committee or representative, if any; and
(b) on request, to a worker at the workplace.
(5) The results of a workplace harassment investigation do not constitute a report for the purposes of clause (3)(h).
[S.P.E.I. 2018, c. 45, s. 5]
Workplace Hazardous Materials Information System Regulations
EC2017-455
WORKER EDUCATION AND TRAINING
Section 4 Hazard information to be supplied to employee
4. An employer shall ensure that a worker who works with a hazardous product or may be exposed to a hazardous product in the course of the worker’s work activities is informed about all hazard information received from a supplier concerning that hazardous product, if applicable, and any other hazard information the employer is aware of, or ought to be aware of, concerning that hazardous product.