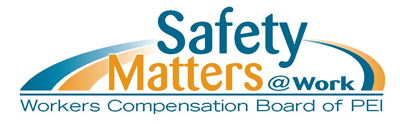


Guardrails
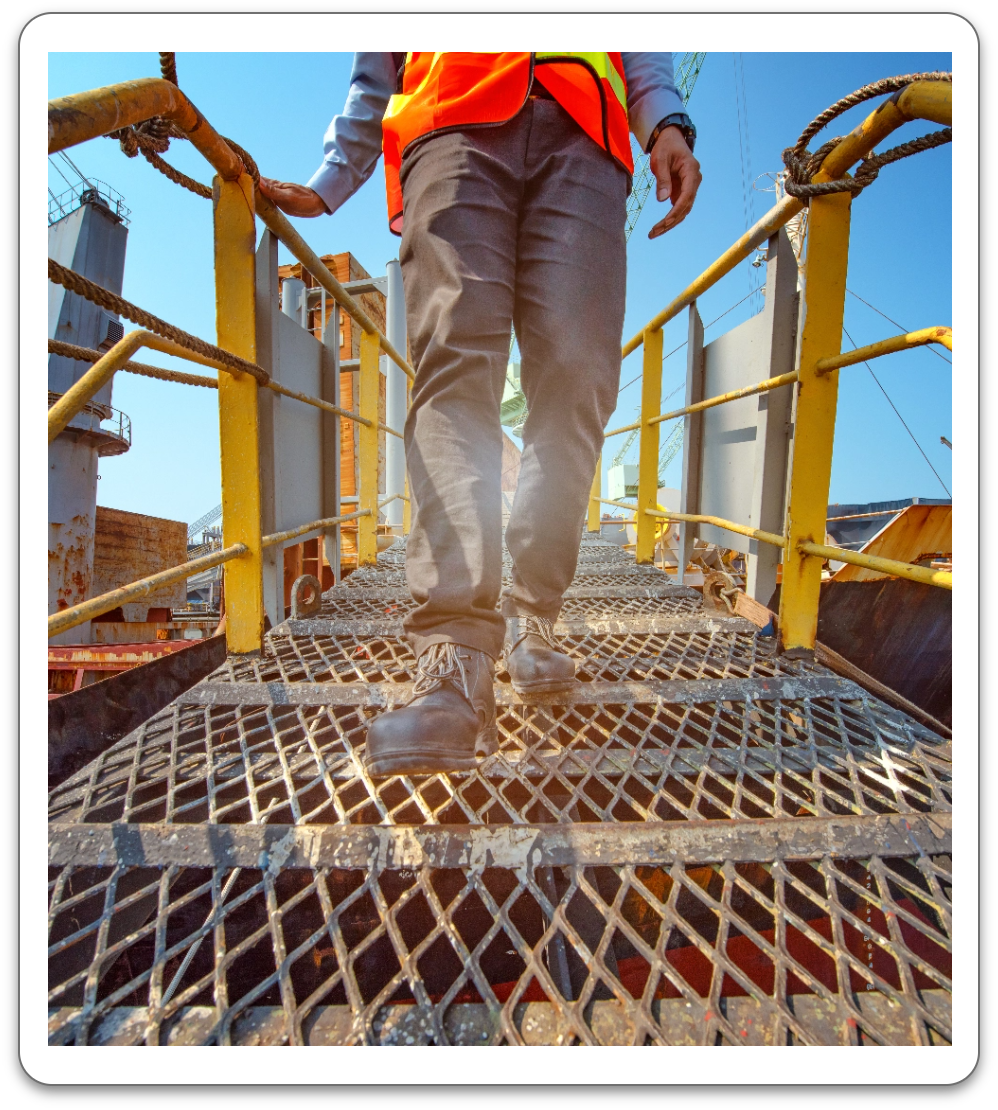
[OHS General Regs., S. x] Follow these links
to related legislation.
Highlighted words reveal
definitions and supplementary
information when selected.
Guardrails are a stationary (or "fixed") system used to protect workers from falls when working at heights. Guardrails are a preferred means of protecting workers because the system does not rely on the worker to be trained to use, inspect, and wear a fall protection system.
Well-built guardrails are a reliable and convenient means of fall protection because they act as a visible and physical barrier to help prevent falls from heights or between levels, including falls from roofs, balconies, stairwells, or falls into open holes. Guardrails are used where covers, floors, or walls cannot be installed or are not practical.
Employer duties
Employers have a duty to take every reasonable precaution to protect the occupational health and safety of persons at or near the workplace. This duty includes that workers are made familiar with the proper use of all safety features or devices, equipment, and clothing required for their protection. [OHS Act, S. 12(1)(a)(b)(e)]
To reduce exposure to falls, the employer should:
- Identify risk factors in the workplace in consultation with the Joint Occupational Health and Safety Committee or Health and Safety Representative as applicable.
- Evaluate the risk to workers by consulting with employees affected and those who do similar work.
- Ensure that employees are competent and trained to identify risk factors including the early signs and symptoms of injuries and the correct use of control measures when working with conveyors.
- Post warning signs in the hazard areas.
- Put safe work procedures in place.
- Monitor the effectiveness of control measures.
Employers must specifically make sure that:
- Runways, ramps, or platforms (other than a scaffold platform) have a guardrail on the open side or sides. [OHS General Regs., S.21.4]
- Stairs have a handrail or guardrail that is secure and supported on the open side or sides of each flight and at each landing. [OHS General Regs., S. 22.5(b)]
- Pile driving equipment has decks and working areas around the pile-driver that have a guardrail and are kept clear of ropes, tools, and other materials. [OHS General Regs., S. 32.1(b)]
- Safety measures are in place to protect a worker from falling into water including (but not limited to) a guardrail or safety net that are installed and used according to the Fall Protection Regulations. [OHS General Regs., S. 45.4.1(2)]
- A forklift platform is equipped with guardrails. [Scaffolding Regs., S.17(2)(b)]
Employers must make sure that guardrails extend around areas such as an uncovered opening in a floor, mezzanine, balcony, or other surfaces. The guardrails must: [Fall Protection Regs., S. 4(1)]
- Have posts that are not more than 2.4 m.
- Be secured against movement.
- Have a top railing that is between 0.91 m and 1.06 m above the surface.
- Have a toe board that extends from the base of the posts to a height of 102 mm.
- Have an intermediate railing on the inner side of the posts midway between the top railing and the toe board.
If the guardrails are made from wood, they must meet the requirements above, and: [Fall Protection Regs., S. 4(2)]
- Have a top and immediate railing and posts that are at least 51 mm by 101 mm.
- Have a toe board that is at least 25 mm by 75 mm.
- Be made of Grade Two or better spruce or equivalent.
If the guardrail has wire rope railings, it must meet the general requirements above, and: [Fall Protection Regs., S. 4(3)]
- Have top and immediate railings that are at least 8 mm in diameter.
- Be identified with high visibility markings that are placed every 1.5 m on the top railing.
- Have a turnbuckle or similar on the top and immediate railings to maintain adequate tension.
The employer can have a manufactured guardrail installed or constructed at the work area if it provides an equivalent level of protection as the wood guardrail. [Fall Protection Regs., S. 4(4)]
Where there is an opening in a building shaft, and an employer is required by the regulation to have a guardrail constructed or installed at the work site, the employer must make sure that the guardrail is marked with a warning sign that indicates the presence of an open building shaft. [Fall protection Regs., S.5]
Worker duties
Workers are responsible for:
- Working safely and following health and safety rules.
- Participating in all training so they have a full understanding of the need for their PPE and how to use it safely.
- Properly and consistently wearing required PPE.
- Following all instructions, safe work practices and procedures, in the safe handling of the equipment.
- Participating in training, or hazard assessments, where appropriate.
- Reporting any hazard to the supervisor or employer.
- Using the equipment in a safe manner for the purpose for which it was designed.
Fall Protection Regulations
EC2004-633
PART 4 - GUARDRAILS
Section 4 Construction and installation requirements
4. (1) A guardrail that is constructed or installed at a work area, in accordance with subsection 2(1), shall
(a) extend around
(i) any uncovered opening in a floor or other surface, and
(ii) the perimeter or other open side of a floor, mezzanine, balcony or other surface, at the work area from which a worker may be exposed to the hazards of a fall described in clauses 2(1)(a) to (c);
(b) have posts that
(i) are spaced at intervals of not more than 2.4 m; and
(ii) are secured against movement by the attachment of the posts to the structure under construction or that is otherwise being worked on, or by another means that provides an equivalent level of safety;
(c) have a top railing that is between 0.91 and 1.06 m above the surface of the protected working area and that is securely fastened to posts secured in compliance with subclause (b)(ii);
(d) have a toeboard, securely attached to the posts and the structure to which the posts are secured, extending from the base of the posts to a height of 102 mm; and
(e) have an intermediate railing on the inner side of the posts midway between the top railing and the toeboard.
(2) Where a wooden guardrail is constructed or installed at a work area, the guardrail shall, in addition to the requirements of subsection (1),
(a) have top and intermediate railings and posts that are at least 51 mm by 102 mm;
(b) have a toeboard that is at least 25 mm by 75 mm; and
(c) be made of
(i) Grade Two or better spruce, or
(ii) other lumber that provides an equivalent level of safety to the type of lumber referred to in subclause (i).
(3) Where a guardrail that is constructed or installed at a work area has wire rope railings, the guardrail shall, in addition to the requirements of subsection (1),
(a) have top and intermediate railings that are at least 8 mm in diameter;
(b) be identified with high visibility markings placed every 1.5 m on the top railing; and
(c) have top and intermediate railings that are equipped with turnbuckles or other means that provide adequate tension to ensure an equivalent level of protection to that provided by the wooden railings required under subsection (2).
(4) Notwithstanding anything to the contrary in subsection (1), an employer may have a manufactured guardrail installed or constructed at a work area if it provides an equivalent level of protection to that provided by a wooden guardrail that complies with the requirements of subsections (1) and (2).
[EC2021-125, s. 3]
Section 5 Building shafts
5. Where, at a work area,
(a) there is no work platform installed at the level of a doorway or opening in a building shaft; and
(b) the employer is required by these regulations to have a guardrail constructed or installed at the work area,
the employer shall ensure that the guardrail is marked with a warning sign that indicates the presence of an open building shaft.
General Regulations
EC180/87
Part 21 PLATFORMS, RUNWAYS AND RAMPS
Section 21.4 Guardrail
21.4 A runway, ramp or platform other than a scaffold platform shall have a guardrail on the open side or sides.
Part 22 STAIRS
Section 22.5 Requirements
22.5 The employer shall ensure stairs and landings shall be designed and constructed to safely support a live load of 4.8 kPa with a safety factor of 4 and shall
(a) have a vertical distance between landings not exceeding 3.7 m and intermediate landings shall have a dimension of not less than 1100 mm measured in the direction of the run;
(b) have a handrail or guardrail securely fastened and supported in place on the open side or sides of each flight and at each landing.
[EC2024-600, s. 15]
Part 32 PILE DRIVING EQUIPMENT
Section 32.1 Pile driving equipment
32.1 The employer shall ensure that
(a) on steam or air-operated hammers of pile-drivers, the hoses shall be secured to prevent reaction hazardous to workers in case of a break of the hose or connections by placement of suitable safety straps across all couplings;
(b) decks and working areas around the pile-driver shall be provided with a guardrail and kept clear of ropes, tools and other materials;
(c) where piling is being hoisted in the leads, workers not engaged in the operation shall remain at a safe distance;
(d) pile-driver operators shall be responsible for ensuring that the suspended hammer is securely chocked when not in use and that on pile-drivers with swinging or suspended leads, the hammer shall not be raised until necessary;
(e) pile-heads shall be cut square, and shall be cleaned of debris, bark and slivers before being driven but only when the hammer is securely chocked;
(f) the exhaust of steam engines shall be arranged to discharge at a point where it will not interfere with the view of the engineer or work or injure workers nearby;
(g) hoisting-engines shall be covered with a suitable roof or shelter to eliminate hazards to the operator from falling objects and as a protection from the weather.
[EC2021-126, s. 3]
Part 45 PERSONAL PROTECTIVE EQUIPMENT
Section 45.4.1 Flotation device, when required
45.4.1 (1) An employer shall ensure that a worker who is employed under conditions that involve a risk of drowning is provided with and wears at all times a lifejacket or personal flotation device that is Flotation device, when required
(a) suitable to the conditions in the workplace; and
(b) of the correct size and appropriate for the weight of the worker who will wear it.
(2) Subsection (1) does not apply if
(a) other sufficient safety measures are in place to protect a worker from falling into water, including but not limited to a guardrail or safety net installed and used in accordance with the relevant requirements of Part 2 of the Fall Protection Regulations (EC633/04) made under the Act;
(b) the worker is a lifeguard on duty; or
(c) the worker is performing occupational diving tasks.
[EC2021-126, s. 40]
Scaffolding Regulations
EC2006-44
Section 17 Use of industrial lift truck
17. (1) An employer shall ensure that an industrial lift truck is not used to lift a fork-lift platform where
(a) the ground or other conditions at a workplace may affect the stability of the industrial lift truck; or
(b) the industrial lift truck is susceptible to tipping, displacement or other destabilization.
(2) An employer shall ensure that a fork-lift platform is
(a) erected, used, maintained and dismantled in accordance with
(i) the manufacturer's specifications, or
(ii) a professional engineer's design that includes instructions on erection, use, maintenance and dismantlement;
(b) equipped with guardrails;
(c) securely attached to an industrial lift truck during use;
(d) operated at all times by a competent person, who shall be continuously at the controls where the platform is in an elevated position; and
(e) used only where a firm, flat surface ensures the stability of the industrial lift truck, unless otherwise specified by the manufacturer.
(3) While a worker is working on a fork-lift platform, the employer of the worker shall ensure that the worker is wearing a fall arrest system and that the fall arrest system is attached to an anchor point on the platform.
(4) An employer shall ensure that an industrial lift truck complies with CSA Standard B335-15 , "Safety standard for lift trucks".
(5) Where
(a) a fork-lift platform is in an elevated position; and
(b) a worker is on the platform,
the employer of the worker shall ensure the industrial lift truck supporting the work platform is not moved horizontally.
[EC2017-605, s. 1]
OCCUPATIONAL HEALTH AND SAFETY ACT
R.S.P.E.I. 1988, c. O-1.01
Section 12 Duties of employers
12. (1) An employer shall ensure
(a) that every reasonable precaution is taken to protect the occupational health and safety of persons at or near the workplace;
(b) that any item, device, material, equipment or machinery provided for the use of workers at a workplace is properly maintained, and is properly equipped with the safety features or devices, as recommended by the manufacturer or required by the regulations;
(c) that such information, instruction, training, supervision and facilities are provided as are necessary to ensure the occupational health and safety of the workers;
(d) that workers and supervisors are familiar with occupational health or safety hazards at the workplace;
(e) that workers are made familiar with the proper use of all safety features or devices, equipment and clothing required for their protection; and
(f) that the employer's undertaking is conducted so that workers are not exposed to occupational health or safety hazards as a result of the undertaking.
(2) An employer shall
(a) consult and cooperate with the joint occupational health and safety committee or the representative, as applicable;
(b) cooperate with any person performing a duty or exercising a power conferred by this Act or the regulations;
(c) provide such additional training of committee members as may be prescribed by the regulations;
(d) comply with this Act and the regulations and ensure that workers at the workplace comply with this Act and the regulations; and
(e) where an occupational health and safety policy or occupational health and safety program is required under this Act, establish the policy or program.
(3) An employer shall establish and implement as a policy, in accordance with the regulations, measures to prevent and investigate occurrences of harassment in the workplace.
[S.P.E.I. 2018, c. 45, s. 3]